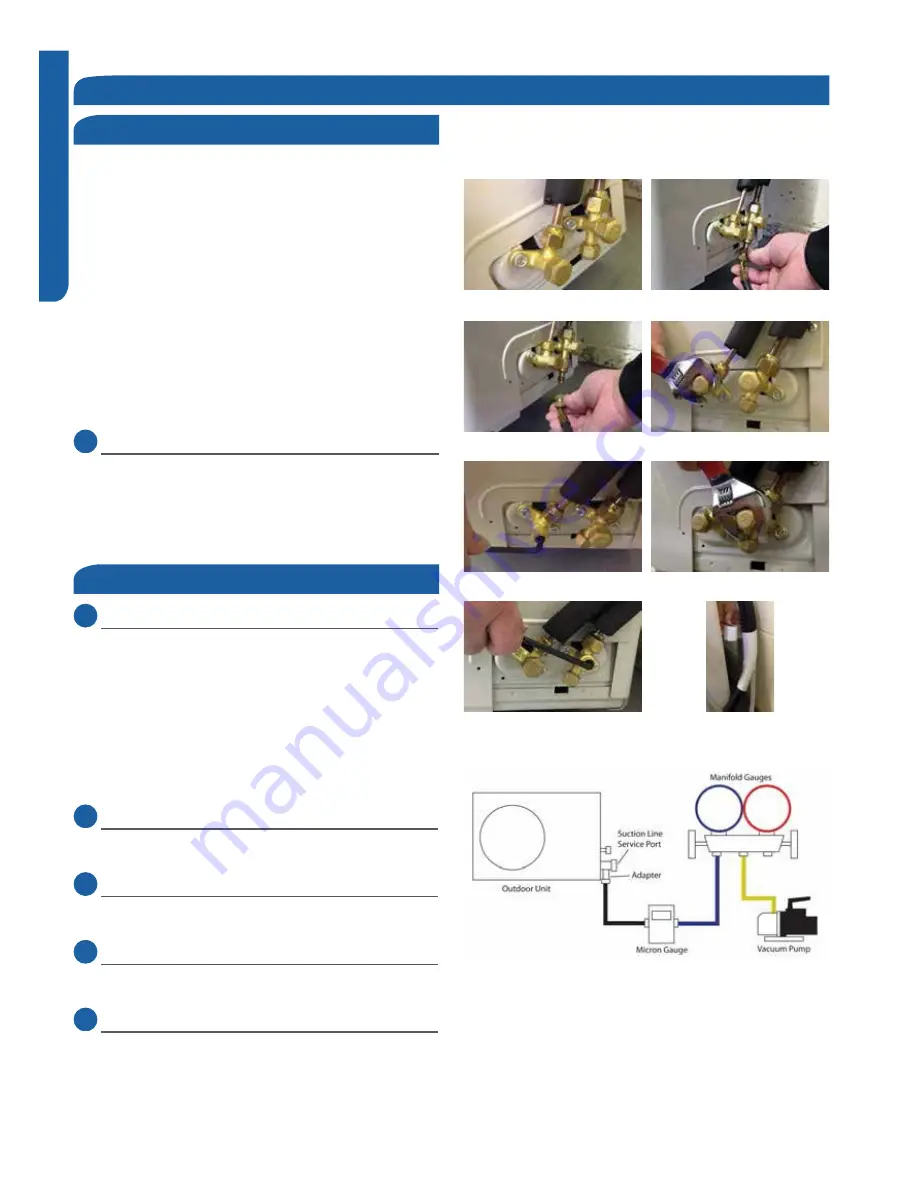
INSTALLATION
PAGE 6
ENGLISH
* $<B /3 Y *
leaks. Explosive conditions may occur. Use a leak test solution
or other approved methods for leak testing. Failure to follow
recommended safe leak test procedures could result In death
A A*;
Use only dry nitrogen with a pressure regulator for
pressurizing unit. Do not use acetylene, oxygen or
compressed air or mixtures containing them for pressure
testing. Do not use mixtures of a hydrogen containing
refrigerant and air above atmospheric pressure for pressure
AA" Y"* *
an explosion. Refrigerant, when used as a trace gas should
only be mixed with dry nitrogen for pressurizing units. Failure
to follow these recommendations could result in death or
A A*;
5.1
Step - 5.1
Using a tank of nitrogen with attached regulator, charge the
system with 150 PSIG of dry nitrogen. Use adapter AD-87
+]**. 33;7#$ #
Y] """ * *;
If a leak is detected, repair and recheck. If no leaks are
detected, proceed to evacuate the system.
Step 5.1
Step 5.3
Step 5.2
Step 5.4A
Step 5.5A
Step 5.6
Step 5.4B
Step 5.5B
Illustration 5
Leak Test
System Evacuation
Step 5 - Leak Test and Evacuation
5.2
Step - 5.2
Attach a manifold gauge, micron gauge, and vacuum pump
*&'()+]**.;
(Illustration 5)
Evacuate the system to 350 microns.
Close the vacuum pump valve and check the micron
gauge. If the gauge rises above 500 microns in 60 seconds,
evacuation is incomplete or there is a leak in the system. If
the gauge does not rise above 500 microns in 60 seconds,
evacuation is complete.
5.3
Step - 5.3
Remove the adapter and hose connection from the suction
line port, and replace the cap.
5.4
Step - 5.4A & 5.4B
Remove the cap from the liquid line valve. Using the hex
wrench, open the valve, then replace and tighten the cap.
5.5
Step - 5.5A & 5.5B
Remove the cap from the suction line valve. Using the hex
wrench, open the valve, then replace and tighten the cap.
5.6
Step - 5.6
Wrap the lineset, drain line, and wiring starting at the bottom
of the bundle with an overlap type wrap, concluding at the