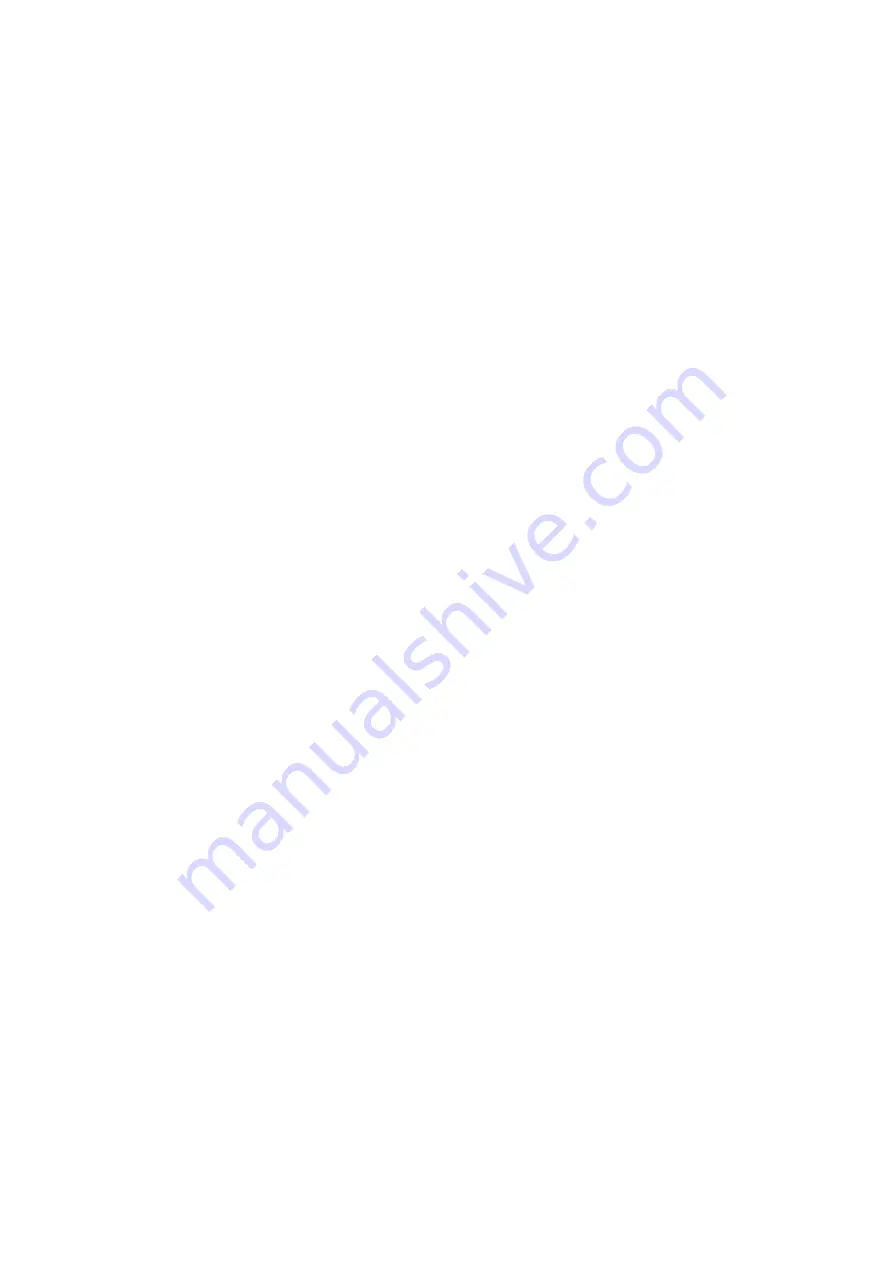
RE 15345-WA, Version 11.2022, Bosch Rexroth AB
Safety instructions |
Drive system Hägglunds Fusion 7/72
2 Safety instructions
2.1 About this chapter
This product has been manufactured in strict compliance with the generally
accepted rules of technology. However, this does not exclude the risk of damage
to persons or property if this chapter and the safety instructions included in the
present documentation are not observed.
f
Read this documentation carefully before starting to use the product.
f
Keep this documentation in a location where it is accessible to all users at any
time.
f
When providing the product to third parties, make sure to include the
necessary documentation.
2.2 Intended use
The Hägglunds Fusion is a hydraulic drive system.
In the application the Hägglunds Fusion drive system is classified as a partly
completed machinery in the sense of the EU machine directive 2006/42/EC,
Appendix IIB. A partly completed machinery is exclusively intended to form an
incomplete or a complete machine together with other components or partly
completed machineries. The drive system may only be commissioned after it has
been installed in the machine/system for which it is intended and the safety of the
entire system has been established in accordance with the machine directive.
Intended use includes having read and understood the complete documentation,
especially the chapter
.
The product is intended for the following use:
•
Closed loop hydraulic system to convert electric energy to mechanical rotation of
a shaft.
Special drive systems
Standard drive systems are not allowed to be used outside an ambient
temperature range of -20 °C to 40 °C (-4 °F to 104 °F), or in areas with potentially
explosive atmospheres.
Drive systems intended for use in ambient temperature below 0 °C (32 °F), can be
fitted with special optional equipment for preheating the hydraulic system before
start.
Observe the technical data, application and operating conditions and performance
limits as specified in the product-specific documentation and in the order
confirmation.