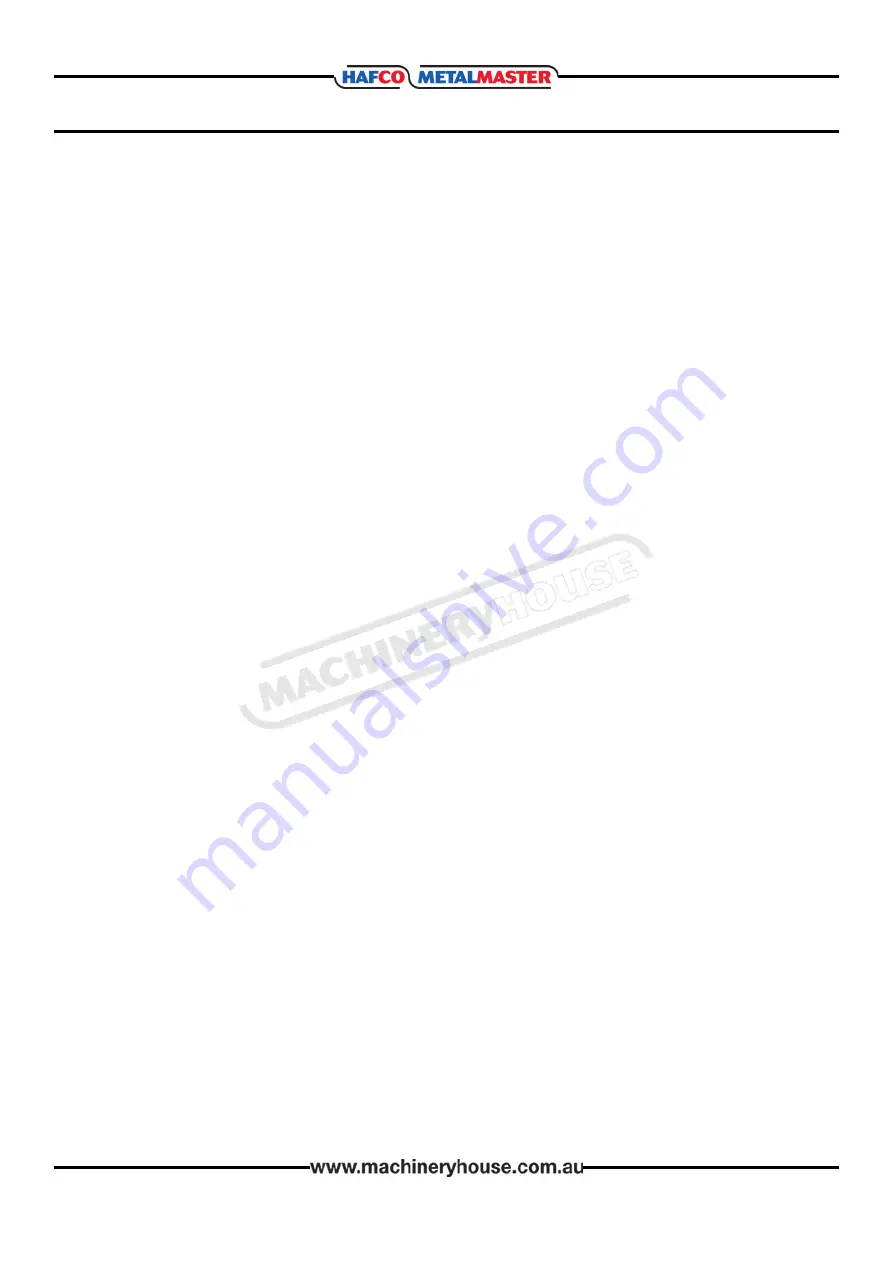
7
OPERATION MANUAL
WEARING PROPER APPAREL
Do not wear
clothing, apparel or jewelry that can become
entangled in moving parts. Always tie back
or cover long hair. Wear non-slip footwear to
avoid accidental slips, which could cause loss of
operating control.
HEARING PROTECTION
. Always wear hearing
protection when operating or observing loud
machinery. Extended exposure to this noise
without hearing protection can cause perma-
nent hearing loss.
REMOVE ADJUSTING TOOLS.
Tools left on
zzzzzzzzzzz can become dangerous projectiles
upon startup. Never leave hex keys, wrenches,
or any other tools on the machine. Always
verify removal before starting!
USE CORRECT TOOL FOR THE JOB.
Only use
this tool for its intended purpose. Do not force
the machine or its attachments to do a job for
which they were not designed. Never make
unapproved modifications. Modifying the ma-
chine or using it differently than intended may
result in malfunction or mechanical failure that
can lead to personal injury or death!
AWKWARD POSITIONS.
Keep proper footing
and balance at all times when operating ma-
chine. Do not overreach! Avoid awkward hand
positions that make operating control difficult.
This could increase the risk of accidental injury
GUARDS & COVERS.
Guards and covers reduce
accidental contact with moving parts or flying
debris. Make sure they are properly installed,
undamaged, and working correctly.
FORCING MACHINERY
. Do not force the ma-
chine. It will do the job safer and better at the
rate for which it was designed.
NEVER STAND ON MACHINE
. Serious injury
may occur if the machine is tipped or if the
cutting tool is unintentionally contacted
STABLE MACHINE
. Unexpected movement
during operation greatly increases risk of injury
or loss of control. Before starting, verify the
machine is stable and if using a mobile base it
is locked in position.
UNATTENDED OPERATION
. To reduce the
risk of accidental injury, turn the machine OFF
and ensure all moving parts have completely
stopped before walking away. Never leave the
machine running while unattended.
MAINTAIN WITH CARE
. Follow all maintenance
instructions and lubrication schedules to keep
the machine in good working condition. A
machine that is improperly maintained could
malfunction, leading to serious personal injury
or death.
CHECK DAMAGED PARTS
. Regularly inspect
the machine for any condition that may af-
fect the safe operation. Immediately repair or
replace damaged or parts that are incorrectly
fitted before operating.
CHILDREN & BYSTANDERS
. Keep children and
bystanders at a safe distance from the work
area. Stop using machine if they become a
distraction.
BLADE CONDITION.
Do not operate with dull,
cracked or badly worn blades. Inspect the
blades for broken teeth before each use.
2.1 SAFETY REQUIREMENTS Cont.
Page 7
Instruction Manual for EB-280DSV (B063V)
10/04/2019