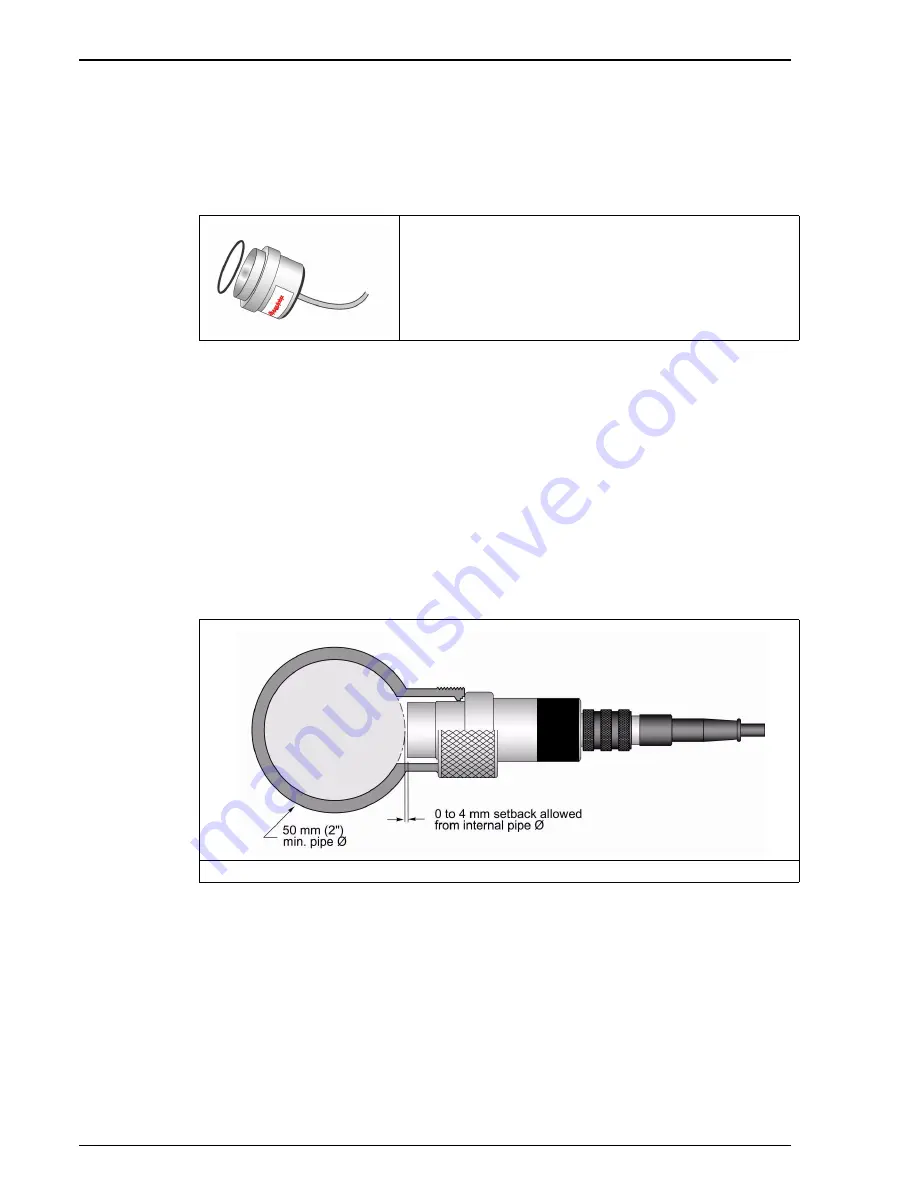
24
Installation
4.3 Mounting accessories
4.3.1 External pressure sensor
The system can be fitted with an external pressure sensor. This enables a measurement of
fraction of gas under variable pressure conditions during gas phase measurement.
Note:
Do NOT exceed the pressure range of the sensor. This would permanently deform the sensor
membrane, thus delivering incorrect pressure values in the future.
The external sensor connects to the ORBISPHERE measuring equipment with a 1 meter cable
and a 4 pin connector (an optional extension cable can be used, but total length should not
exceed 50 m.).
The external pressure sensor can be installed in the 32002.xxx multi parameter flow chamber. It
is held in place by a blue threaded collar. Tightness is assured by the O-ring on the sensor seat.
4.3.2 Weld-on stainless steel socket
The 29501 weld-on sensor socket can be used to install a sensor into a stainless steel pipe
(min.Ø 50 mm or 2”). When welding the socket to the pipe, check that setback between the
pipe’s inner diameter and the sensor tip does not exceed 4 mm (see diagram).
Note:
Be sure to remove the two O-rings from the socket before welding and leave the sensor’s stainless
steel cap screwed on during welding to prevent thread distortion.
Two models are available, depending on application:
•
28117 Pressure sensor 0 - 5 bar absolute
•
28117C Pressure sensor 0 - 1 bar absolute
Figure 8 Weld-on sensor socket