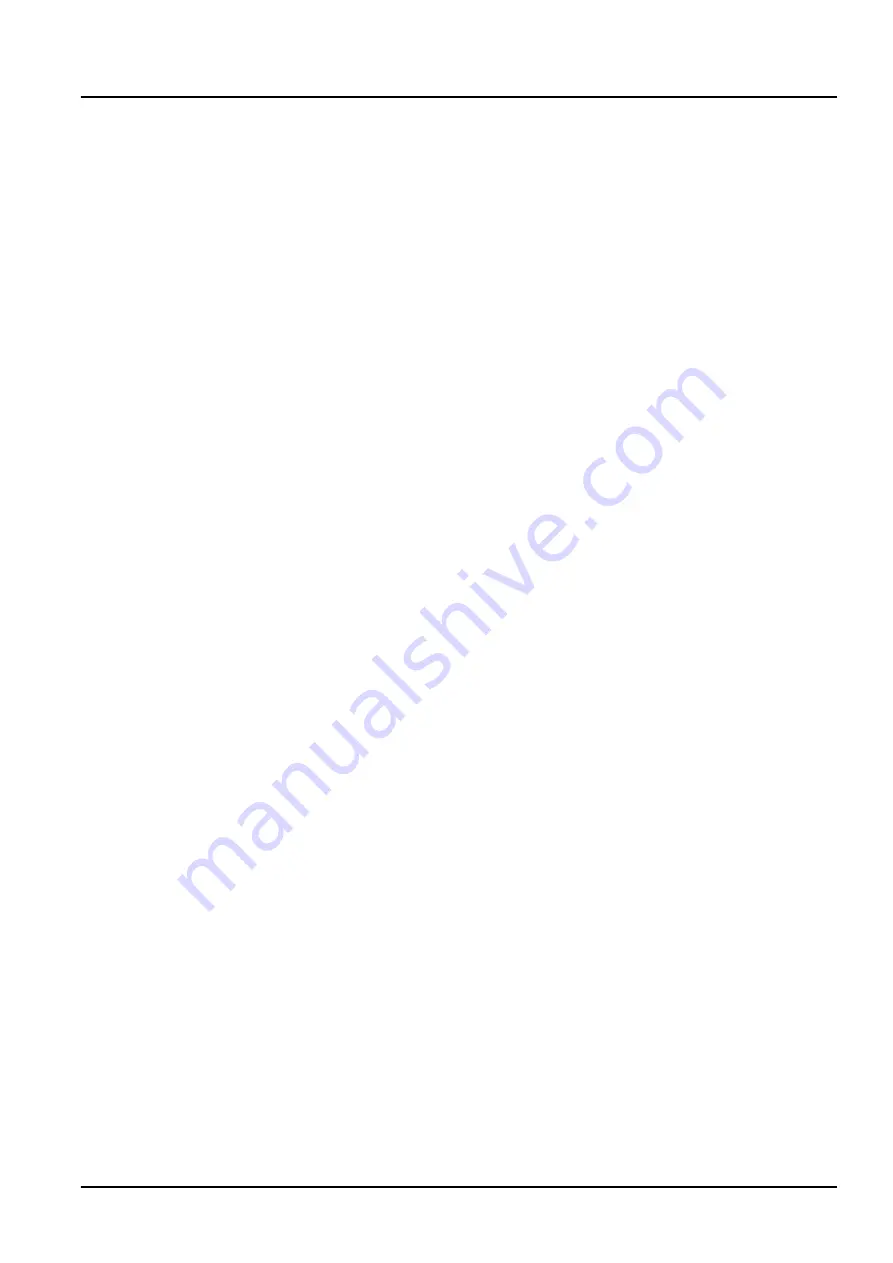
15
Section 3
Installation
DANGER
Only qualified personnel should conduct the tasks described
in this section of the manual.
The SS7 sc/sc controller product
configuration is not intended for installation in
hazardous locations.
The tasks described in this section requires individuals to be
technically knowledgeable of the associated dangers. Burns,
shock, eye damage, fire and chemical exposure may occur if this
work is not done by qualified personnel. Always review appropriate
Material Safety Data Sheets (MSDS) before working with
chemicals.
3.1 Basic installation overview
1.
Unpack the SS7 sc or SS7 sc-HST Turbidimeter (
section 3.2
).
2.
Review the environmental requirements and select the
mounting location (
section 3.3.2 on page 17
).
3.
Mount the sample unit (
section 3.3.3 on page 17
).
4.
Install the optional heat exchanger, if required (
section 3.3.4 on
page 19
).
5.
Install the 3-way ball valve, if required (
section 3.3.5 on
page 20
).
6.
Connect the sample in, body drain and overflow drain
(
section 3.5 on page 21
).
7.
Connect the air purge valve (
section 3.6 on page 24
).
8.
Connect the sample unit to the controller to supply power to the
system (
section 3.7.2 on page 24
).
3.2 Unpacking the instrument
1.
Remove the instrument from the shipping carton.
2.
Verify that no visible damage has occurred during shipment. Be
sure the following items are included in the carton:
•
Sample unit
•
Instruction manual
•
Installation kit items (
Figure 7
)
Contact the manufacturer immediately to report missing or
damaged items.
Summary of Contents for DOC026.52.00769
Page 2: ......
Page 4: ...Visit us at www hach com...
Page 10: ...Visit us at www hach com...
Page 30: ...Visit us at www hach com...
Page 54: ...Visit us at www hach com...
Page 60: ...Visit us at www hach com...
Page 62: ...Visit us at www hach com...
Page 63: ......
Page 64: ......