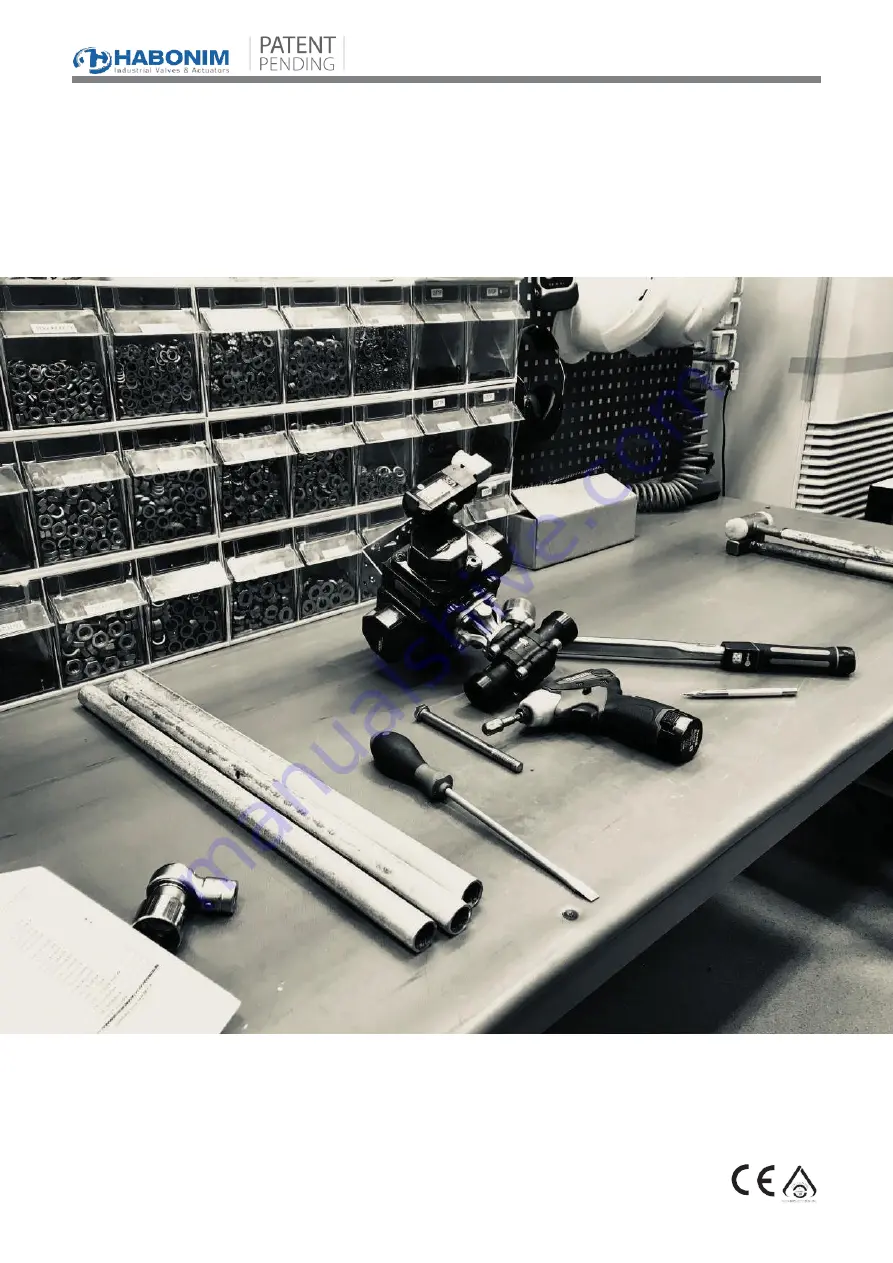
Top Entry Trunnion Mounted Cryogenic Ball Valves – C52
Valves Series
Installation, Operating & Maintenance
Top Entry Cryogenic Trunnion Ball Valves
C52 Valves Series
Habonim USA
Toll Free Phone: 1-866-261-8400
Toll Free Fax: 1-866-243-9959
[email protected]
Habonim EUROPE
Tel: +34 640 384 759
[email protected]
[email protected]
Habonim AUSTRALIA
Tel: +61 400 001 988
Habonim CHINA
Tel: + 86 21 64453190 *146
Habonim ISRAEL
Tel: +972-4-6914911
Fax: +972-4-6914935
Habonim UK
Tel: +44-1633-484554
Fax: +44-1633-482252
Habonim SINGAPORE
Tel: +65 6296 7828
Fax: +65 6299 3184
REV00-12/19