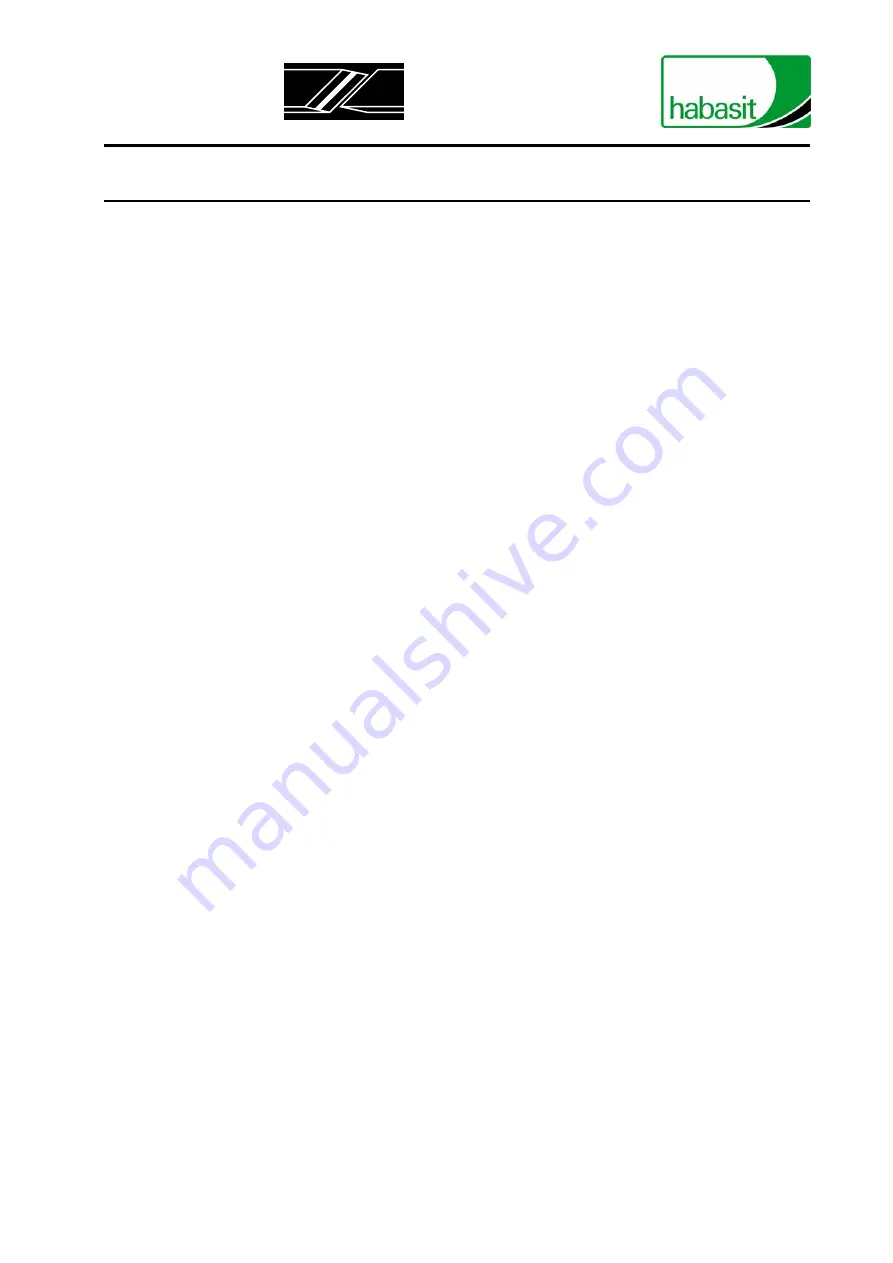
Habasit Italiana S.p.A.
Vittorio Veneto 31029 (TV)
Tel.: ++39(0)438.9113
Fax. ++39(0)438.200545
Skiving device AT-306
Author:
S.D.T. / KM
OPERATION
Edition: 02/2005
Page
D-4
Replaces: 01/2001
D.3
Start up
Turn the
main switch
[29] to ON and press the start push buttons for:
start
skiving roller
[21],
start
power pack
[26] and
start cycle
[23].
Check that the running direction of the
skiving roller
[8] is as shown by the
motor rotation arrow
[33] on
the
cover
[34]. If not, invert any two phases off the power supply wire.
The skiving table advances and returns properly. If not satisfiying, adjust speed of the skiving table [2] by
means of the
regulating knobs
[13].
D.3.1
Calibration of the zero line
This must be done:
Ö
after replacement of the
skiving roller
[8]
Ö
when the skiving of the belt/tape end is uneven
Use the 6 mm hex-wrench provided.
Stop the machine: press the
stop skiving roller
push button [22] and the
reset cycle
button [24].
Stick a paper tape onto the end of the
wear plate
[3].
Fix
the
wear plate
[3] to the
skiving table
[2] with adhesive tape.
Press
the
start skiving roller
push button [21], the
start power pack
button [26] and the
start
cycle
button [23]. Then wait until the machine has completed a full skiving cycle.
Check that the paper strip is evenly skived over the whole width. If so, the zero setting is correct
and the machine is ready for operation.
In case the zero setting is not correct, adjust alignment of the edge of the
wear plate
[3] with the
skiving roller
[8] by turning the
alignment screws
[14] with the 6 mm hex-wrench.
Replace the strip of paper and repeat the operations described above until skiving is uniform.
D.3.2
Setting up of the skiving angle
To be carried out according to:
Ö
the thickness of the belt/tape (see individual joining data sheets)
Use the 8 mm hex-wrench provided.
Stop the machine: press the
stop skiving roller
push button [22] and the
reset cycle
button [24].
Turn
the
clamping screws
[16] anticlockwise.
Turn
the
regulating pivot
[15] to the value required (%).
Turn
the
clamping screws
[16] clockwise and tighten.
Press
the
start skiving roller
push button [21], the
start power pack
button [26] and the
start
cycle
button [23]. Then wait until the machine has completed a full skiving cycle.
If necessary, adjust the position of the
regulating pivot
[15] repeating the operations described
above until skiving is satisfying.
Skiving device AT-306