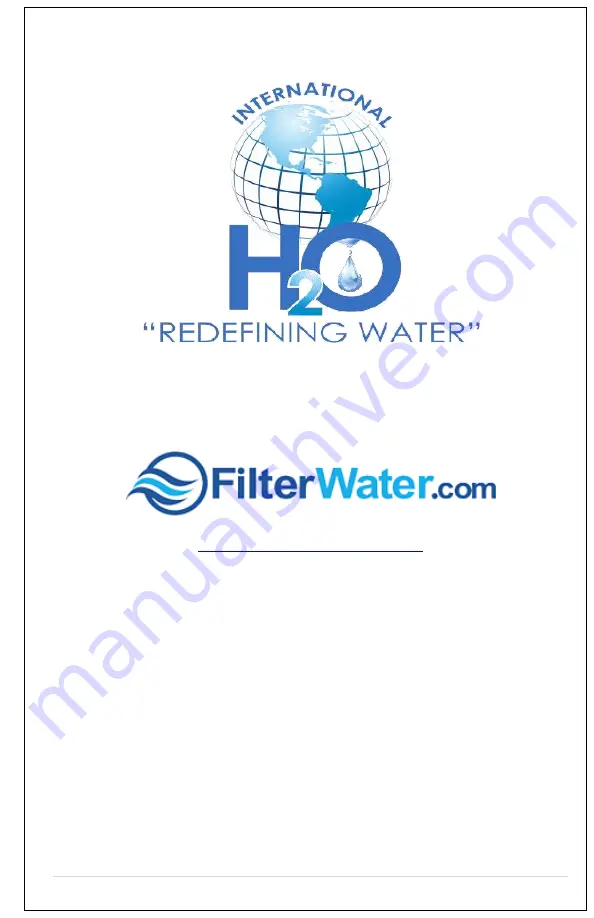
-
19 -
|
P a g e
Your Trusted Vendor:
Tel. (800) 439-0263
Fax (215) 354-0304
E-mail [email protected]
Mailing Address:
FilterWater.com
P.O. Box 968
Southampton, PA 18966
USA
-
19 -
|
P a g e
Your Trusted Vendor:
Tel. (800) 439-0263
Fax (215) 354-0304
E-mail [email protected]
Mailing Address:
FilterWater.com
P.O. Box 968
Southampton, PA 18966
USA