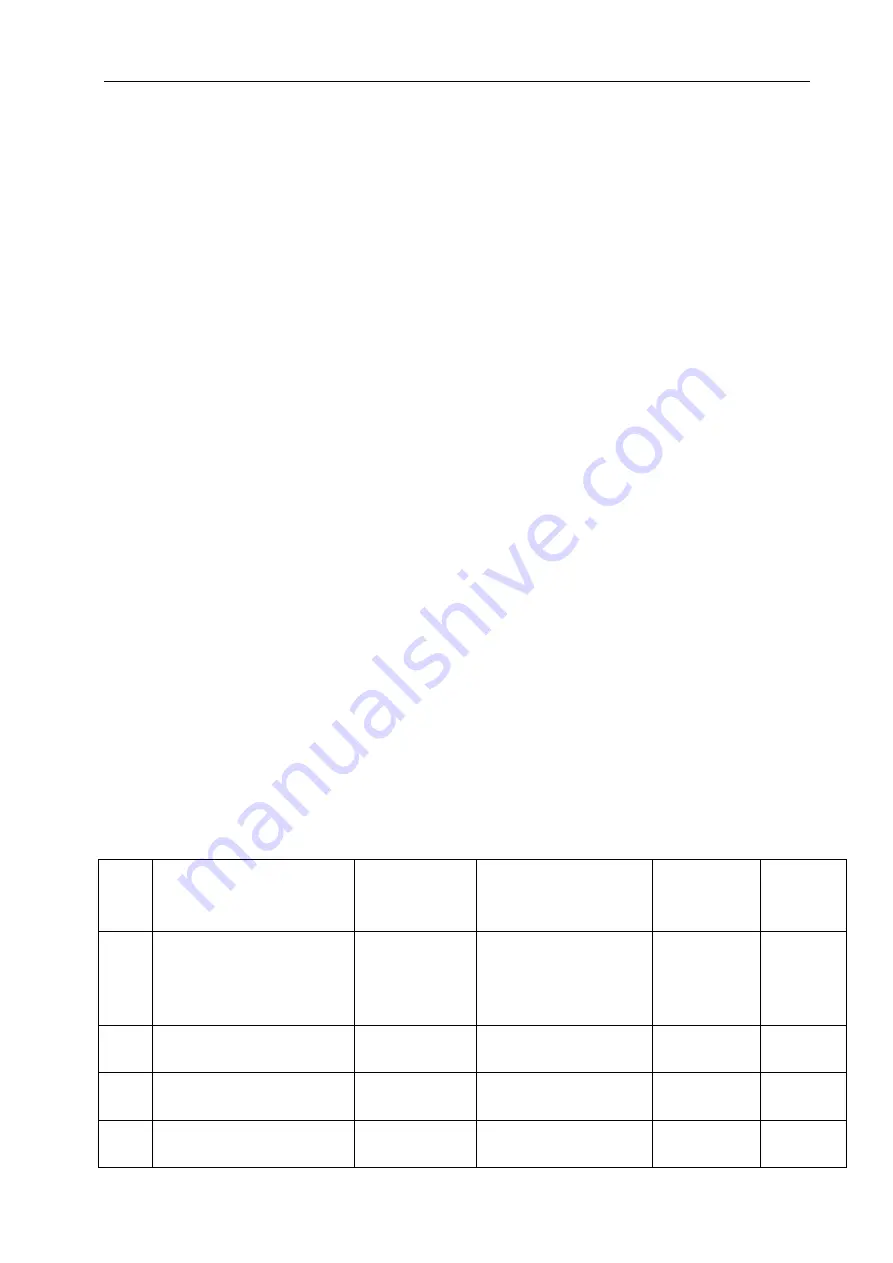
WINTER TIMBERMAX 4 – 23 ECO
37
④
Check if each controlled breaker in the electric box positioned normal “ON”. The cover
must be closed while closing the electric box for inspection. Check whether the limit
switches and emergency stops are in the normal position. Switch on pneumatic supply
(pressure under normal situation), trun the main electric breaker on the electric box to “ON”,
then the power indicator lights. Press restoration button SB0, when spindles and feeding
contactors are under normal positon, main contactor KM0 will take action and the indicator
HL10 lights, machine toll is ready to work. Press SB10-SB18 to start each spindle then to
press SB6 to start feeding. To stop the feeding, press SB7, then to stop each spindle by
pressing SB9-SB17. When the machine is running, the feeding will be stopped
automatically by pressing stop of any spindle.
Attention:
①
When the cover is opened, only jogging lift or fall the feed bead can be done,
spindles and feeding can only be operated when the cover is closed.
②
For the first start of each spindle and feeding motor, check whether the rotary
direction of each motor is tally with the symbols sticked on the control panel. If not,
change random 2 of the 3 pieces of power supply cable.
This operation can only be
carried out by qualified electrician.
③
Press emergency stop SB1 on the main control panel, wait 45 seconds till the safety
indicator HL10 lights, then to open the cover and operate.
④
Machine and electric box must use specified earthing cable. To open the electric box
and maintain can only be carried out by qualified electrician, the main power breaker
much be off at the same time before operation.
9.2
Pneumatic power
Pressure is 0.5~0.8Mpa. Adjust the cylinder pressure to a specific value by adjusting the reductor.
9.3
Dust-collection
The wind speed should be 30-34m/s to collect all the dust. For less dusts, the wind speed can be reduced.
9.4
Test run
Start the machine after the steps of 9.1-9.3 are finished, feed a 30×150×800mm or similar wood-blank in,
measure its dimension after processing and further check digits indicated on all the digital indictators
10.
Lubrication and maintenance
10.1
Lubrication of machine tool
TABLE 7
No.
Lubricated Part(s)
Lubricant
Lubricating times
Standard of
Lubricating
volume
Remark
1
Friction part when adjusting
cutter (e.g. chain, screw rod,
angular gear etc., sliding
sleeve of chief shaft
Ca-based
Grease ZG-3
Once a shift
Grease coated
2
Bearing of feeding shaft
Ca-based
Grease ZG-3
Once every 6 months
As defined
3
Gear box of feed beam
elevation
Engine oil N46
Once every 6 months
As defined
4
Working bench
Engine oil N46
3-5 times/shift
Press 4-5
times
Manual oil
pump