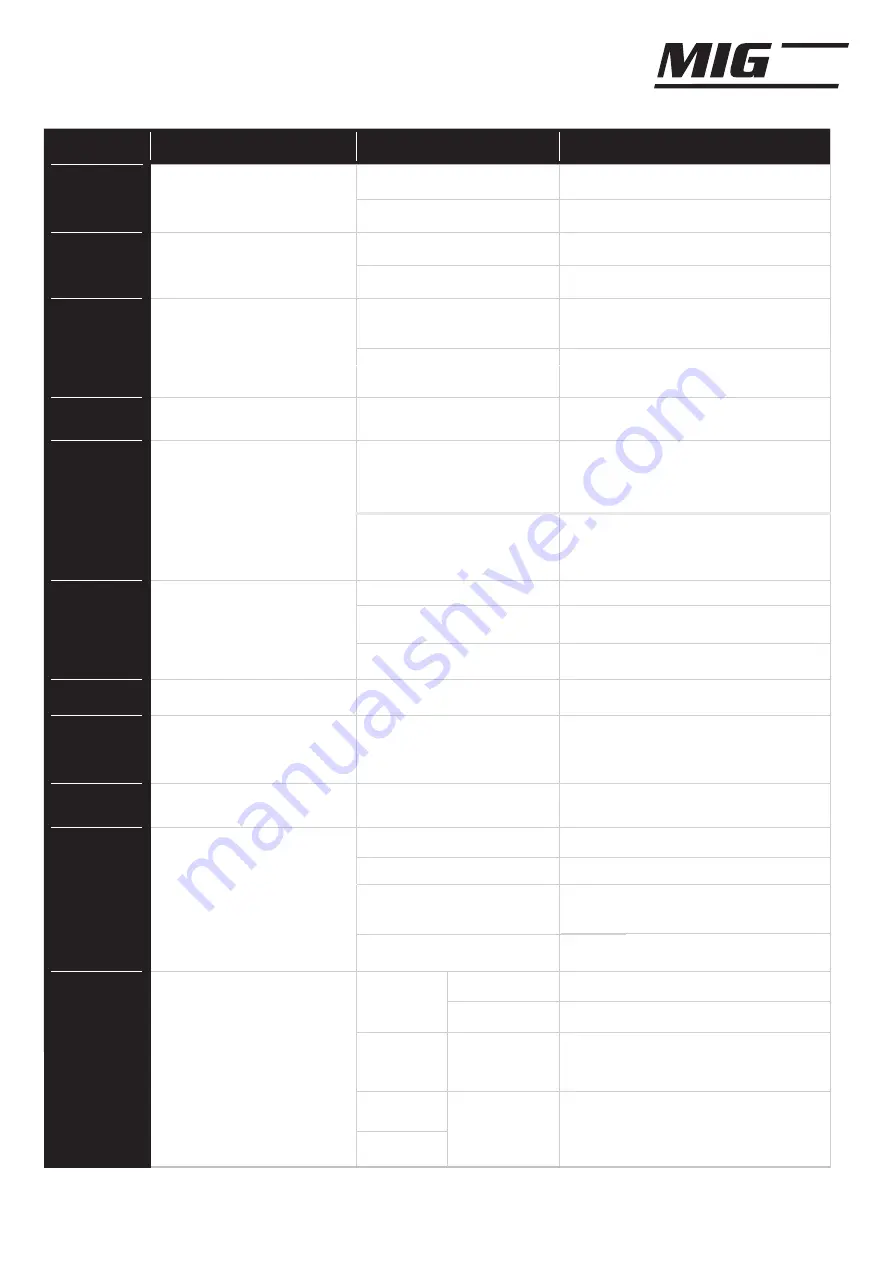
14
5.0 Troubleshooting
If there are simple troubles with your MIG160 welding machine, you can consult the following overhauling chart:
When the machine is powered
on, the fan works but the
power light is not on
Light damaged or has a bad
connection
Power PCB Failures
Test/repair the inside circuit of power
light
Repair or change control panel
When the machine is powered
on, the power light is on
but the fan doesn’t work
There is something in the fan
The fan motor is damaged
Clear out
Change fan motor
When the machine is powered
on, neither the fan or power
light work
No input voltage
Check whether there is power supply
The fuse inside the machine
is damaged
Change it (10A)
No no-load voltage output
(MMA)
The machine is damaged
Check the main circuit
The max and min value
displayed doesn’t match
the set value
No Gas Flow (TIG)
Something in the valve
Gas cylinder is closed or gas
pressure is low
Electromagnetic valve is
damaged
Remove it
Open or change the gas cylinder
Change it
The displayed current on the
screen doesnt match output
The LED screen is broken
Change the LED screen
The welding current can
not be adjusted
The welding current
potentionmeter in the front
panel has a bad connection
or is damaged
Repair or change the potentionmeter
The penetration of the molten
pool is not enough
The welding current is
adjusted too low
Increase the welding current
Gas always flows
Something in the valve
The gas test on front panel is on
Electromagnetic valve
is damaged
Remove it
Turn off
Repair or change it
Repair or change it
The alarm light is on
Over heat
protection
Over current
protection
Over welding
current
Working time
too long
Unusual current
in the main
circuit
Reduce the welding current output
Reduce the duty cycle (interval work)
Use a stable power supply/ ensure
not too many machines are using the
same power supply
1
2
3
4
5
6
7
8
9
10
11
S/N
Troubles
Reasons
Solutions
The max value isn’t in
accordance
The min value isn’t in
accordance
Adjust potentiometer Imin on the power
board
Adjust potentiometer Imaxin the current
meter
The adjustment kob of pre-gas
timeon the front panel is
damaged
Low-Voltage
Protection
Over-Voltage
Protection
Power supply
fluctuates
Use a stable power supply
160