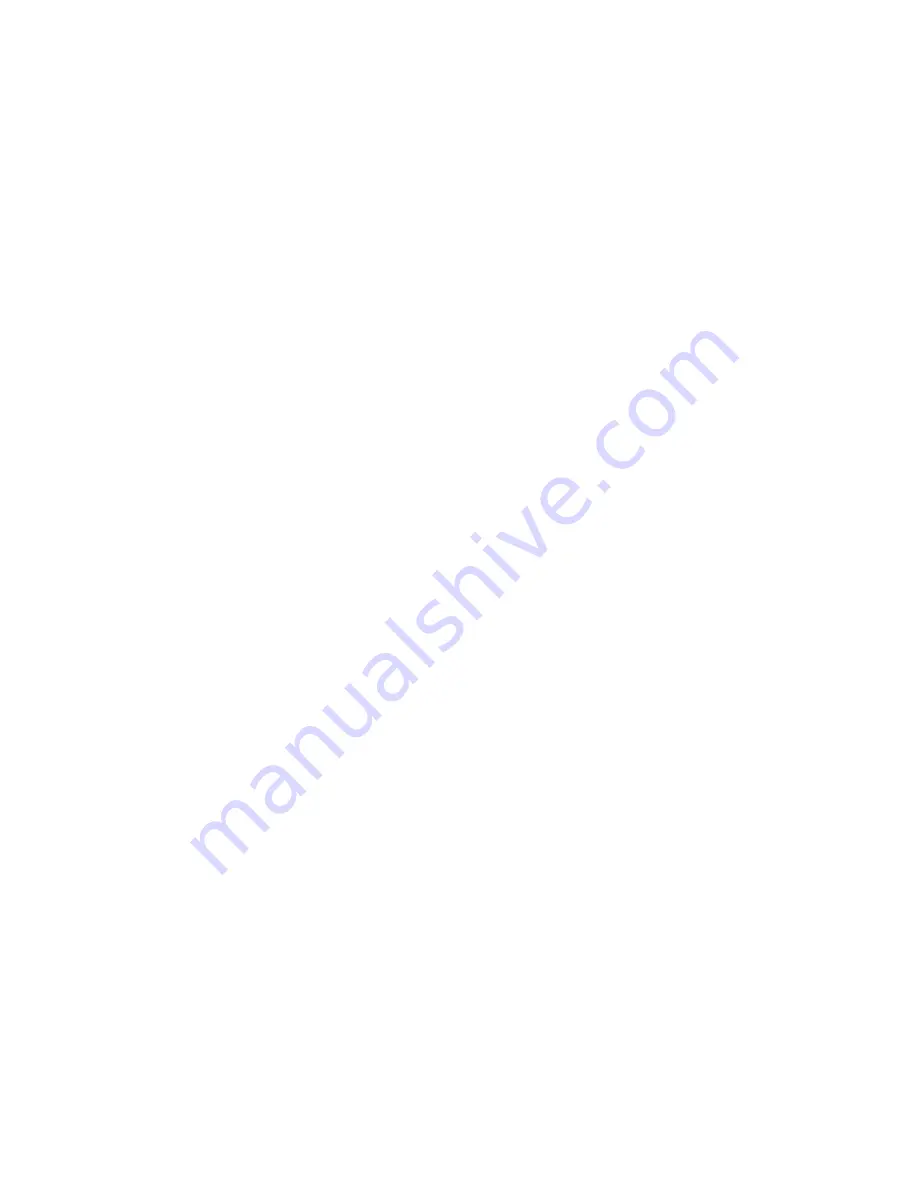
4. When the outline of the loop and the lead-in has been marked the pavement can be cut. The
saw cut should be approximately 2.0 inches deep and 0.25 inches wide. All 90 degree corners
should be chamfered so that the course of the loop wire does not change direction sharply but
rather at shallow angles of 45 degrees or less. The saw slot should be cleaned out and allowed
to dry.
5. Loop wire is typically 14, 16, 18, or 20 AWG with cross-linked polyethylene insulation, rated
for direct burial. Since moisture can cause significant changes in the dielectric constant of
the insulation, which results in excessive loop (frequency) drift, choose an insulation which
is most impervious to moisture. PVC, TFFN, THHN and THHN-THWN should be avoided
since they tend to absorb moisture and crack easily. XLPE (cross-linked polyethylene) is very
resistant to moisture absorption and provides good abrasion resistance.
6. If long lead-ins are required, it is suggested that the loop cable be spliced onto shielded, pre-
twisted, lead-in wire (IMSA specification 50-2 is recommended) at a convenient pull box
location close to the loop. The shield may be connected to earth ground at the cabinet end but
should then be insulated and isolated from earth ground at the loop end.
7. Start laying the loop wire from the termination of the lead-in out towards the loop, continue
around the loop for the number of turns required and finally return to the lead-in termination.
Leave the lead-in wire out of the slot so that it may be twisted together before being laid in the
slot. Lead-ins should be twisted with a minimum of 4 to 6 twist per foot to prevent any separa-
tion of the lead-in wires.
8. Make sure that the loop wire is pushed fully to the bottom of the saw slot. The wire must be
held firmly in the bottom of the slot using a plastic foam material called “backer rod”, before
applying loop sealent.
9. Many different types of loop sealant are now available. Single part types are the easiest to ap-
ply since no mixing is required, but they also tend to be more expensive in terms of linear feet
of saw slot filled. When applying the sealant, make sure that it is able to sink to the bottom
of the slot and completely encase the loop wire. The wire should not be able to move when
the sealant is set. Ensure that there is enough sealant to completely fill the slot; if possible
the sealant should protrude slightly above the surface of the pavement so that small rocks or
other debris cannot collect in the slot. The sealant manufacturer’s instructions concerning cure
time should be noted - especially when determining the length of time to wait before allowing
vehicles to cross the loop area.
10. It is very important that any splices be soldered and each splice point be protected with a
moisture proof seal. Failure to do so will result in system problems, if not imediately then
sometime in the near future.