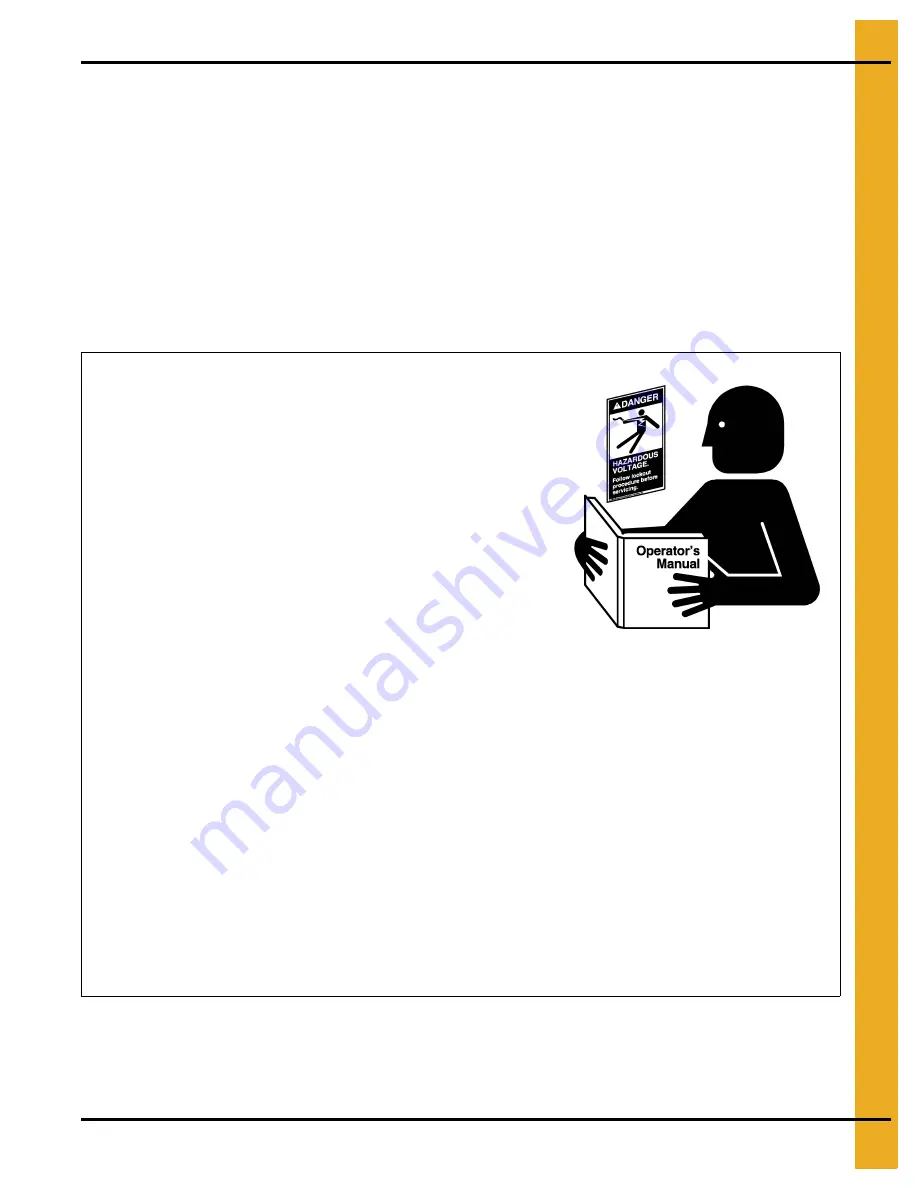
2. Safety
PNEG-1366
12" and 16" Series II Sweep Quick Disconnect Control Box Kit
7
Safety Instructions
Our foremost concern is your safety and the safety of others associated with this equipment. We want to
keep you as a customer. This manual is to help you understand safe operating procedures and some
problems which may be encountered by the operator and other personnel.
As owner and/or operator, it is your responsibility to know what requirements, hazards and precautions
exist, and to inform all personnel associated with the equipment or in the area. Safety precautions may be
required from the personnel. Avoid any alterations to the equipment. Such alterations may produce a very
dangerous situation where SERIOUS INJURY or DEATH may occur.
This equipment shall be installed in accordance with the current installation codes and applicable
regulations which should be carefully followed in all cases. Authorities having jurisdiction should be
consulted before installations are made.
Follow Safety Instructions
Carefully read all safety messages in this manual and
safety signs on your equipment. Keep signs in good
condition. Replace missing or damaged safety signs.
Be sure new equipment components and repair parts
include the current safety signs. Replacement safety signs
are available from the manufacturer.
Learn how to operate the machine and how to use controls
properly. Do not let anyone operate without instruction.
Keep unqualified personnel out of the work area at
ALL times.
Keep your machinery in proper working condition.
Unauthorized modifications to the machine may impair
the function and/or safety and affect machine life.
Never work alone.
Never start equipment until all personnel are clear of the
work area.
Never attempt to assist machinery or try to remove trash
from equipment while in operation.
Keep all guards in place during operation.
Always lock out power to equipment when work is finished.
If you do not understand any part of this manual and need
assistance, contact your dealer.
Read ALL Safety Information
and Instructions before
Operating Machinery.