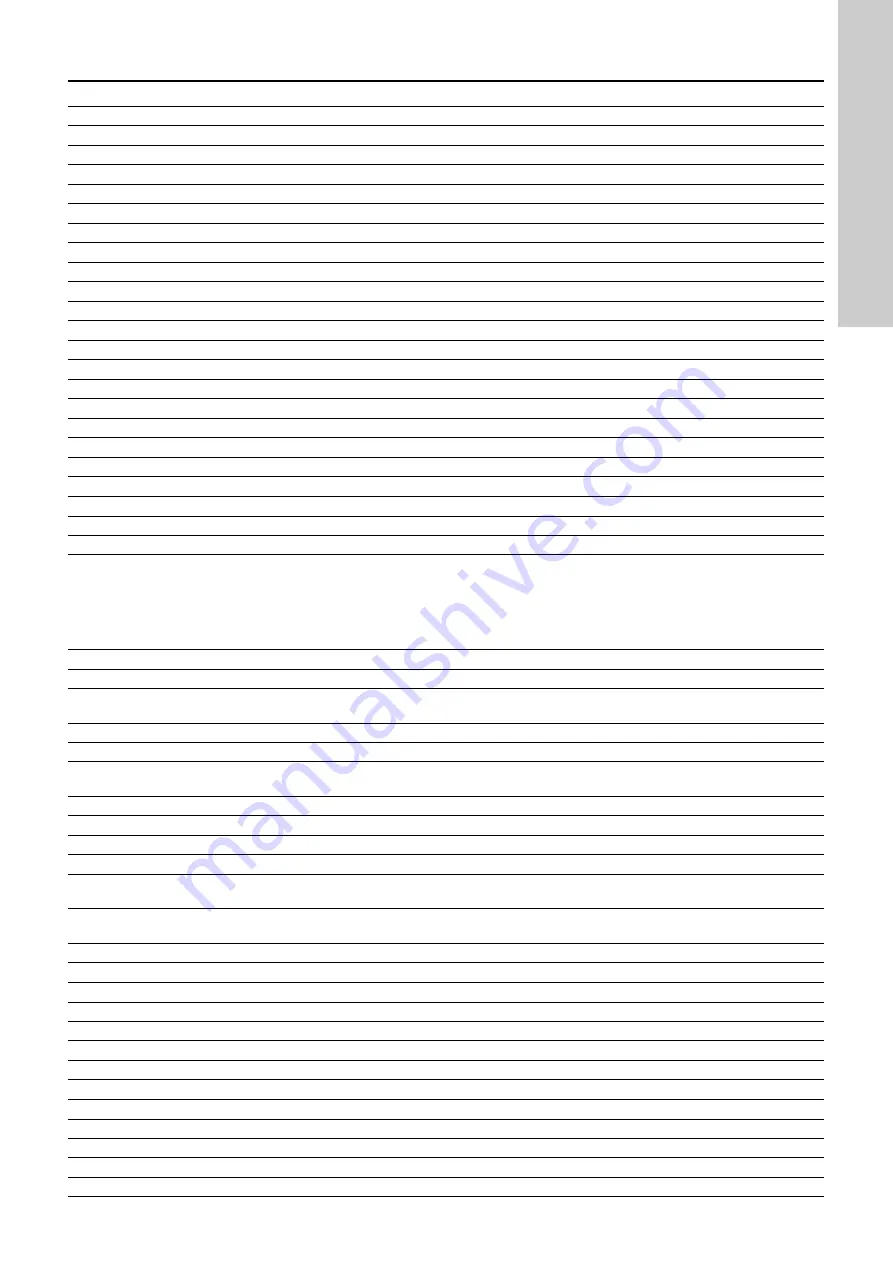
English (GB)
23
13.5 Material specification
Pos.
Description
Material
EN standard
AISI/ASTM
6a
Pin
Stainless steel
-
-
7a
Rivet
Stainless steel
-
-
9a
Key
Stainless steel
-
-
26a
O-ring
NBR
-
-
37
O-ring
NBR
-
-
37a
O-rings
NBR
-
-
44
Grinder ring
Stainless steel
1.4542
630
45
Grinder head
Stainless steel
1.4542
630
48
Stator
-
-
-
48a
Terminal board
-
-
-
49
Impeller
Cast iron
EN-JL-1030
-
50
Pump housing
Cast iron
EN-JL-1030
-
55
Stator housing
Cast iron
EN-JL-1030
-
58
Shaft seal carrier
Cast iron
EN-JL-1030
-
66
Locking ring
Stainless steel
-
-
68
Adjusting nut
Stainless steel
1.4057
431
76
Nameplate
Stainless steel
1.4301
304
90a
Electronic unit
-
-
-
90b
O-ring
-
-
-
92
Clamp
Stainless steel
1.4301
304
102
O-ring
NBR
-
-
103
Bush
Stainless steel
1.4057
431
104
Seal ring
NBR
-
-
105/
105a
Shaft seal
Primary seal (0.9 to 1.5 kW): SiC/SiC
Secondary seal (0.9 to 1.5 kW): Lip seal, NBR
Primary seal (2.6 to 4.0 kW): SiC/SiC
Secondary seal (2.6 to 4.0 kW): Carbon/aluminium oxide
Other components: NBR, stainless steel
-
-
107
O-rings
NBR
-
-
112a Retaining ring
Stainless steel
-
-
153
Bearing, lower
Up to and including 1.5 kW: 6303
2.6 kW and up: 3205
-
-
153a Locking washer
Stainless steel
-
-
153b Retaining ring
Stainless steel
-
-
154
Bearing, upper
Up to and including 1.5 kW: 6201
2.6 kW and up: 6205
-
-
155
Oil chamber
-
-
-
158
Corrugated spring
Steel
-
-
159
O-ring
NBR
-
-
161b Pt1000 sensor with bracket
-
-
-
161c
Run capacitor and Pt1000
sensor with bracket*
-
-
-
172
Rotor/shaft
Shaft part at rotor: steel
Shaft end at hydraulics: stainless steel
1.0533
1.4301
304
-
173
Screw
Steel
-
-
173a Washer
Steel
-
-
174
Earth screw
-
-
-
174a Washer
-
-
-
176 Inner
plug
part
PET
-
-
181 Outer plug part
CR rubber, cable H07RN-F
1.4308
CF-8
188a Screw
Stainless steel
-
-
190
Lifting bracket
Stainless steel
1.4308
CF-8
193
Oil screw
Stainless steel
-
-
193a Oil
Shell Ondina X420
-
-
194
Gasket
Nylon
-
-
198
O-ring
NBR
-
-
199
Locking ring
Summary of Contents for seg autoadapt
Page 1: ...SEG AUTOAdapt 0 9 4 0 kW DIN 50 Hz Service instructions GRUNDFOS INSTRUCTIONS ...
Page 20: ...English GB 20 13 2 Exploded view 0 9 to 1 5 kW TM06 5750 0316 ...
Page 21: ...English GB 21 13 3 Sectional drawing 2 6 to 4 0 kW TM06 6111 0716 6a ...
Page 22: ...English GB 22 13 4 Exploded view 2 6 to 4 0 kW Fig 21 SEG AUTOADAPT 2 6 4 kW TM06 5770 0316 ...