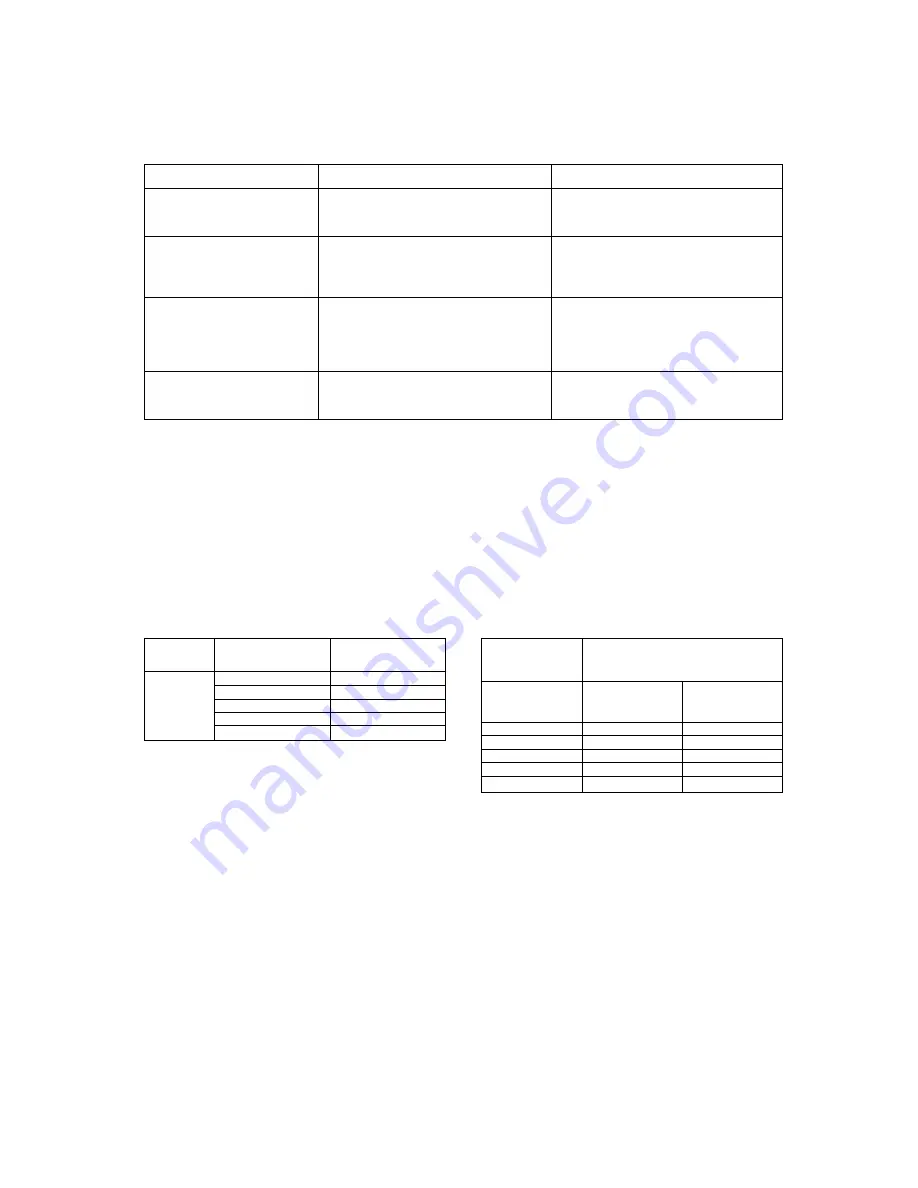
10
TROUBLESHOOTING CHART
E. Fuses Blow or Circuit Breakers Trip
POSSIBLE CAUSES
HOW TO CHECK
HOW TO CORRECT
1. High or low voltage.
Check voltage at pump panel. If not
within ± 10%, check wire size and
length of run to pump panel.
If wire size is correct, contact power
company. If not, correct and/or replace
as necessary.
2. Control box wiring and
components.
Check that control box parts match the
parts list. Check to see that wiring
matches wiring diagram. Check for
loose or broken wires or terminals.
Correct as required.
3. Defective capacitor.
Turn off power and discharge capacitor.
Check using an ohmmeter (Rx100K).
When the meter is connected, the
needle should jump forward and slowly
drift back.
If no meter movement, replace the
capacitor.
4. Starting relay (Franklin
single-phase motors only).
Check resistance of relay coil with an
ohmmeter (Rx1000K). Check contacts
for wear.
Replace defective relay.
TECHNICAL DATA
Table A
Minimum Water Flow Requirements for
Submersible Pump Motors
MOTOR
CASING OR SLEEVE
MIN. FLOW PAST
DIAMETER
I.D. IN INCHES
THE MOTOR (GPM)
4”
4
1.2
5
7
6
13
7
21
8
30
NOTES:
1. A flow inducer or sleeve must be used if the
water enters the well above the motor or if
there is insufficient water flow past the motor.
2. The minimum recommended water velocity over
4” motors is 0.25 feet per second.
Table B
Guide for Engine-Driven Generators in
Submersible Pump Applications
MINIMUM KILOWATT RATING OF
GENERATOR FOR THREE-WIRE
SUBMERSIBLE PUMP MOTORS
EXTERNALLY
INTERNALLY
REGULATED
REGULATED
MOTOR HP
GENERATOR
GENERATOR
0.33 HP
1.5 KW
1.2 KW
0.50
2.0
1.5
0.75
3.0
2.0
1.0
4.0
2.5
1.5
5.0
3.0
NOTES:
1. Table is based on typical 80°C rise continuous
duty generators with 35% maximum voltage dip
during start-up of single phase motors.
2. Contact the manufacturer of the generator to
assure the unit has adequate capacity to run
the submersible motor.
3. If the generator rating is in KVA instead of
kilowatts, multiply the above ratings by 1.25 to
obtain KVA.
Summary of Contents for Redi-Flo4
Page 14: ...13 NOTES ...
Page 15: ...14 NOTES ...