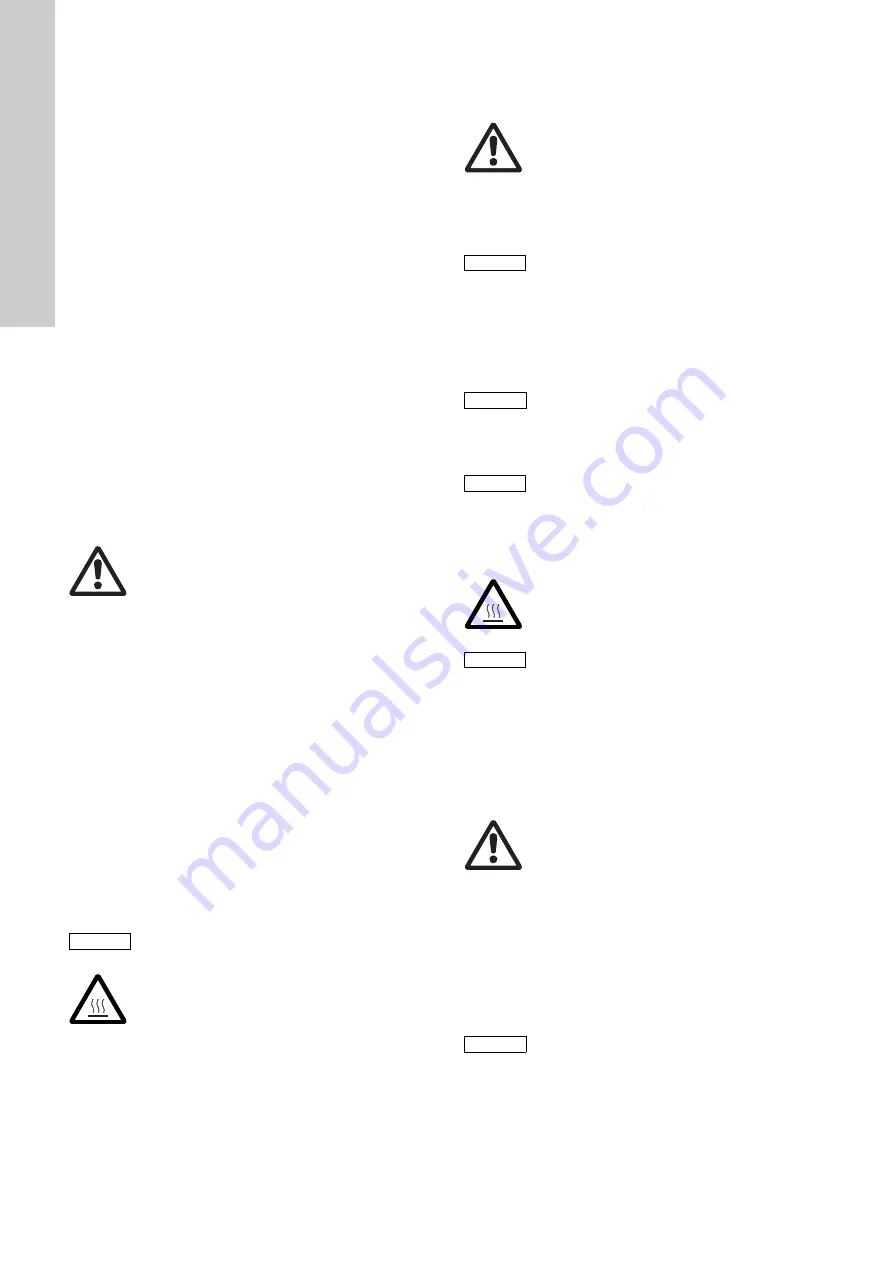
English (GB)
24
12.3 Pump set
• Check that all screws are tight and not corroded.
• Check all safety devices such as coupling guard.
• Check that all electrical connections are tight and intact.
• Replace defective cables and tighten loose connections.
• Check the alignment of the pump and driver.
See section
.
• Carry out a test run according to the standard applying to the
pump set. See section
.
12.4 Shaft seal
Mechanical shaft seals are maintenance-free and almost leak-
free. In case of considerable and increasing leakage, check the
shaft seal immediately. If the seal faces are damaged, replace the
entire shaft seal. See service instructions for the pump and
section
.
12.5 Bearings
The maintenance-free bearings in the pump are permanently
lubricated.
12.6 Fuel filters
The engine fuel filter must be replaced according to the
installation and operating instructions for the engine.
We recommend that you replace the tank fuel filter at the same
time.
12.7 Battery
The batteries must be dry under all operating conditions.
The liquid level in the batteries must be maintained.
The water used for filling must be distilled water.
Check the health of the battery by using a refractometer or similar
tool.
12.7.1 Battery replacement
If the battery is low on power, leaking or damaged otherwise the
battery must be replaced.
Before you replace the batteries, read the general precautions in
section
must be observed.
1. Observed the position of the cables.
2. Remove the black minus cables.
3. Remove the red plus cables.
4. Carefully remove the defect battery.
5. Install the new battery.
6. Mount the two red plus cables.
7. Mount the black minus cables.
For further instructions, see section
12.8 Diesel engine
1. Check the fuel level in the fuel tank and add fuel, if necessary.
2. Check the pipes of the fuel system for leakages.
3. Replace defective fuel pipes and tighten loose pipe
connections.
4. Fasten the fuel pipes with Norma type torque brackets.
5. Drain condensate from the fuel tank and the fuel filter.
6. Check oil level and add oil, if necessary.
7.
Water-cooled diesel engines
:
Check the level of coolant in the equalisation tank and add
coolant, if necessary.
8.
Water-cooled diesel engines
: Check pipes and hoses of the
cooling system for leakages. Replace defective pipes and
hoses. Tighten loose pipe and hose connections.
9. Check if the pressure gauge of the cooling circuit, if any,
displays a pressure value when the engine is running.
10. Check the entire exhaust pipe system for leaks while the
engine is running. Tighten loose pipe connections and replace
defective pipes immediately.
11. Check V-belts for wear and correct tension.
12. Check air filter.
12.9 Coupling
Couplings used for pump sets are maintenance-free.
However, check the alignment of the pump and driver once a
year. See section
12.10 Controller
Warning
Too low liquid level can cause overheat and
explosion.
Note
See also installation and operating instructions
for the diesel engine.
Warning
During and after operation, surfaces,
components and working materials of the diesel
engine can be very hot.
Warning
Fuel vapours are flammable. Therefore, never top
up fuel when the engine is running or when the
engine is warm.
Do not inhale fuel vapours when filling the fuel
tank.
Ensure good ventilation of the room during the
refuelling so that the fuel vapours dissipate
quickly.
Do not start the engine if there are fuel vapours in
the room.
Caution
Use the diesel fuel specified by the manufacturer
of the diesel engine.
Note
Collect water-containing and excess fuel in a
container and dispose of it in accordance with
local regulations.
Caution
Do not fill oil above the maximum mark.
Overfilling may damage the engine.
Use only the type of oil specified by the
manufacturer of the diesel engine.
Warning
Do not the remove cap of equalisation tank when
the engine is warm. The tank is under pressure.
Caution
Use only the type of coolant specified by the
manufacturer of the diesel engine.
Warning
A damaged exhaust system may result in
suffocation.
Note
See installation and operating instructions for
the controller.
Summary of Contents for Fire NKF Series
Page 2: ...2 ...