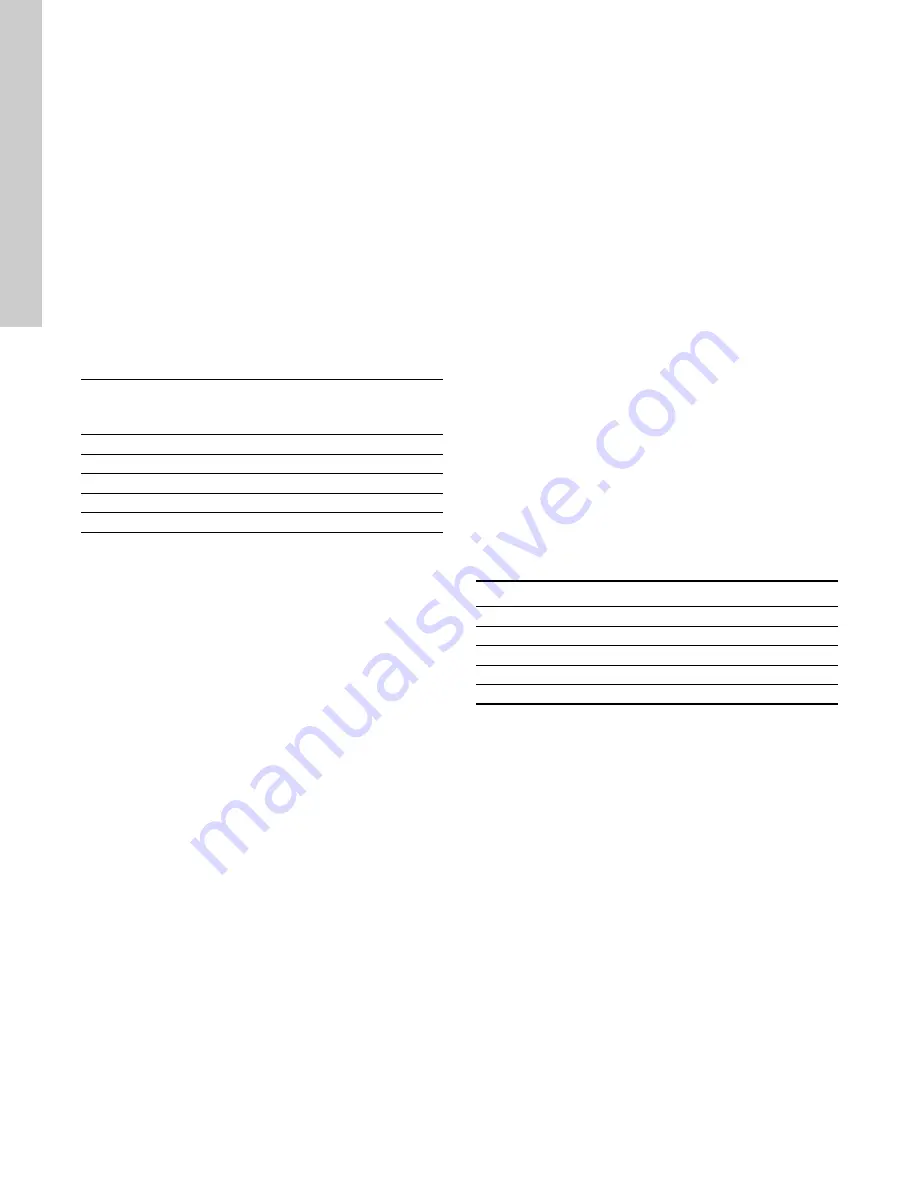
Eng
lish (US)
10
Drop-leg
Choose the pipe diameter of the drop-leg so that the mean liquid
velocity at the dimensioning flow rate is the following:
• 1.0 ft/s for installations with a single pump or multiple pumps
that do not operate simultaneously (e.g. standby pumps).
• 0.5 ft/s for installations with multiple pumps operating
simultaneously connected to the same drop-leg.
• The velocities listed above allow the entrained bubbles to rise
in the drop leg.
• Oil is to be collected from the drop leg or the vessel.
Pump-legs
Select the pipe diameter of the individual pump-legs so that the
mean liquid velocity at nominal pump flow rate is the following:
• 1.0 ft/s for HFC's
• 1.6 ft/s for R717 (NH3)
The velocities listed above allow the entrained bubbles to rise in
the pump leg.
This prevents the bubbles from entering the inlet port of the
pump.
Pipe elbow
Avoid horizontal sections in the drop-leg and the pump-leg(s) by
inclining the pipe sections by minimum 15 °F so that the vapor
always can flow backwards towards the separator. In case of pipe
elbows, the minimum bending radius is 2 times the pipe diameter.
Isolation valves
Place isolation valve(s) in the individual pump-leg(s) that have
the same or a larger diameter as the pump-leg. Use valves with a
very low flow restriction in fully open position. Place stop valves
as close to the pump inlet as possible.
Pump inlet
The reduction of the pipe diameter from pump-leg to the pump
inlet must be as smooth as possible and placed as close to the
pump inlet as possible. The horizontal run must not exceed 1.5 ft.
The reducer installed in the inlet line must be eccentric and must
be installed with the flat side on top.
Do not install strainers or filters in the drop-leg or in the pump-
leg(s) as they will reduce the available NPSHA and can increase
the level of turbulence in the pump inlet. Consider installing
strainers or filters on the outlet side of the pump. The inlet pipe is
to be insulated along with the reservoir.
Drain valving assists in pump service. The drain valves assist in
evacuating system oil and refrigerant.
A inlet pressure gauge is valuable when analyzing proper pump
performance.
5.4.2 Outlet pipe
Install a check valve downstream of the pump to prevent back
flow and reverse rotation of the pump. Install an isolation valve
(for service of pump) downstream of the check valve. Place a
pressure relief regulator in between the check valve and the
isolation valve.
Pumps installed in parallel must have a check valve in the outlet
pipeline. The minimum pressure differential at which the check
valve is completely open must be less than 2.2 psi. Place the
check valve at least 3 ft. from the pump outlet. Place the outlet
isolation valve after the check valve. Place a pressure relief
regulator in between the check valve and the isolation valve.
An outlet pressure gauge is valuable when analyzing proper
pump performance.
5.4.3 Bypass and vent line
All pumps must have a bypass and vent line from the pump head
back to the reservoir.
The bypass and vent line must include an isolation valve that can
close the bypass and vent line in case of service. This isolation
valve is to be tagged in the open position. Only close this isolation
valve during pump service.
Installations with multiple pumps must have individual bypass and
vent lines.
The bypass and vent line must be connected to the vapor zone in
the inlet tank.
Do not install a check valve on the bypass and vent line. The
bypass and vent line must be continuously rising to the inlet tank.
The orifice plate must be installed in the vertical line.
The bypass and vent line is required for each pump. Never
combine these lines.
The bypass and vent pipe size is listed below for CRN-H pumps
with 2 pole motors for refrigerants.
Pump Size
Pump Leg
R717
Pump Leg
HFCs
Drop Leg
(1 pump
operating)
CRN-H 3
2.5"
3.5"
3.5"
CRN-H 5
3.5"
4.5"
4.5"
CRN-H 10
4.5"
6.0"
6.0"
CRN-H 15
6.0"
7.0"
7.0"
CRN-H 20
7.05"
8.0"
8.0"
Grundfos pump model
Bypass and vent pipe size
CRN-H 3
3/4"
CRN-H 5
3/4"
CRN-H 10
3/4"
CRN-H 15
1"
CRN-H 20
1"
Summary of Contents for CRN-H MAGdrive
Page 26: ...26 ...