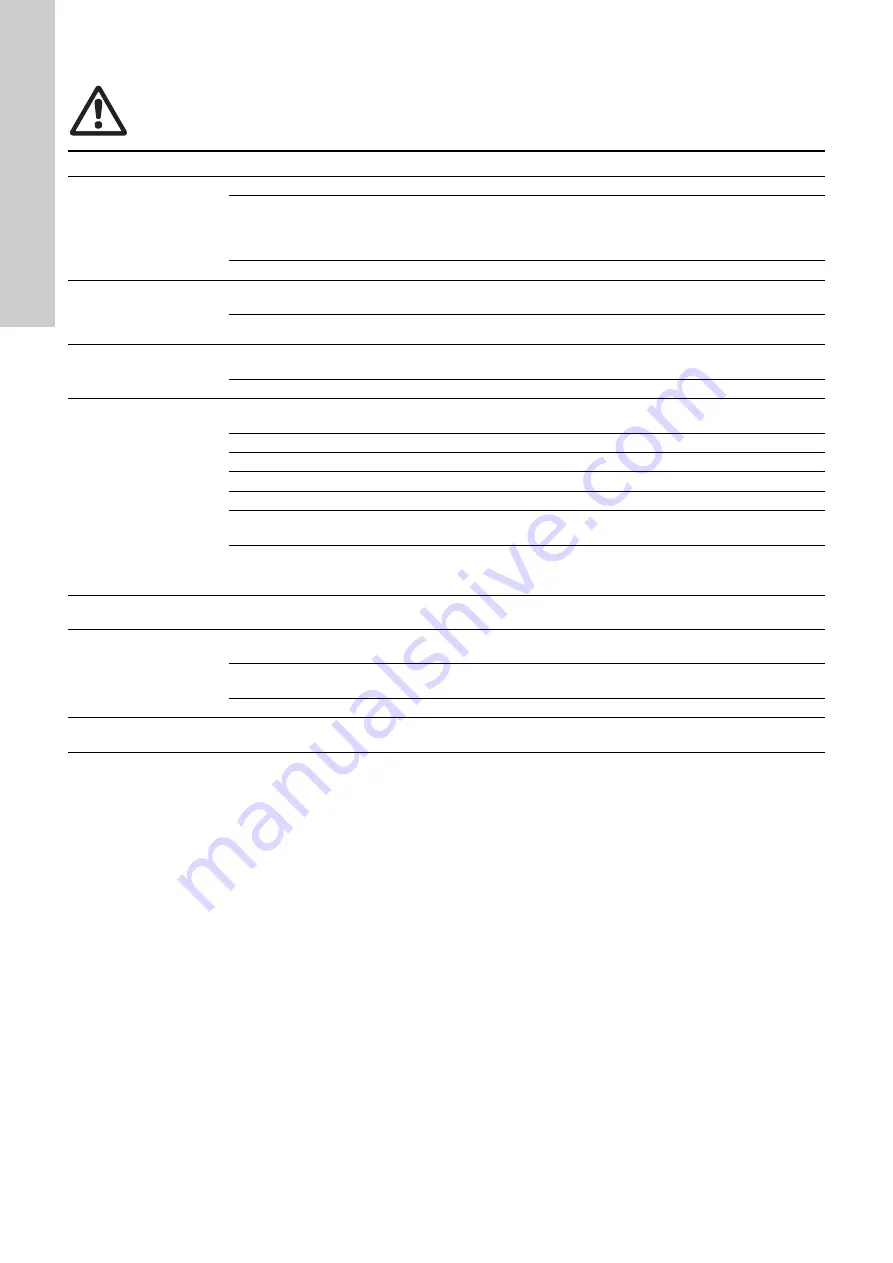
E
nglis
h (
G
B)
12
11. Fault finding chart
12. Disposal
This product or parts of it must be disposed of in an
environmentally sound way:
1. Use the public or private waste collection service.
2. If this is not possible, contact the nearest Grundfos company
or service workshop.
Warning
Before making any connections in pumps, terminal boxes or control cabinet, the power supply must be switched off.
Fault
Cause
Remedy
1.
Motor does not run
when started.
a) Power supply disconnected.
Connect the power supply.
b) Motor protection cut out.
Single-phase: Via built-in thermal switch or
fuses.
Three-phase: Via automatic circuit breaker.
Correct the fault. Await automatic resetting of the
built-in thermal switch, replace fuses (single-phase)
or cut in the automatic circuit breaker.
c) Motor defective.
Repair/replace the motor.
2.
Motor starts, but stops
immediately
afterwards.
a) Incorrect setting of pressure switch.
Increase the cut-out pressure and/or differential
pressure (
Δ
p).
b) Incorrect tank precharge pressure.
Check the tank precharge pressure.
3.
Frequent starts and
stops.
a) Incorrect setting of pressure switch.
Increase the cut-out pressure and/or differential
pressure (
Δ
p).
b) Tank defective.
Repair the tank.
4.
Pump is running but
delivers no water.
a) Suction pipe/pump or discharge pipe blocked
by impurities.
Clean the suction pipe/pump or discharge pipe.
b) Non-return valve blocked in closed position.
Clean the non-return valve.
c) Suction pipe leaky.
Repair the suction pipe.
d) Pump/suction pipe is not filled with water.
Refill the pump/suction pipe.
e) Air in suction pipe/pump.
Vent the pump. Check the suction pipe for leakages.
f)
Suction head is too high.
Check the NPSH value and modify the installation,
if necessary.
g) Three-phase versions:
Motors running with the wrong direction of
rotation.
Change the direction of rotation.
5.
Leakage from the shaft
seal.
a) Shaft seal defective.
Replace the shaft seal.
6.
Noise.
a) The pump is cavitating.
Clean the suction pipe/pump and possibly the
suction strainer.
b) The pump does not rotate freely.
Support the manifolds/pipes with strong and
appropriate support.
c) Back flow when the pump stops.
Change or clean the non-return valve.
7.
Leakage from hydraulic
chambers.
a) Mechanical stress on the pump. The manifolds/
pipes are not supported.
Support the manifolds/pipes with strong and
appropriate support.
Subject to alterations.