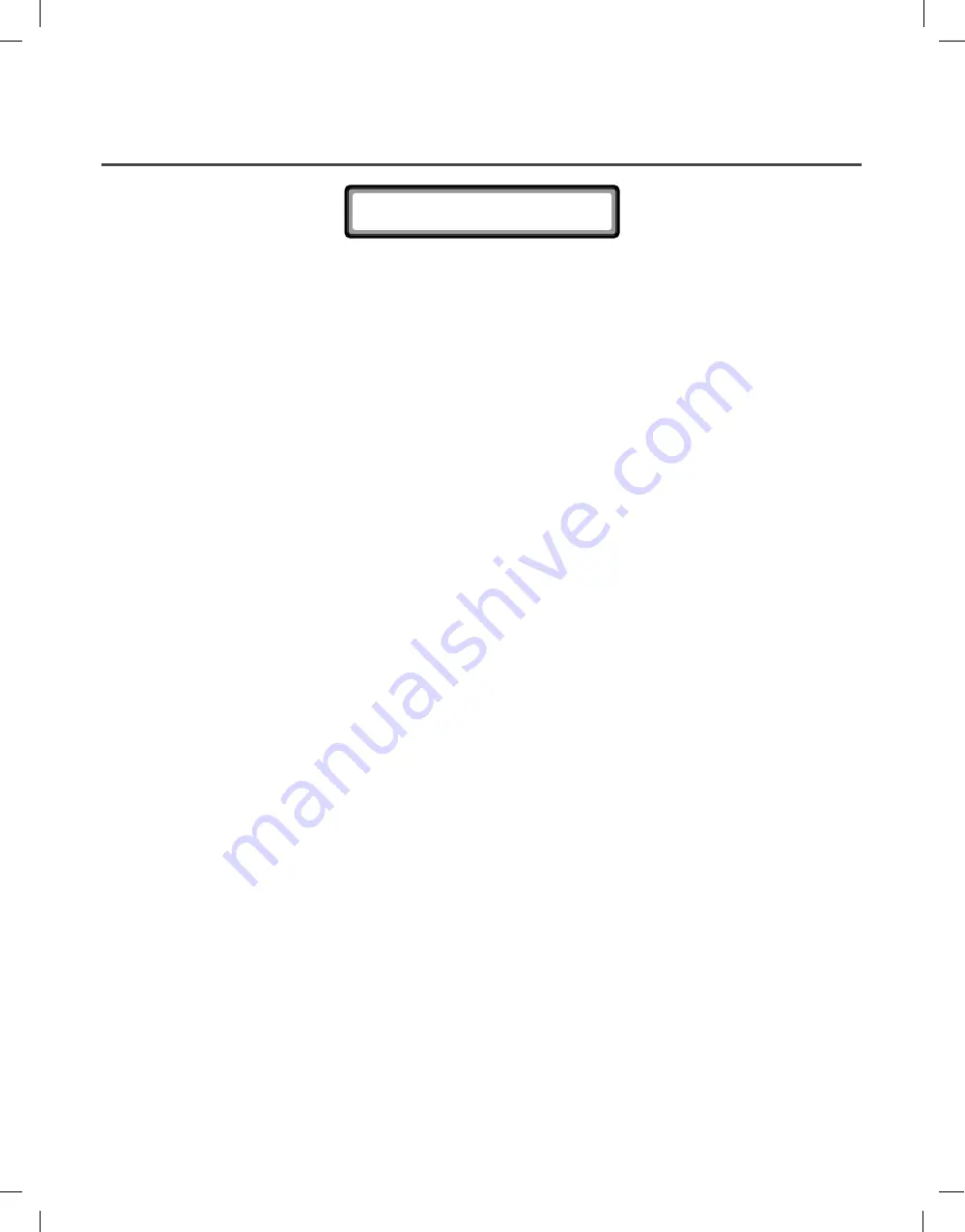
CONTENTS
3
1. IMPORTANT SAFETY INSTRUCTIONS ............................................................................. 4
2. SPECIFICATIONS ............................................................................................................. 10
3. FEATURES AND BENEFITS ............................................................................................. 12
4. INITIAL STEPS FOR INSTALLING YOUR DRYER ............................................................ 13
5. STACK MACHINE INSTALLATION INSTRUCTIONS ........................................................ 19
6. EXHAUST REQUIREMENTS AND MAINTENANCE ......................................................... 28
7. DRYER CYCLE PROCESS ............................................................................................... 32
8. COMPONENT TESTING INFORMATION ......................................................................... 33
9. MOTOR DIAGRAM AND SCHEMATIC .............................................................................. 36
10. CONTROL LAY - OUT ..................................................................................................... 37
11. WIRING DIAGRAM ........................................................................................................... 38
12. DIAGNOSTIC TEST.......................................................................................................... 39
12-1. TEST 1 240V AC ELECTRICAL SUPPLY ............................................................ 40
12-2. TEST 2 THERMISTOR TEST................................................................................ 43
12-3. TEST 3 MOTOR TEST ......................................................................................... 44
12-4. TEST 4 MOISTURE SENSOR............................................................................... 45
12-5. TEST 5 DOOR SWITCH TEST.............................................................................. 46
12-6. TEST 6 HEATER SWITCH TEST - ELECTRIC TYPE........................................... 47
12-7. TEST 7 GAS VALVE TEST - GAS TYPE .............................................................. 48
13. ERROR MODE ................................................................................................................ 49
14. CHANGE GAS SETTING (NATURAL GAS, PROPANE GAS) ........................................ 50
15. DISASSEMBLY INSTRUCTIONS .................................................................................... 52
16. EXPLODED VIEW ........................................................................................................... 60
16-1-1. Control Panel & Plate Assembly - Coin / OPL Type ............................................. 60
16-2-1. Cabinet & Door Assembly - Electric Stack Upper Type ........................................ 61
16-2-2. Cabinet & Door Assembly - Electric Stack Lower Type ........................................ 62
16-3-1. Drum & Motor Assembly: Electric Type ................................................................ 63
www.groupdynamics-laundry.com