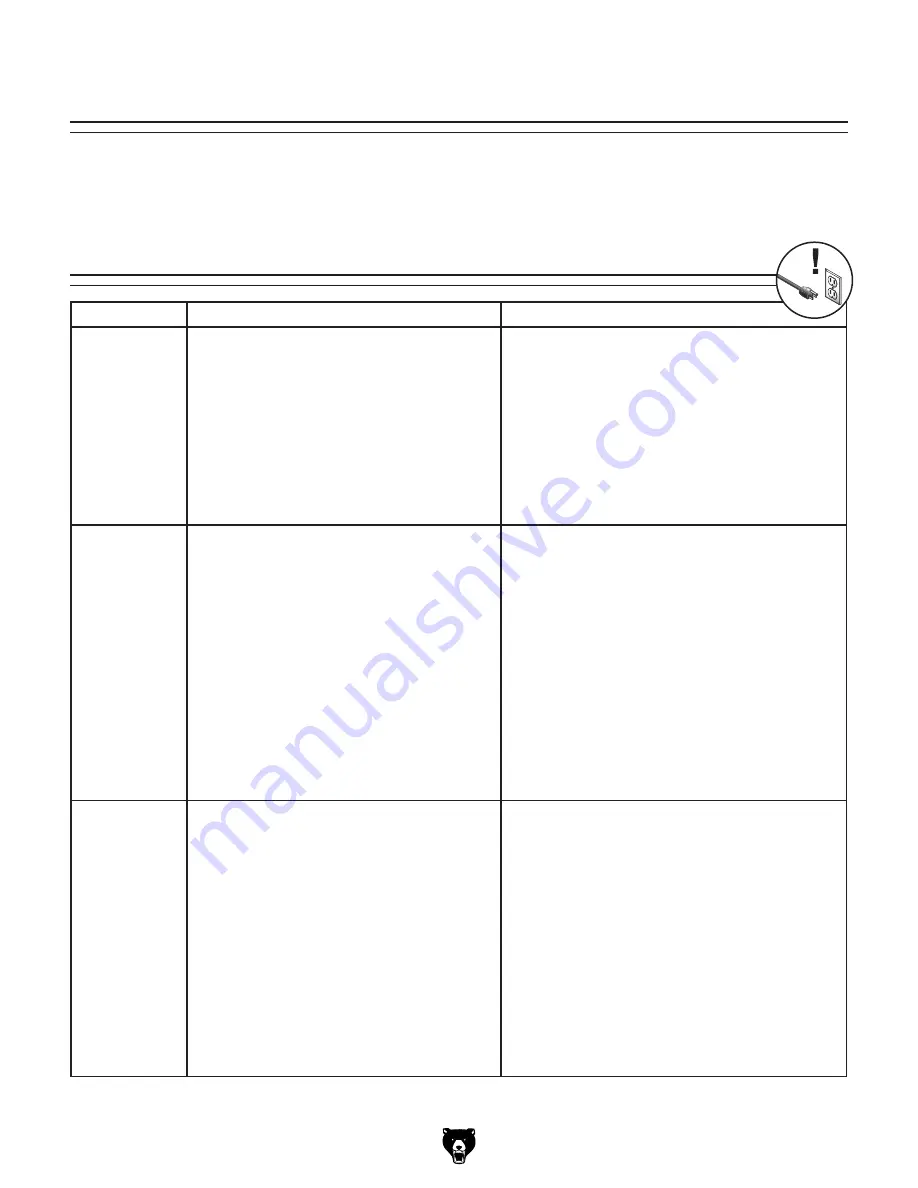
Model T28798 (Mfd. Since 12/18)
-27-
Review the troubleshooting procedures in this section if a problem develops with your machine. If you need
replacement parts or additional help with a procedure, call our Technical Support.
Note: Please gather the
serial number and manufacture date of your machine before calling.
SECTION 7: SERVICE
Troubleshooting
Symptom
Possible Cause
Possible Solution
Machine does
not start or a
breaker trips.
1. Disabling pin installed in switch.
2. Power supply circuit breaker tripped or fuse
blown.
3. Motor wires connected incorrectly.
4. Plug/receptacle at fault/wired incorrectly.
5. Wiring open/has high resistance.
6. START/STOP or circuit breaker switch at fault.
7. Start capacitor at fault.
8. Centrifugal switch/contact points at fault.
9. Motor at fault.
1. Remove disabling pin (
Page 19).
2. Ensure circuit is sized correctly and free of shorts.
Reset circuit breaker or replace fuse.
3. Correct motor wiring connections (
Page 28).
4. Test for good contacts; correct the wiring.
5. Check/fix broken, disconnected, or corroded wires.
6. Replace switch/circuit breaker.
7. Test/replace.
8. Adjust/replace centrifugal switch/contact points.
9. Test/repair/replace.
Machine has
vibration or noisy
operation.
1. Debris caught in impeller.
2. Motor or component loose.
3. Motor fan rubbing on cover.
4. Motor mount loose/broken.
5. Motor bearings at fault.
6. Motor shaft bent.
7. Dust collector not on a flat surface, wobbles.
8. Impeller damaged or unbalanced.
9. Impeller loose on motor shaft.
1. Inspect impeller for debris or damage (
Page 25).
2. Inspect/replace damaged bolts/nuts, and retighten
with thread-locking fluid.
3. Fix/replace fan cover; replace loose/damaged fan.
4. Tighten/replace.
5. Test by rotating shaft; rotational grinding/loose shaft
requires bearing replacement.
6. Test with dial indicator. Replace motor if damaged.
7. Stabilize dust collector.
8. Disconnect dust collector from power. Inspect
impeller for dents, bends, or loose fins. Replace
impeller if damaged.
9. Secure impeller; replace motor and impeller as a set
if motor shaft and impeller hub are damaged.
Dust collector
does not
adequately
collect dust
or chips; poor
performance.
1. Collection drawer or air filter dust tray are full.
2. Filters are dirty/clogged.
3. Clog in ducting.
4. Leak in ducting/connections.
5. Ducting blocked/restricted.
6. The dust collector is too far away from the
point of suction, or there are too many sharp
bends in the ducting.
7. Dust collector is undersized.
8. Run capacitor at fault.
9. Centrifugal switch/contact points at fault.
1. Empty collection drawer and dust tray (
Page 24).
2. Clean filters; replace with new filters if performance
does not improve (
Page 26).
3. Remove clog.
4. Seal leak.
5. Remove ducting from dust collector inlet and
unblock the restriction.
6. Relocate the dust collector closer to the point of
suction; remove sharp bends in ducting.
7. Install a larger dust collector.
8. Test/replace.
9. Adjust/replace centrifugal switch/contact points if
available.
Summary of Contents for T28798
Page 15: ...Model T28798 Mfd Since 12 18 13 5mm Hardware Recognition Chart...
Page 36: ......