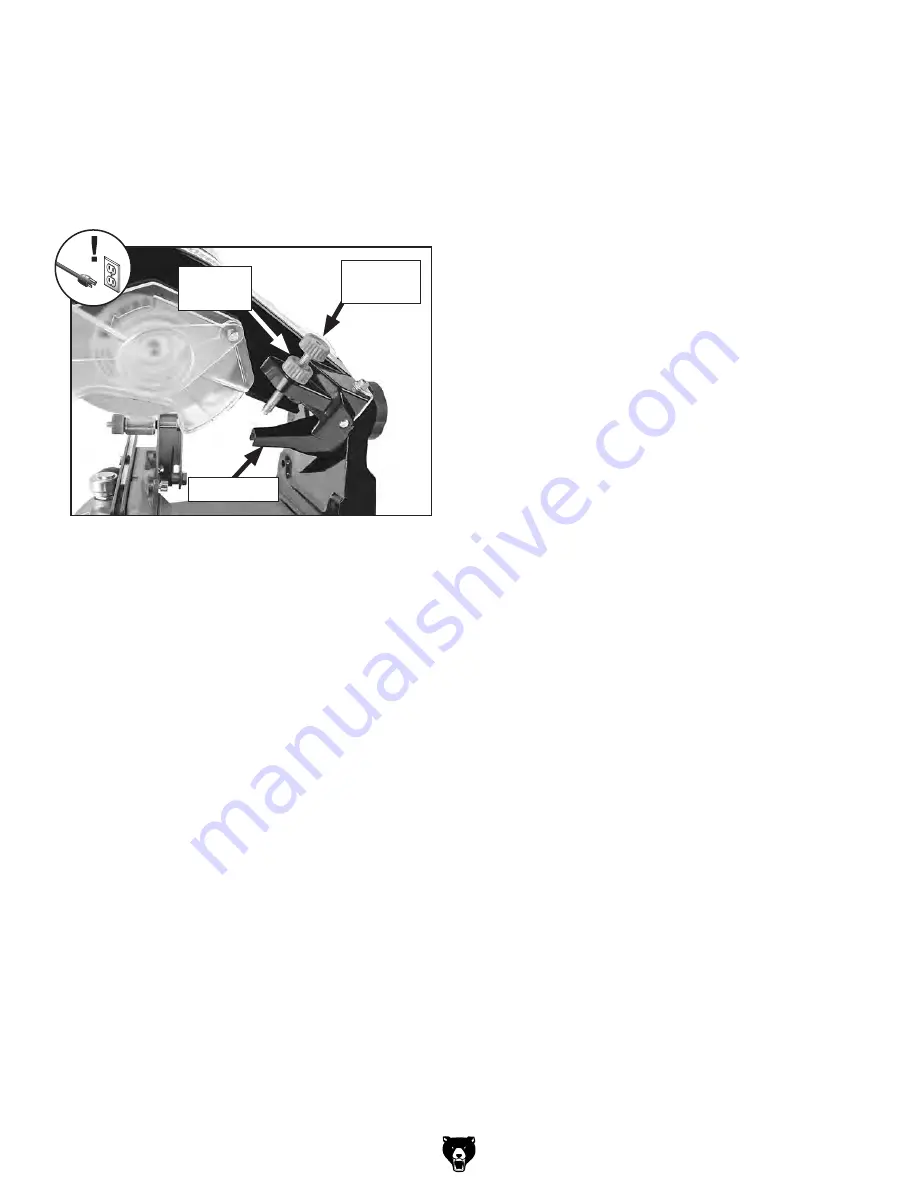
Model T23108 (Mfg. Since 7/10)
-27-
15. Rotate the clamp lever to the right to firmly
secure the chain between the clamp plates of
the chain holder.
16. Lower the grinding wheel into the cutter gullet
until it stops, then thread the depth knob bolt
down until it is against the depth stop (see
Figure 33).
Important: When adjusting the depth knob
bolt, keep in mind that you want to replace
and sharpen angles that may be worn or
damaged. Do not make the gullet any deeper
than is necessary to accomplish this.
Also, taking deep cuts with the grinding wheel
could burn the metal, which will damage
the temper of the steel. Chain cutters that
are heated excessively during sharpening
become brittle and dull quickly.
It is better to make a few light passes than
one deep one!
17. Back the depth knob bolt away from the depth
stop by a small amount, then thread the knob
lock nut down to secure the setting.
18. Adjust the advancement guide so that the
chain moves slightly to the right. This will
remove a small amount from the top and side
plates and provide the sharpened angles.
Note: This critical adjustment is a matter of
trial-and-error and experience.
19. Connect the sharpener to power and wait for
the wheel to come to full speed.
20. Using a slow and steady pace, lower the
grinding wheel into the first cutter link until the
depth bolt hits against the depth stop, then
allow the spring-loaded swing arm to raise
the grinding wheel slowly.
21. While taking care not to contact the spinning
grinding wheel with your hands or the chain,
rotate the clamp lever to the left enough to
release the chain from the clamp plates.
22. Slowly pull the chain to the right until the
advancement guide falls behind the next
cutter link for that side, then
pull the chain to
the left to firmly seat the advancement guide
against the rear of the cutter link to be sharp-
ened. This will properly position the link for
sharpening.
23. Re-tighten the clamp lever and repeat Steps
19–22 until all cutters for that side of the
chain have been sharpened.
24. Turn the sharpener OFF and wait for the
grinding wheel to completely stop, then dis-
connect the sharpener from power.
25. Release the chain from the clamp plates, turn
it around 180° so that the cutters on the other
side of the chain are ready for sharpening.
26. Rotate the chain holder to align with the angle
marks on the other side of the rotation scale,
and, if the chain requires a gullet angle, tilt
the chain holder 10° in the opposite direc-
tion.
27. When you are satisfied that the sharpener
settings are correct, repeat
Steps 18–23
for the rest of the cutters on that side of the
chain.
28. Check, and if necessary, adjust the height of
the depth gauges. Refer to the next subsec-
tion for more information.
29. Clean and lubricate the chain per the manu-
facturer's recommendation before re-install-
ing it onto the chain saw.
Figure 33. Depth stop and controls.
Depth
Knob Bolt
Knob
Lock Nut
Depth Stop
Summary of Contents for T23108
Page 40: ......