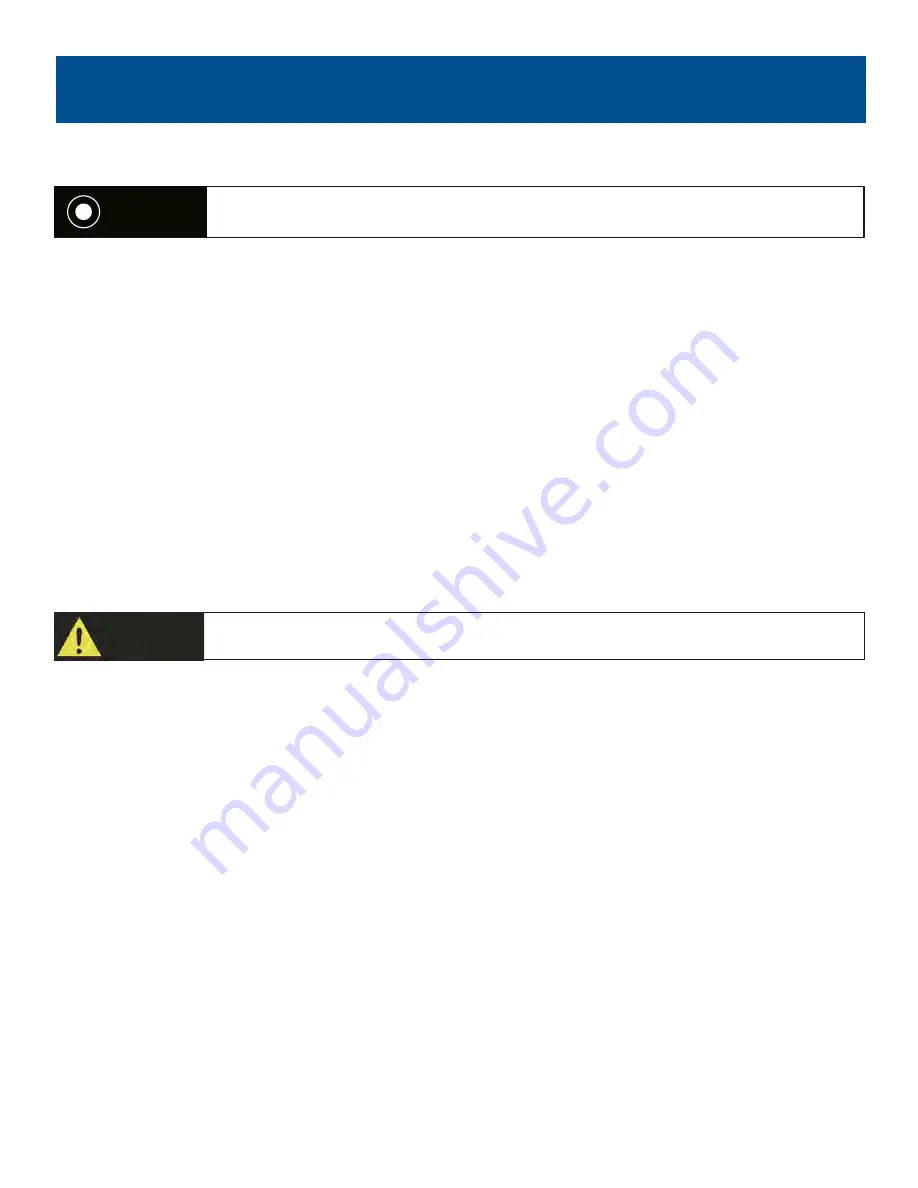
TROUBLESHOOTING
Troubleshooting
Troubleshooting problems may have similar causes and solutions.
•
Low pressure, not enough air, or compressor does not stop.
o
Tank drain valve is open: Close drain valve.
•
Prolonged excessive air.
o
Decrease amount of air used.
•
Compressor not large enough for job.
o
Check air requirement of accessory. If it is higher than CFM and pressure of compressor, you need a larger compressor. Most
accessories are rated at 25% of actual CFM while running continuously.
•
Restricted check valve.
o
Remove and clean or replace.
•
Hole in air hose.
o
Check and replace if necessary.
•
Tank leaks.
o
Replace tank.
Immediately replace tank. Do not attempt to repair.
•
Blown seals.
o
Replace any faulty seals.
o
Replace worn parts and reassemble with new seals.
•
Excessive starting and stopping while not in use.
o
Fittings leak. Check fittings with soapy water. Tighten or reseal leaking fittings. DO NOT OVERTIGHTEN.
o
Replace worn parts and reassemble with new seals.
o
Replace any regulator internal parts.
•
Regulated pressure gauge reading drops when air accessory is being used.
o
This is normal in some applications.
•
Compressor not large enough.
o
If pressure drops too low, adjust regulator while accessory is used.
o
Check air requirement of accessory, it may be higher than CFM pressure supplied by compressor. Most accessories are rated
at 25% of actual CFM while running continuously.
•
Circuit breaker trips (fuse blows) too often.
o
Low voltage, consult electrician.
17
NOTE!
WARNING!