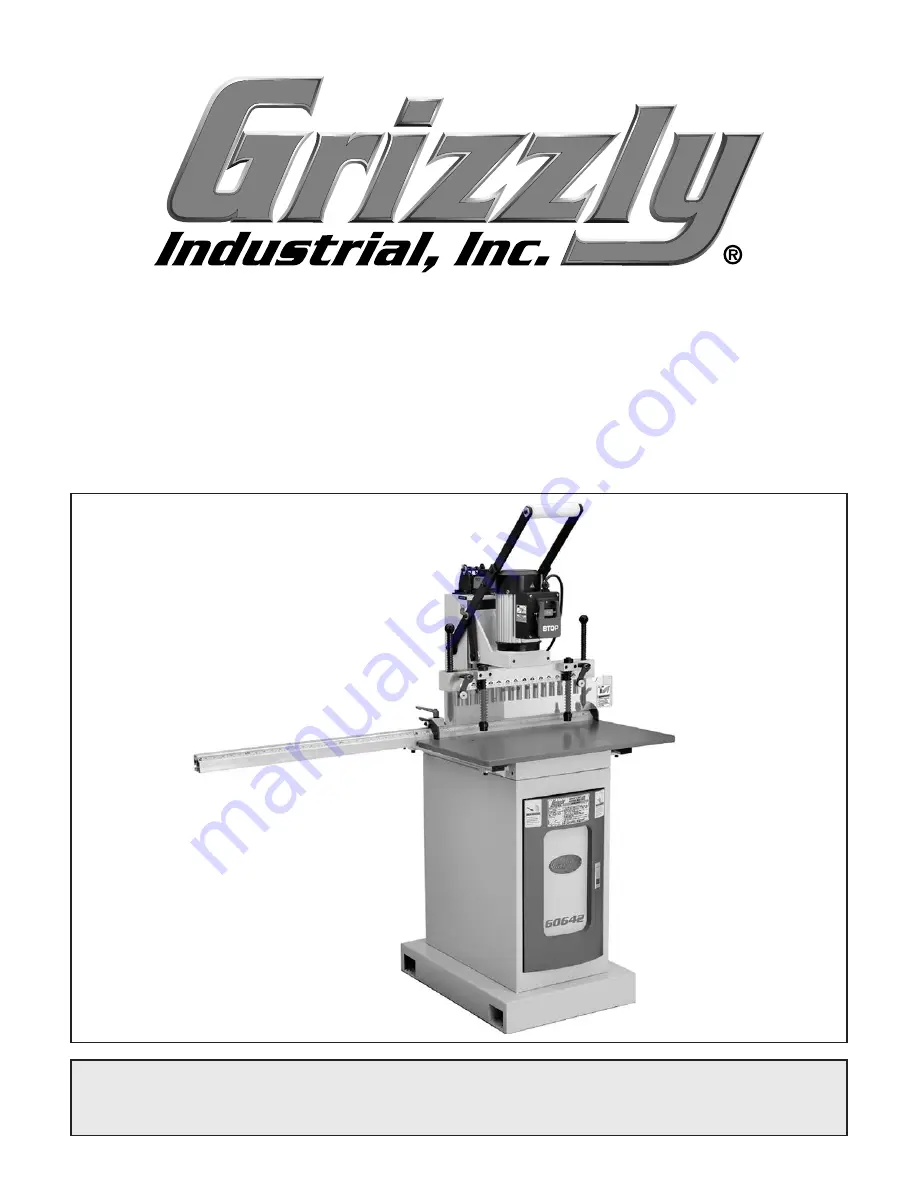
MODEL G0642
15-BIT LINE BORING MACHINE
OWNER'S MANUAL
(For models manufactured since 11/14)
COPYRIGHT © NOVEMBER, 2007 BY GRIZZLY INDUSTRIAL, INC., REVISED MARCH, 2018 (HE)
WARNING: NO PORTION OF THIS MANUAL MAY BE REPRODUCED IN ANY SHAPE
OR FORM WITHOUT THE WRITTEN APPROVAL OF GRIZZLY INDUSTRIAL, INC.
#TS9904 PRINTED IN TAIWAN
V2.03.18
Summary of Contents for Line Boring Machine G0642
Page 44: ... 42 Model G0642 Mfd Since 11 14 ...
Page 48: ......