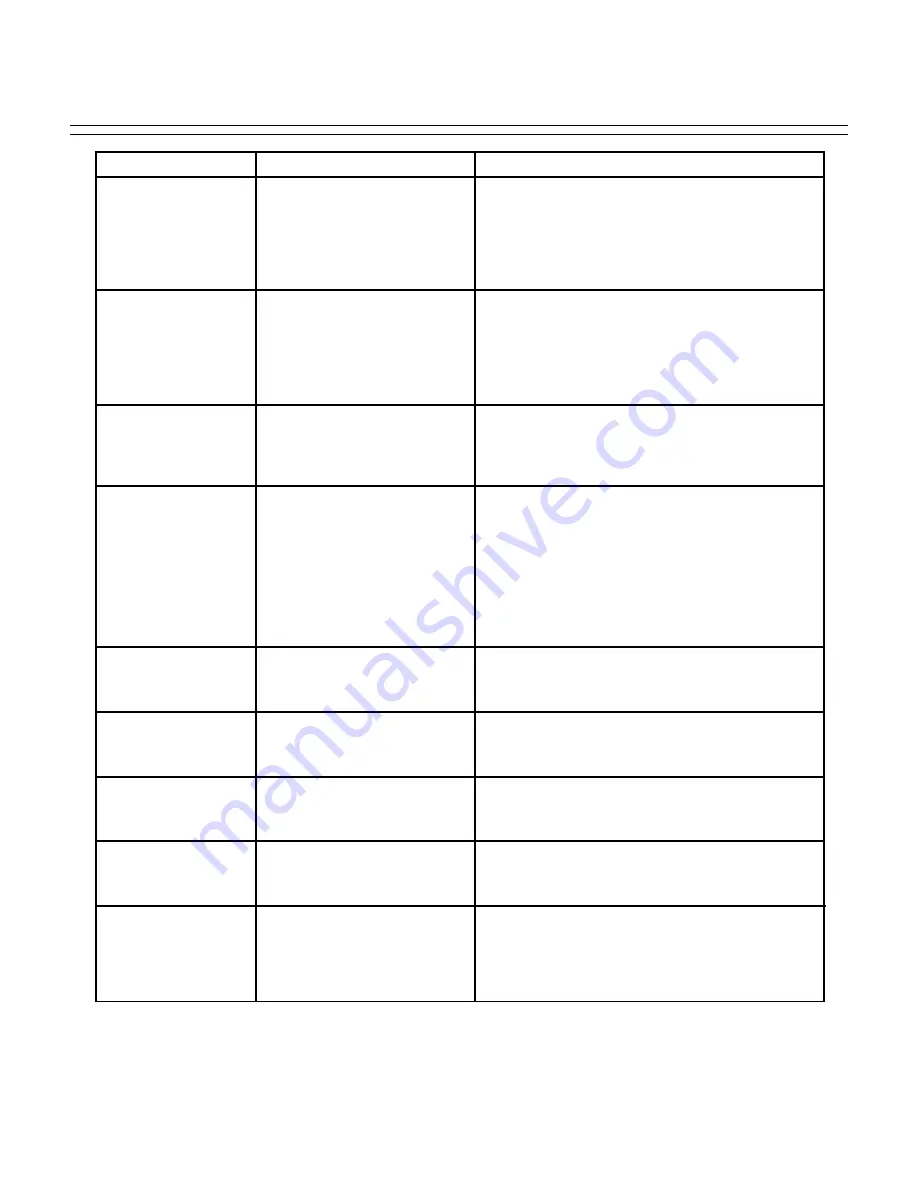
G8694/G8695/G8889 Air Compressors
-13-
SYMPTOM
Pump Motor Will Not
Start
Pump Motor Starts; But
Fuses Blow or Circuit
Breakers Trip
Low Pressure At The
Tool
Low Pressure At The
Tanks
Compressor Knocking
Air Leaks From Pressure
Switch
Air Is Dirty Or Has
Excessive Moisture
Motor Runs Hot
Pressure Relief Valve
Stays Open And Motor
Won’t Stop Running
POSSIBLE CAUSE
1. Low voltage.
2. Open circuit in motor, switch or
cord.
3. Tank already pressurized.
4. Thermal overload switch.
1. Short circuit in line cord or plug.
2. Short circuit in motor or loose
connections.
3. Incorrect fuses or circuit break-
ers in power line.
1. Air leaks in flexible hoses.
2. Pressure gauge bad
3. Pressure regulator bad.
1. Air leaks in tanks or delivery
pipes.
2. Drain cock open
3. Safety valve releasing below
125 PSI.
4. Air filter clogged.
5. Gaskets leaking
6. Worn rings.
1. Improper oil level.
2. Air filter clogged.
3. Piston assembly loose.
1. Faulty check valve.
2. Faulty pressure switch.
1. Tanks not drained.
2. Delivery pipes are dirty.
1. Cooling Fins Dirty.
2. Air filter clogged.
1. Faulty pressure switch, unit is
trying to overpressure the tank
2. Faulty pressure relief valve.
CORRECTIVE ACTION
1. Check power line for proper voltage.
2. Inspect all lead connections on motor, switch and
cord for loose or open connections.
3. Motor will not start if tank pressure is too high.
4. Thermal overload switch has tripped, wait for motor
to cool, then reset switch by pressing red button.
1. Inspect cord or plug for damaged insulation and
shorted wires.
2. Inspect all connections on motor for loose or shorted
terminals or worn insulation.
3. Install correct fuses or circuit breakers.
1. Check air hoses and all connections for leaks.
2. Check pressure in line with known good gauge.
3. Adjust pressure regulator, if no improvement inspect
regulator for leaks or replacement.
1. Check air tanks, pipes and all connections for leaks.
2. Close drain cock.
3. Replace safety valve.
4. Inspect and clean air filter.
5. Check gaskets on cylinder head assembly, repair or
replace as needed.
6. Inspect and replace pump piston rings.
1. Check oil level and add oil.
2. Inspect and clean air filter.
3. Inspect and repair piston and connecting rod.
1. Clean dirt or debris from rubber membrane of check
valve after removing top nut.
2
Repair or replace pressure switch.
1. Open drain cocks on both tanks and make certain all
condensation water is drained out.
2. Remove delivery pipes, clean out and replace.
1. Clean cylinder head fins and also remove any accu-
mulated dirt or grease from motor area.
2. Inspect and clean air filter.
1. Turn compressor off, unplug from power supply,
drain tank. DO NOT USE until switch is repaired or
replaced.
2. Relief valve is relieving pressure too early, test pres-
sure relief and repair or replace,
TROUBLESHOOTING