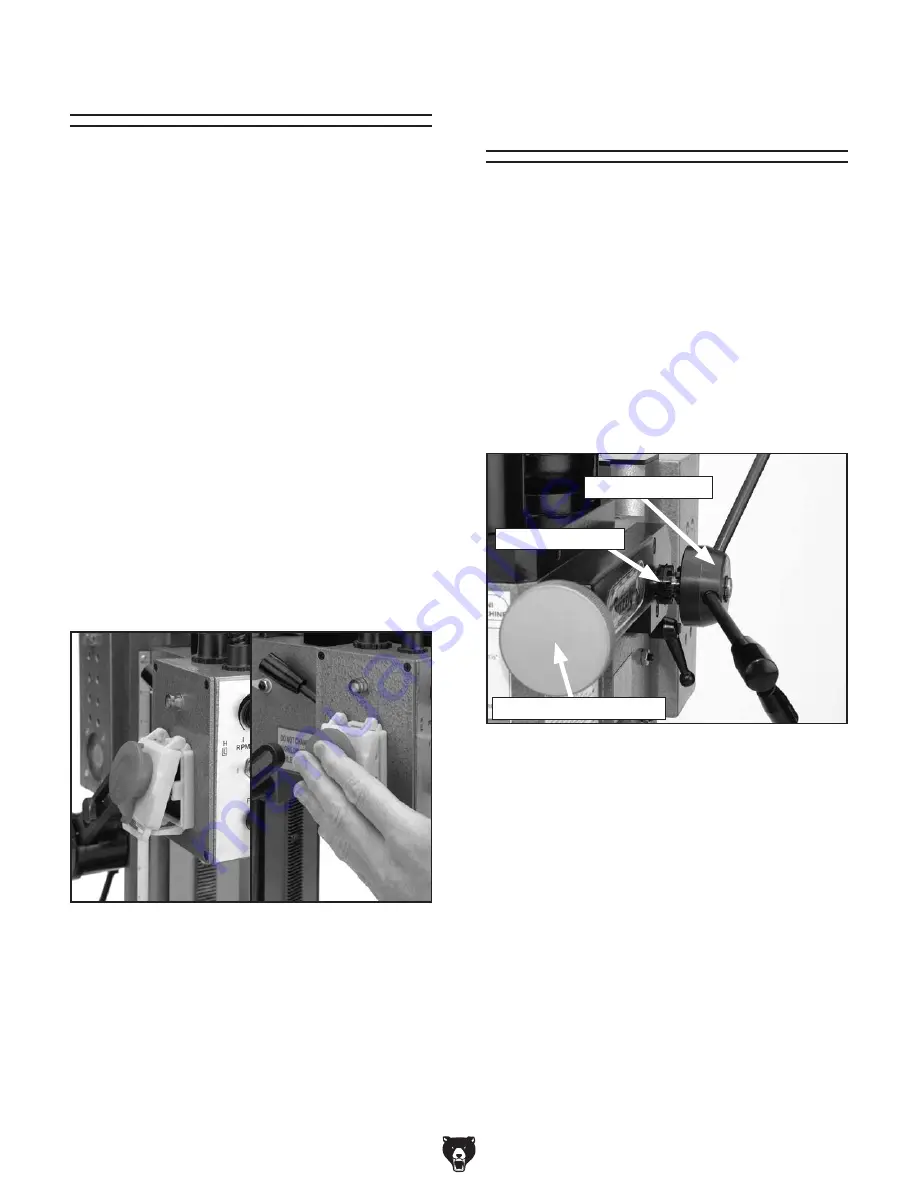
G8689 Mini Mill (Mfg. 8/06+)
-19-
Power Shutdown
It is important to shut the power
OFF when the
mill is not in use. Leaving the power
ON keeps
the circuit board cooling fan running. This will
cause unnecessary wear on the fan and electrical
system.
To completely shut the system power OFF:
1. Turn the SPINDLE ON & RPM Control Knob
OFF.
2. Turn the SYSTEM ON Toggle Switch OFF.
3. Press the EMERGENCY STOP BUTTON.
At this point the green power light and the
amber fan power light should not be lit.
Note: The EMERGENCY STOP Button is
a flap style button that lays over the switch.
Closing the flap shuts
OFF power to the
system. The system can be re-activated by
opening the switch cover. This is done by
pushing in and up on the button and allowing
the inner button to release.
Rapid & Micro
Downfeed Controls
The Model G8689 spindle height is controlled by
two methods. The rapid downfeed works similar
to a drill press. The micro downfeed will allow you
to make adjustments to 0.001". One full revolution
is 0.060".
To use the rapid downfeed:
1. Make sure the column lock is released from
the head.
2. Pull the downfeed handle hub out to disen-
gage the teeth as shown in
Figure 13.
3. Turn the levers to lower and raise the head.
To use the micro downfeed:
1. Make sure the column lock is released from
the head.
2. Push the feed handle hub in so the teeth
engage.
3. Turn the micro downfeed knob to the desired
depth.
Figure 12. EMERGENCY STOP Button.
Figure 13. Downfeed handle.
Downfeed Hub
Downfeed Teeth
Micro Downfeed Knob
Summary of Contents for G8689
Page 15: ...G8689 Mini Mill Mfg 8 06 13 Hardware Recognition Chart...
Page 40: ...38 G8689 Mini Mill Mfg 8 06...
Page 44: ......