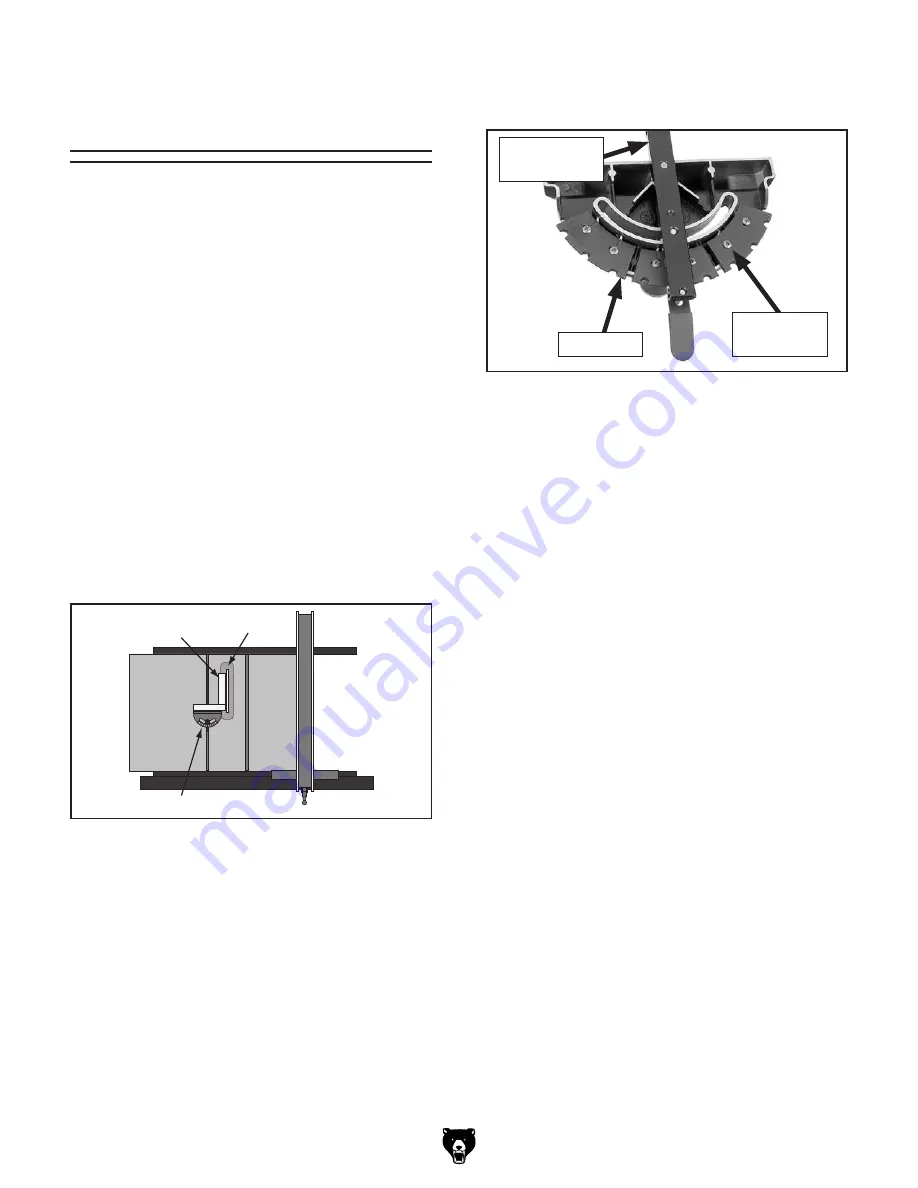
Model G0771 (Mfd. Since 8/15)
-67-
Miter Gauge
Adjustments
The miter gauge is equipped with stop screws that
allow you to easily adjust the miter gauge 0°– 30°
left, 90°, and 0°–45° right. The stop screws con-
tact the shaft, which moves in or out of the way
for adjustments.
Tools Needed
Qty
Phillips Head Screwdriver .................................. 1
90° Square ........................................................ 1
45° Square ........................................................ 1
30° Square ........................................................ 1
Wrench 8mm ..................................................... 1
Checking/Setting 90° Stops
1. DISCONNECT SAW FROM POWER!
2. Slide miter gauge into T-slot on table.
3. Place square evenly against face of miter
gauge and blade, as shown in
Figure 129.
Figure 129. Checking 90° stop on miter gauge.
Square
Miter Gauge
Blade
— If square touches miter body and body of
blade evenly at same time, then it is square
to blade. No adjustments are necessary.
— If square does not touch miter body and
blade evenly, then proceed to
Step 5.
4. Remove miter gauge from miter slot.
Checking/Setting 45° Stops
Follow the same process with the 45° and 30°
stops that you followed with the 90°, except using
a 45° square or adjustable square to verify that
the miter body is 45° to the blade.
Figure 130. Checking 45° stop on miter gauge.
6. Using a square, position miter shaft at 90° to
miter gauge body.
7. Tighten stop plate screws.
Miter Gauge
Shaft
Stop Plate
Adjustment
Screws
5. Loosen two Phillips head screws that secure
90° stop plate (see
Figure 130).
Summary of Contents for G0771
Page 84: ......