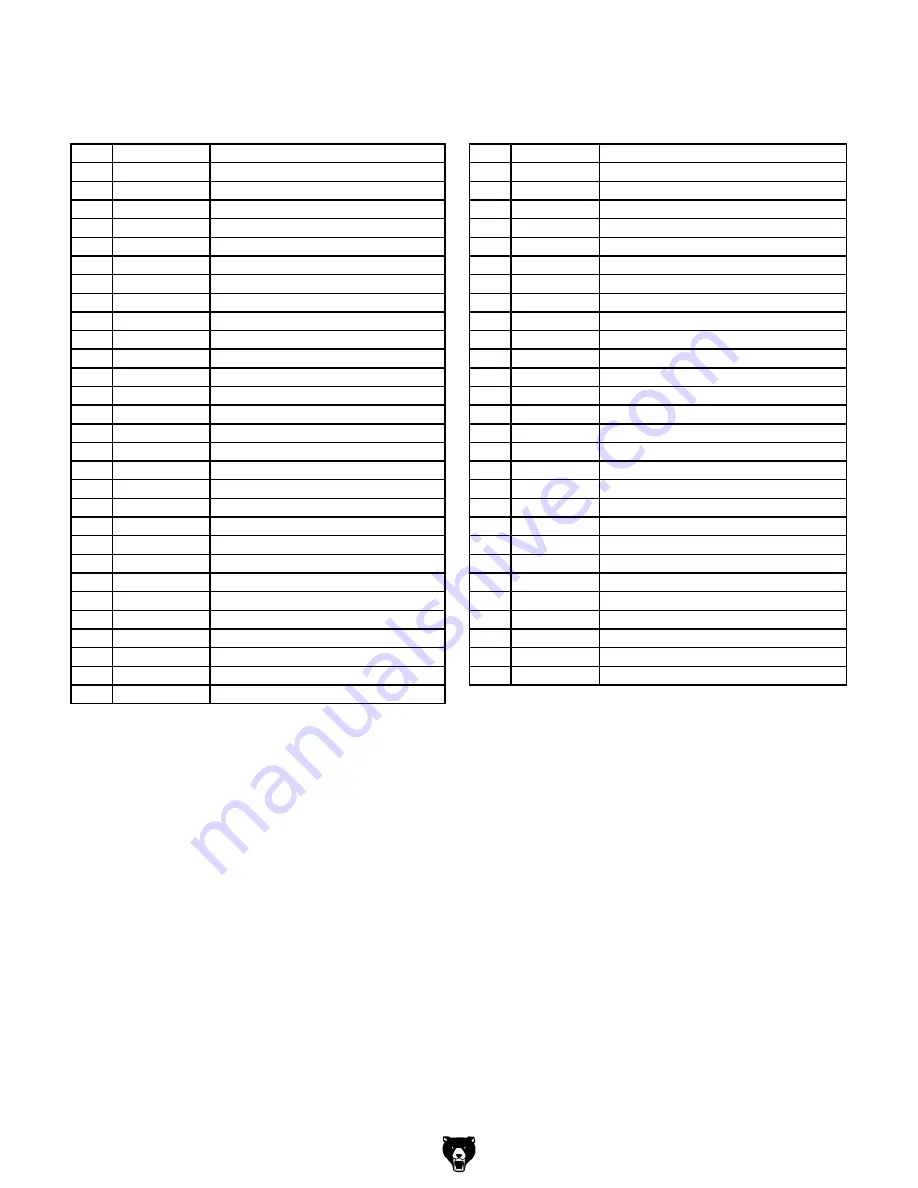
-50-
Model G0705 (Mfg. since 09/09)
headstock parts list (continued)
REF PART #
DESCRIPTION
REF PART #
DESCRIPTION
48
PCAP05
CAP SCREW 1/4-20 X 3/4
80
P0705080
PULLEY IDLER PLATE
49
P0705049
ELEVATION CRANK
81
PN04
HEX NUT 5/8-11
51
P0705051
CLAMP HANDLE
82
PW07
FLAT WASHER 5/16
52
P0705052
OUTER QUILL CLAMP
83
PCAP08
CAP SCREW 5/16-18 X 1-1/2
53
P0705053
INNER QUILL CLAMP
84
P0705084
IDLER PULLEY
54
P0705054
QUILL CLAMP SPACER
85
PN04
HEX NUT 5/8-11
55
P0705055
QUILL CLAMP HANDLE
86
P0705086
MOTOR PULLEY SET
56
P0705056
SCREW KEY
88
PVA33
V-BELT A33
57
PN08
HEX NUT 3/8-16
89
PVA39
V-BELT A39
58
P0705058
COMPRESSION SPRING
90
P0705090
WIRE CLIP
59
P0705059
BELT TENSION PIN
91
PCAP09
CAP SCREW 5/16-18 X 5/8
60
P0705060
RUBBER PAD
92
P0705092
MOTOR MOUNT PLATE
61
PB46
HEX BOLT 5/8-11 X 6
93
P0705093
MOTOR 2HP 110/220V 1-PH
62
PW14
FLAT WASHER 5/8
93-1
P0705093-1
MOTOR JUNCTION BOX
63
PN04
HEX NUT 5/8-11
93-2
PC150D
S CAPACITOR 150M 250V 1-5/8 X 3-1/4
64
P0705064
HEADSTOCK WRENCH
93-3
PC20B
R CAPACITOR 20M 450V 1-5/8 X 3-1/4
65
P0705065
LOCK HANDLE M8-1.25 X 25
93-4
P0705093-4
MOTOR FAN
66
P0705066
FRONT COVER PLATE ASSEMBLY
93-5
P0705093-5
MOTOR FAN COVER
67
PCAP04
CAP SCREW 1/4-20 X 1/2
94
PW07
FLAT WASHER 5/16
68
P0705068
LIMIT PLATE
95
PB03
HEX BOLT 5/16-18 X 1
69
PW18
FLAT WASHER #5
96
PN02
HEX NUT 5/16-18
70
PS50
PHLP HD SCR 5-40 X 1/4
97
PB36
HEX BOLT 7/16-14 X 3/4
71
P0705071
BELT COVER
98
PK109M
KEY 7 X 7 X 35
72
P0705072
LOWER BELT PLATE
99
P0705099
GUARD BRACKET
74
P0705074
SPINDLE COVER
100
PCAP03M
CAP SCREW M5-.8 X 8
75
PCAP158M
CAP SCREW M3-.5 X 16
101
PCAP26M
CAP SCREW M6-1 X 12
76
PW07
FLAT WASHER 5/16
102
P0705102
PROTECTIVE PLATE
77
PB32
HEX BOLT 5/16-18 X 5/8
113
P0705113
CHUCK B16 1–13MM
78
PCAP04
CAP SCREW 1/4-20 X 1/2
113-1 P0705113-1
CHUCK KEY
79
P0705079
SPEED CHART
Summary of Contents for G0760
Page 62: ......