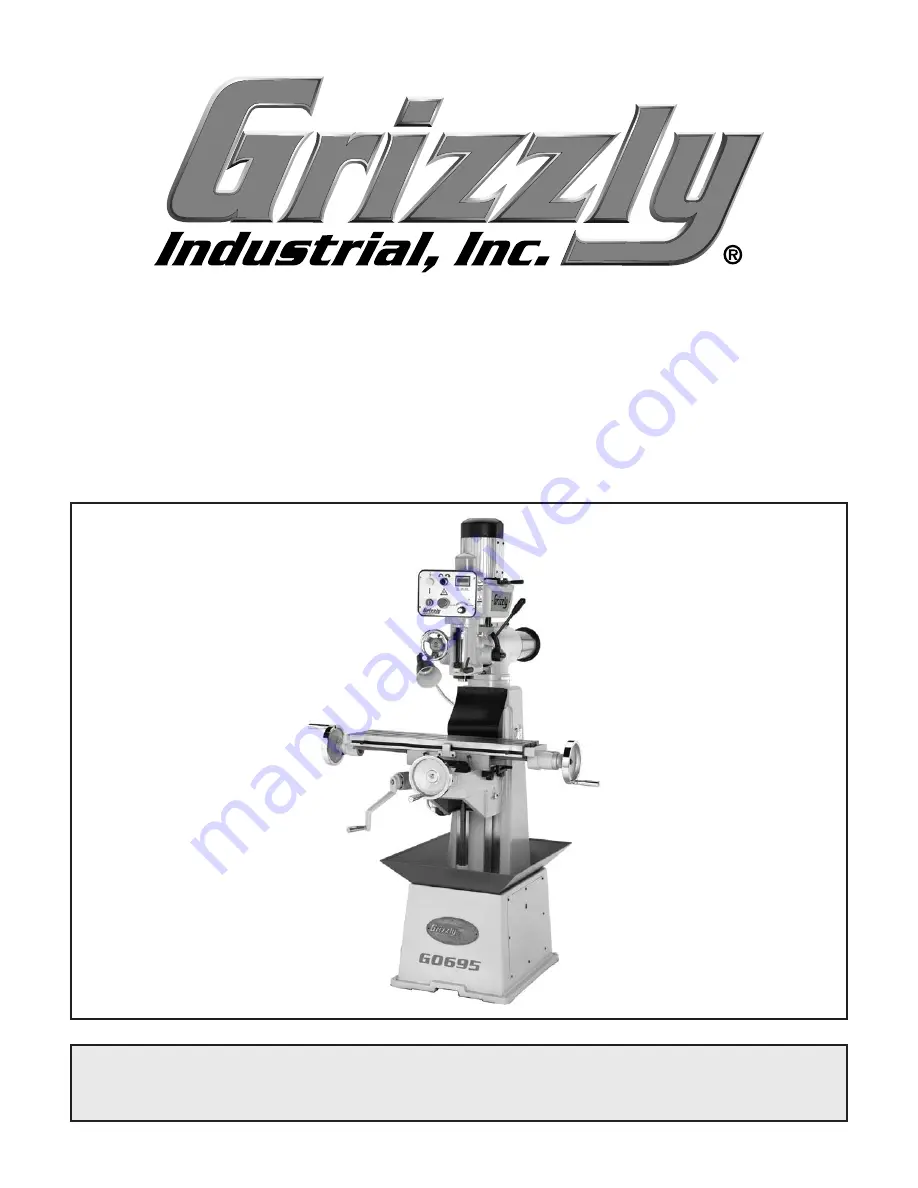
COPYRIGHT © JULY, 2009 BY GRIZZLY INDUSTRIAL, INC., REVISED SEPTEMBER, 2019 (RS)
WARNING: NO PORTION OF THIS MANUAL MAY BE REPRODUCED IN ANY SHAPE
OR FORM WITHOUT THE WRITTEN APPROVAL OF GRIZZLY INDUSTRIAL, INC.
#TRCRBLTSJB11908 PRINTED IN TAIWAN
V2.09.19
MODEL G0695
VS MILLING MACHINE w/RAM HEAD
OWNER'S MANUAL
(For models manufactured since 01/17)
Summary of Contents for G0695
Page 56: ......