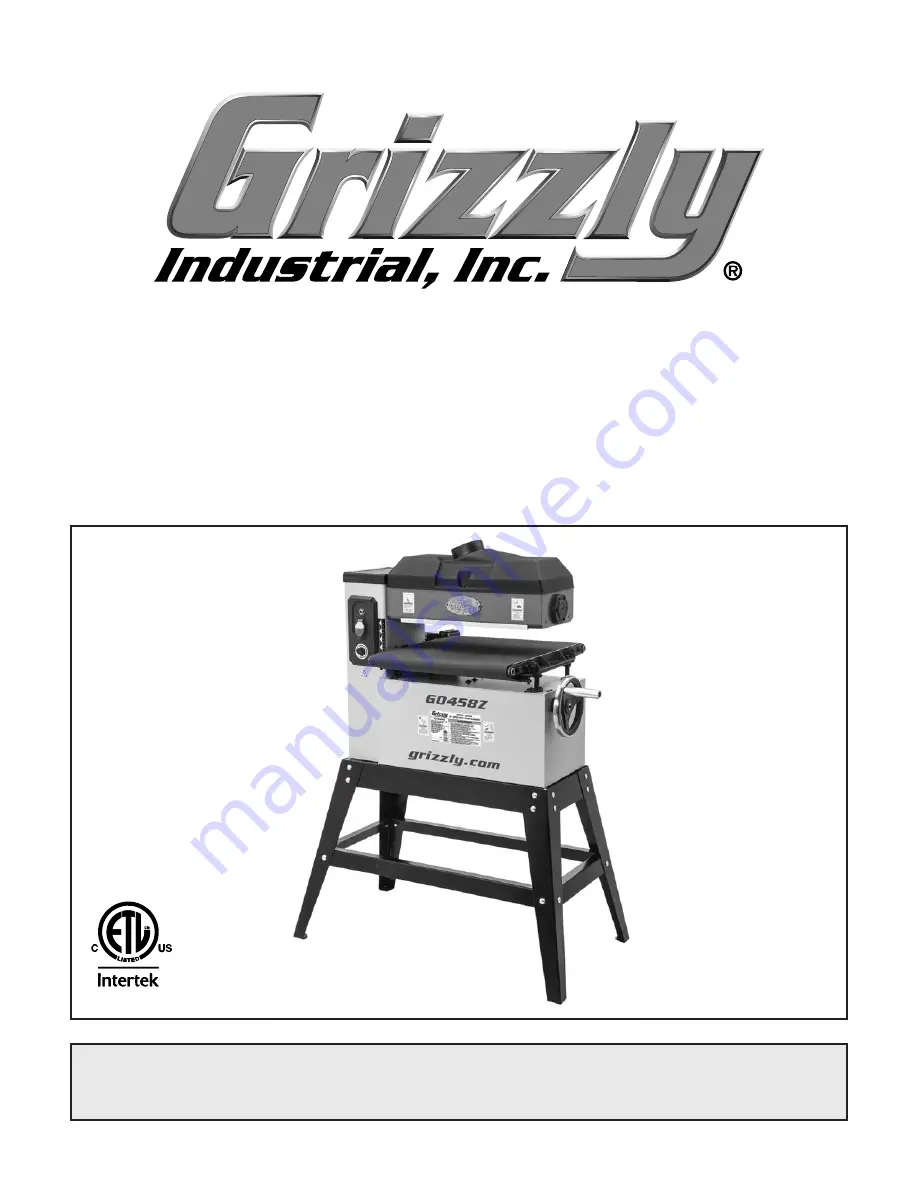
MODEL G0458Z
18" OPEN-END DRUM SANDER
OWNER'S MANUAL
(For models manufactured since 7/19)
COPYRIGHT © MARCH, 2018 BY GRIZZLY INDUSTRIAL, INC., REVISED OCTOBER, 2019 (MN)
WARNING: NO PORTION OF THIS MANUAL MAY BE REPRODUCED IN ANY SHAPE
OR FORM WITHOUT THE WRITTEN APPROVAL OF GRIZZLY INDUSTRIAL, INC.
#JHAB19391 PRINTED IN CHINA
V2.10.19
3092372