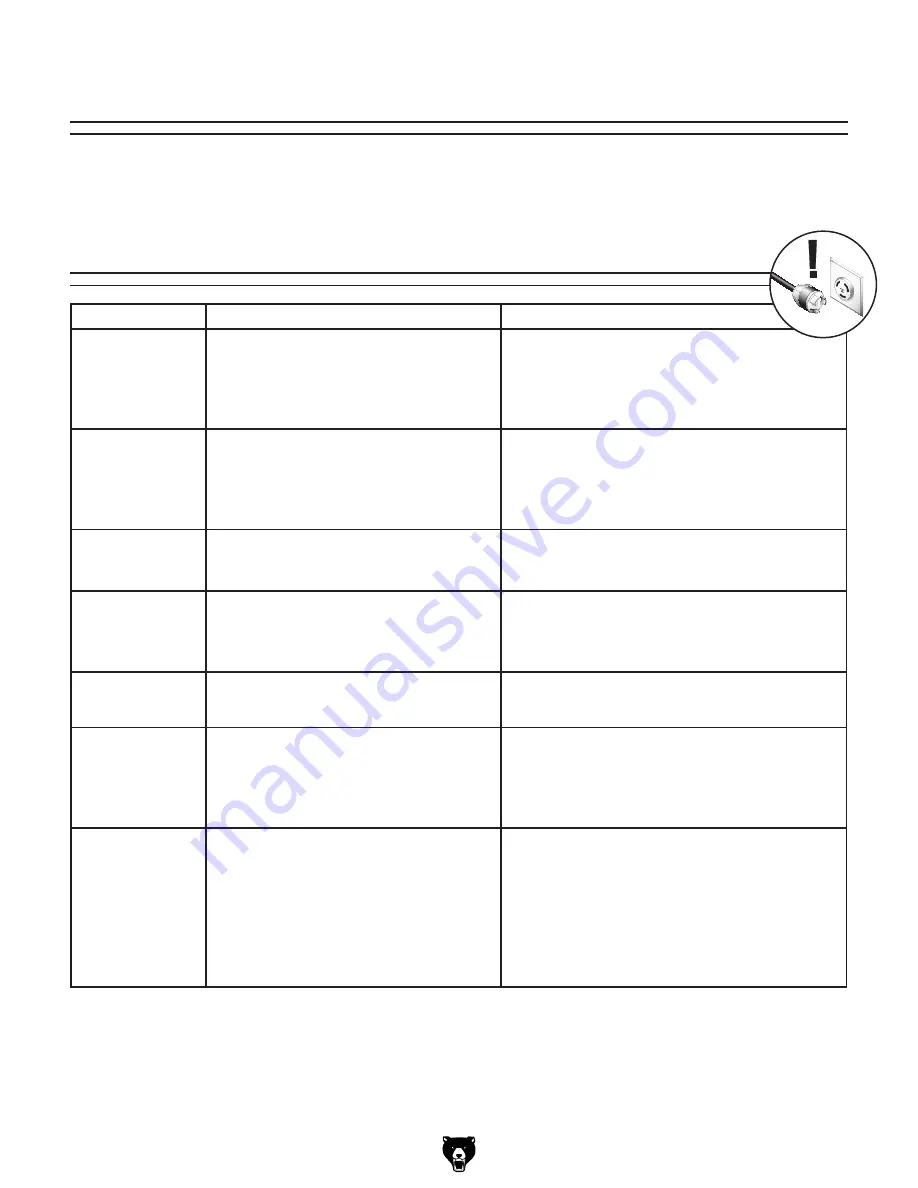
H8151 230V Mini Welder
-13-
Review the troubleshooting and procedures in this section to fix or adjust your machine if a problem devel-
ops. If you need replacement parts or you are unsure of your repair skills, then feel free to call our Technical
Support at (570) 546-9663.
SECTION 6: SERVICE
Troubleshooting
Symptom
Possible Cause
Possible Solution
Welder does not
power up or the
breaker trips.
1. Plug/receptacle is at fault or wired incor-
rectly.
2. Wiring is open/has high resistance.
3. ON/OFF switch is at fault.
1. Test for good contacts; correct the wiring.
2. Check for broken wires or disconnected/corroded
connections, and repair/replace as necessary.
3. Replace faulty ON/OFF switch.
Porosity; small cavi-
ties or holes caused
from gas packets in
weld.
1. Arc length is too long.
2. Workpiece is dirty.
3. Damp electrodes.
4. Incorrect electrode used.
1. Reduce length of arc.
2. Remove all grease, oil, moisture, coatings, rust, and
dirt from workpiece before welding.
3. Use dry electrodes.
4. Use correct type and size of electrode.
Excessive spatter.
1. Amperage too high for electrode.
2. Voltage too high; arc length too long.
3. Incorrect electrode used.
1. Select large electrode or decrease amperage.
2. Reduce voltage or arc length.
3. Use correct type and size of electrode.
Distortion of base
metal.
1. Excessive heat applied to base metal.
1. Make tack welds along joint before starting opera-
tion; select lower amperage for electrode; increase
travel speed; weld in small segments and allow cool-
ing between welds.
Burn through or
excessive penetra-
tion of base metal.
1. Excessive heat applied to base metal.
1. Select lower amperage; use smaller electrode;
increase and/or maintain steady travel speed.
Lack of penetration. 1. Improper joint preparation.
2. Improper weld technique.
3. Insufficient heat applied to weld.
1. Material too thick; joint preparation must provide
access to bottom of groove.
2. Keep arc on leading edge of weld puddle; reduce
travel speed.
3. Increase amperage; select larger electrode.
Failure of weld to
fuse completely with
base metal or prior
weld bead.
1. Insufficient heat applied to weld.
2. Improper welding technique.
3. Workpiece dirty.
4. Duty cycle exceeded.
1. Increase amperage; select larger electrode.
2. Widen groove to access bottom during welding;
keep arc on leading edge of weld puddle; place
stringer bead in proper location at joint during weld-
ing.
3. Remove all grease, oil, moisture, coatings, rust, and
dirt from workpiece before welding.
4. Shut down welder and allow it to cool.
Troubleshooting