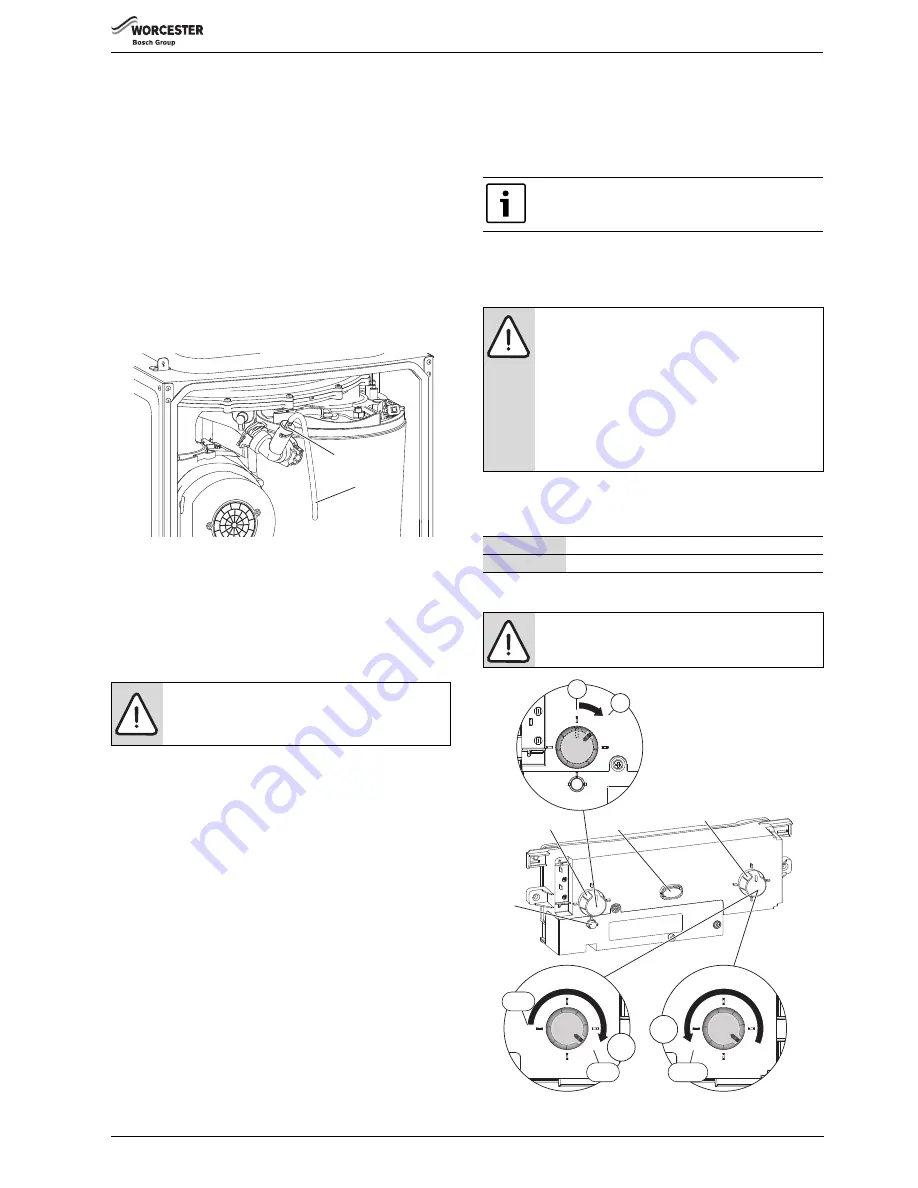
COMMISSIONING
Greenstar Ri
ErP
- 6 720 813 283 (2015/07)
29
6.2
FILLING THE SYSTEM
Open vented systems:
▶ Ensure all system and boiler drain points are closed.
▶ Open all radiator valves.
▶ Turn on the water supply to the system header tank and allow the
system to fill.
Sealed systems:
▶ Fill the system via a WRAS approved filling loop to 1 bar then turn the
valve anti-clockwise to close.
Opened vented and sealed systems:
▶ Vent (1) any air from the boiler heat exchanger using a suitable
container to collect any water. Ensure tube outlet (2) is directed away
from the fan or any other electrical component to prevent any water
damage. Also place a suitable cover over the fan to prevent any
spillage of water on to electrical connections. Ensure the cover is
removed after venting.
Fig. 40 Venting
▶ Vent all radiators and the primary side of the hot water cylinder,
tighten when completed and check the system and correct any leaks.
Sealed systems only:
▶ If required increase system pressure back to 1 bar.
▶ Isolate and remove filling loop connection to system.
6.3
WATER TREATMENT
It is possible to have an ion exchange water softener fitted to the cold
water system of the property. However, the boiler requires an untreated
cold water connection taken from the mains supply, before the water
softener, to the primary water filling point of the heating system.
Alternatively there are water softening/treatment devices that do not
adjust or alter the pH levels of the water. With these devices it may not
be necessary to provide an untreated water by-pass to the primary water
filling point of the heat system.
ENSURE THAT THE SYSTEM HAS BEEN CLEANED AS ON PAGE 11 OF
THESE INSTRUCTIONS
.
FLUSHING (Central Heating):
▶ Switch off the boiler.
▶ Open all drain cocks and drain the system while the appliance is hot.
▶ Close drain cocks and add a suitable flushing agent at the correct
strength for the system condition in accordance with the
manufacturer's instructions.
▶ Run the boiler/system at normal operating temperature for the time
stated by the manufacturer of the flushing agent.
▶ Drain and thoroughly flush the system to remove the flushing agent
and debris.
INHIBITOR (Central Heating):
▶ Check drain cocks are closed and all radiator valves are open before
adding a suitable inhibitor compatible with aluminium (or combined
inhibitor/anti-freeze if the system is exposed to freezing conditions)
to the heating system water in accordance with the manufacturers
instructions.
▶ Fill system as described in section 6.2 opposite.
▶ Set all controls to maximum.
▶ Record the date when the inhibitor was added to the system on the
warrantee card.
WATER TREATMENT PRODUCTS
Suitable water treatment products can be obtain from the following
manufacturers:
6.4
STARTING THE APPLIANCE
Fig. 41 Boiler controls
NOTICE:
▶ ARTIFICIALLY SOFTENED WATER MUST NOT BE
USED TO FILL THE CENTRAL HEATING SYSTEM.
6720804530-12.1Wo
1
2
The pH value of the system water must be less than 8 or
the appliance warrantee will be invalidated.
NOTICE:
▶ The concentration of inhibitor in the system should be
checked every 12 months or sooner if system content
is lost.
▶ Normally the addition of sealing agents to the system
water is not permitted as this can cause problems
with deposits left in the heat exchanger.
▶ In cases where all attempts to find a micro leak have
failed, Worcester, Bosch Group supports the use of
Fernox F4 leak sealer.
FERNOX
0870 601 5000 or www.fernox.com
SENTINEL
0800 389 4670 or www.sentinel-solutions.net
CAUTION:
RUNNING THE APPLIANCE
▶ Never run the appliance when the appliance/system is
empty or partially filled.
1
2
3
4
1.
0
1
1
0
MIN
RESET
MAX
max
min
2.
MIN
RESET
MAX
reset
3.
6720644744-30.1W
o
Summary of Contents for 12Ri ErP
Page 52: ...Greenstar Ri ErP 6 720 813 283 2015 07 52 NOTES...
Page 53: ...Greenstar Ri ErP 6 720 813 283 2015 07 53 NOTES...
Page 54: ......
Page 55: ......