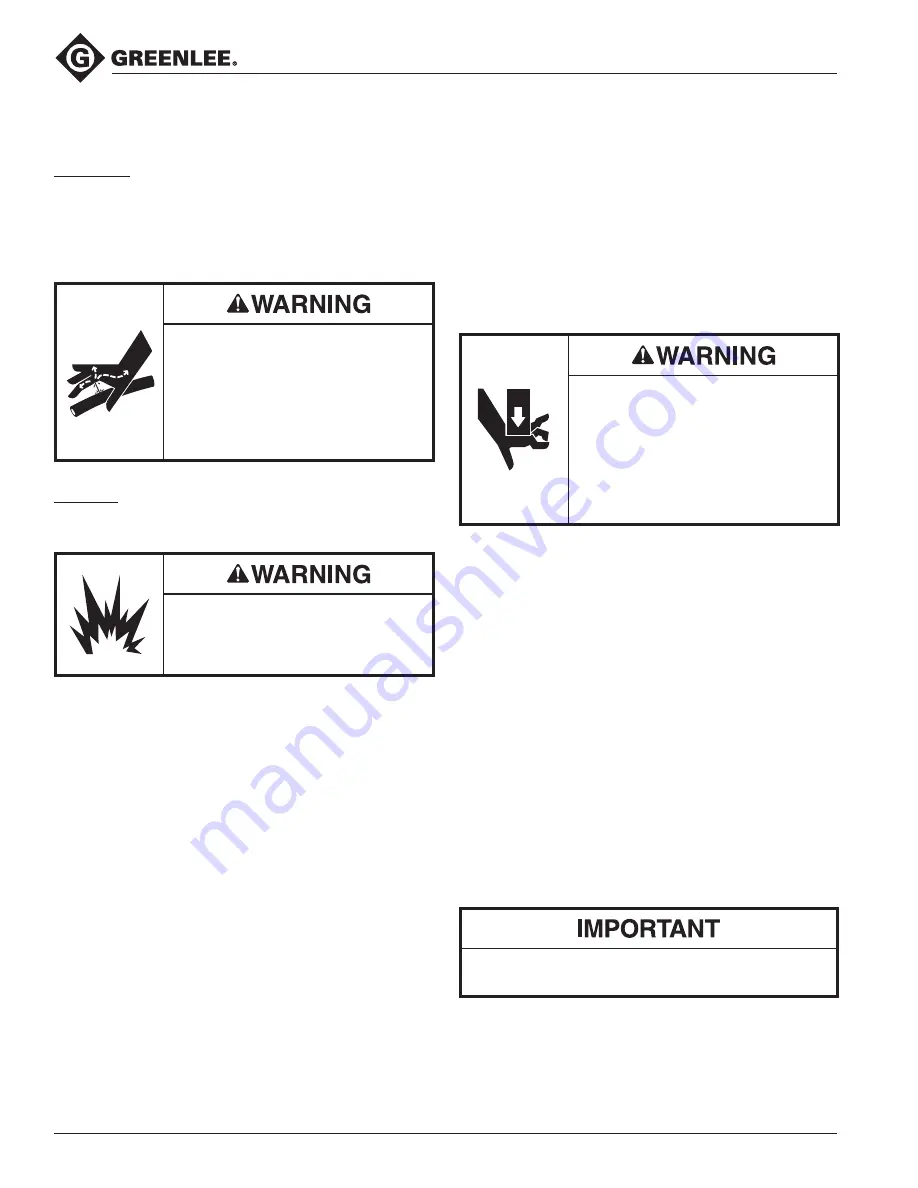
E12CCX 12-ton Battery-powered, High-speed Tool
Greenlee / A Textron Company
4455 Boeing Dr. • Rockford, IL 61109-2988 USA • 815-397-7070
16
Maintenance
Each Operating Day
Before use:
1. Inspect dies and adapters for wear or damage such
as cracks, gouges, or chips.
2. Inspect the tool for damage or leaks. If damage is
detected, return the tool to an authorized Greenlee
service center for inspection.
High pressure hazard:
Do not use fingers or hands to check
for oil leaks. High pressure oil easily
punctures skin causing serious injury,
gangrene, or death.
If injured, seek medical help immedi-
ately to remove oil.
After use:
1. Wipe all tool surfaces clean with a damp cloth and
mild detergent.
Do not use solvents or flammable
cleaners to clean the tool body.
Solvents could ignite, causing serious
injury or property damage.
2. Place tool in the carrying case. Store in a cool,
dry place.
3. Charge the battery.
Monthly
1. Thoroughly clean all surfaces.
2. Check the oil level.
3. Oil the bolt joints.
Annually or After 10,000 Cycles
1. Change the hydraulic oil.
2. Return the tool to an authorized Greenlee service
center for inspection.
Checking the Oil Level
1. Remove the two screws holding the tank housing
cover.
2. Remove the tank housing cover.
3. Point the cutting head towards the ground and
remove the oil plug. Add oil if necessary.
4. Replace the oil plug and the tank housing cover.
Secure with screws.
Recommended Hydraulic Oils
AVIA
®
HVI 15
Shell Tellus T 15
Mobil
®
DTE 11M
NUTO
®
H 15
Periodic Pressure Relief Valve Check
Pinch points:
•
Remove battery before changing
dies, adapters, or jaws.
• Keep hands away from the crimp-
ing tool head when crimping.
Failure to observe these warnings
could result in severe injury or death.
The crimping tool’s relief valve may require occasional
adjustment. To determine whether this adjustment is
necessary, periodically test the crimping tool with a
Greenlee model 35887 Load Cell (purchased
separately).
1. Insert the test die into the tool (refer to steps 3 and
4 under “Operation” in this manual). Position the
load cell so that the load cell piston is centered
between the two test dies.
2. Press the trigger until the crimping tool achieves
pressure relief and note the position of the needle
when the pressure relief is achieved. The needle
should indicate the “12T” range; if the needle is
outside of this range, send the crimping tool to an
authorized service center for adjustment.
Note: If some other type of load cell is used, the ratio
between the area of the tool and the area of the load cell
may be different. The appropriate corresponding pres-
sure range depends upon this ratio.
Relief valve adjustments must be done by an
authorized service center.