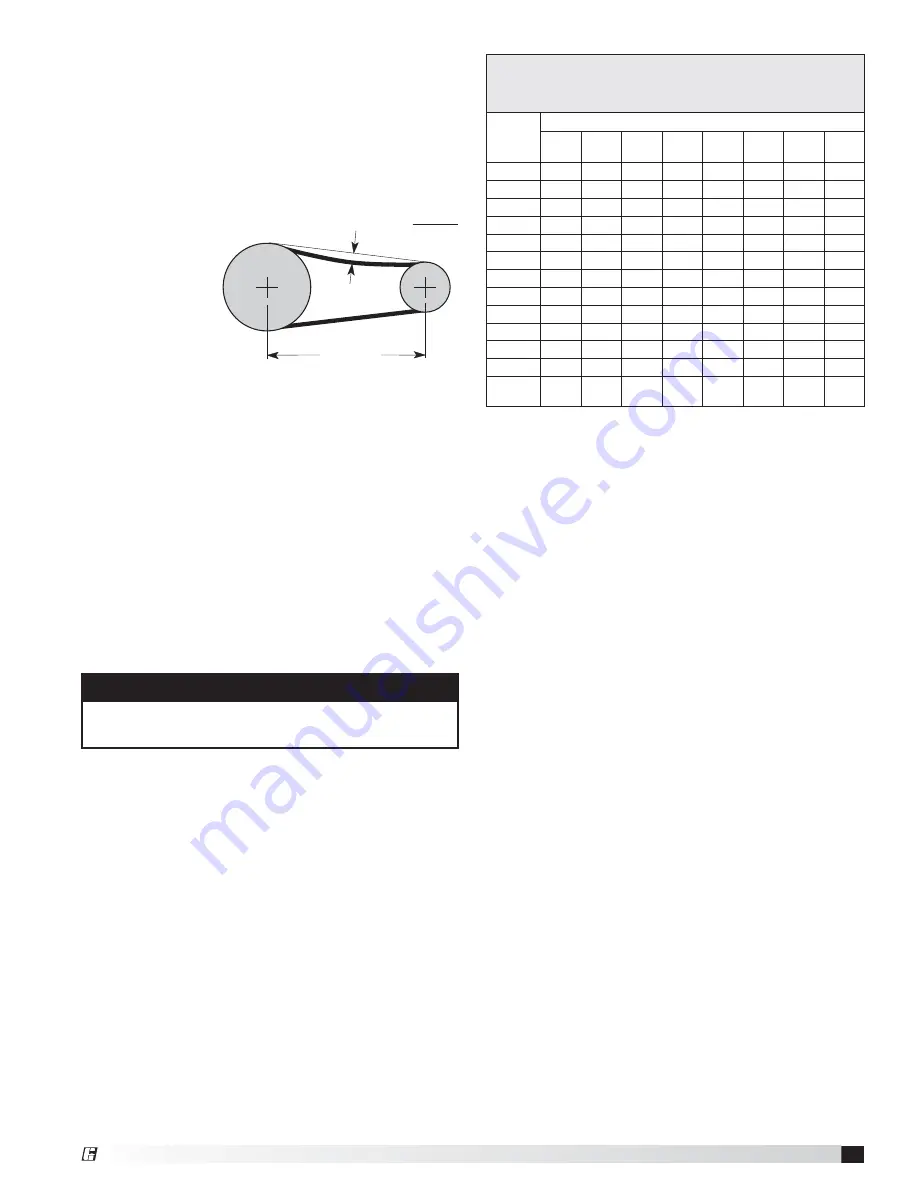
15
Laboratory Exhaust Systems
®
Recommended Bearing Lubrication Schedule
Relubrication Schedule in Months*
Synthetic Grease
Fan
RPM
Bearing Bore (inches)
1
⁄
2
-
1
1
1
⁄
8
-
1
1
⁄
2
1
5
⁄
8
-
1
7
⁄
8
1
15
⁄
16
-
2
3
⁄
16
2
7
⁄
16
- 3
3
3
⁄
16
-
3
1
⁄
2
3
15
⁄
16
-
4
1
⁄
2
4
15
⁄
16
-
5
1
⁄
2
To 250
12
12
12
12
12
12
12
12
500
12
12
12
12
12
12
12
12
750
12
12
12
12
12
12
10
7
1000
12
12
12
12
12
9
6
4
1250
12
12
12
12
9
6
4
2
1500
12
12
12
10
7
4
2
2000
12
10
8
6
3
1.5
.5
2500
12
7
5
4
1
.5
3000
12
5
3
2
.5
3500
12
3
2
.75
4000
12
2
.5
5000
12
1
Number
of shots**
4
8
8
10
16
25
41
57
* Lubrication interval is based on 12 hour day operation and
maximum 160°F housing temperature. For 24 hour per day
operation, the interval should be cut in half.
** Lubricant should be added with the shaft rotating and
until clean grease is seen purging from the bearing. The
lubrication interval may be modified based on the condition
of the purged grease. If bearing is not visible to observe
purged grease, lubricate with number of shots indicated for
bore size.
• For conditions including high temperatures, moisture, dirt
or excessive vibration, consult the factory for a specific
lubrication interval for your application.
• Lubricant should be a high quality lithium complex synthetic
grease conforming to NLGI Grade 2. Factory recommends
synthetic Mobilith SHC100.
• The use of non-synthetic lubricants will decrease lubrication
intervals by approximately three times.
• Storage periods of three months or longer require monthly
rotation of the shaft and purging grease prior to storage and
start-up.
Vektor-MS Nozzle Bearings
The bearings for the Vektor-MS nozzle assembly are
permanently lubricated and do not require additional
grease.
Motors
Motor maintenance is generally limited to cleaning
and lubrication. Cleaning should be limited to exterior
surfaces only. Removing dust and grease buildup on
the motor housing assists proper motor cooling. Never
wash-down motor with high pressure spray.
Greasing of motors is only intended when fittings are
provided. Motors supplied with grease fittings should
be greased in accordance with the manufacturer’s
recommendations. When motor temperature does not
exceed 104ºF (40ºC), the grease should be replaced
after 2000 hours of running time.
Fans have extended grease lines to lubricate the motor
without removal of any guarding.
Bearings (Arrangement 9)
The bearings for Vektor fans are carefully selected to
match the operating conditions of the specific class,
arrangement, and fan size. The instructions provided
in this manual and those provided by the bearing
manufacturer will minimize any bearing problems.
Bearings are the most critical moving part of the fan,
therefore, special care is required when mounting them
on the unit and maintaining them.
Refer to the following chart and the manufacturer’s
instructions for grease types and intervals for various
operating conditions. Never mix greases made with
different bases. This will cause a breakdown of the
grease and possible failure of the bearing.
Failure to follow recommendations may result in
premature bearing failure and is not covered under
warranty.
Do not install new belts on worn sheaves. If the sheaves
have grooves worn in them, they must be replaced
before new belts are installed.
The proper tension for operating a V-belt drive is the
lowest tension at which the belts will not slip at peak
load conditions. Belts are adjusted by swinging out the
motor pivot plate. For initial tensioning, the proper belt
deflection halfway between sheave centers is 1/64 inch
for each inch of belt
span. For example,
if the belt span is
64 inches, the belt
deflection should
be 1 inch using
moderate thumb
pressure at mid-
point of the drive.
Check belt
tension two times during the first 24 hours of
operation and periodically thereafter.
Belt Span
Deflection =
Belt Span
64
NOTE
Motors for direct drive arrangement 4 models have
12 month lubrication intervals.