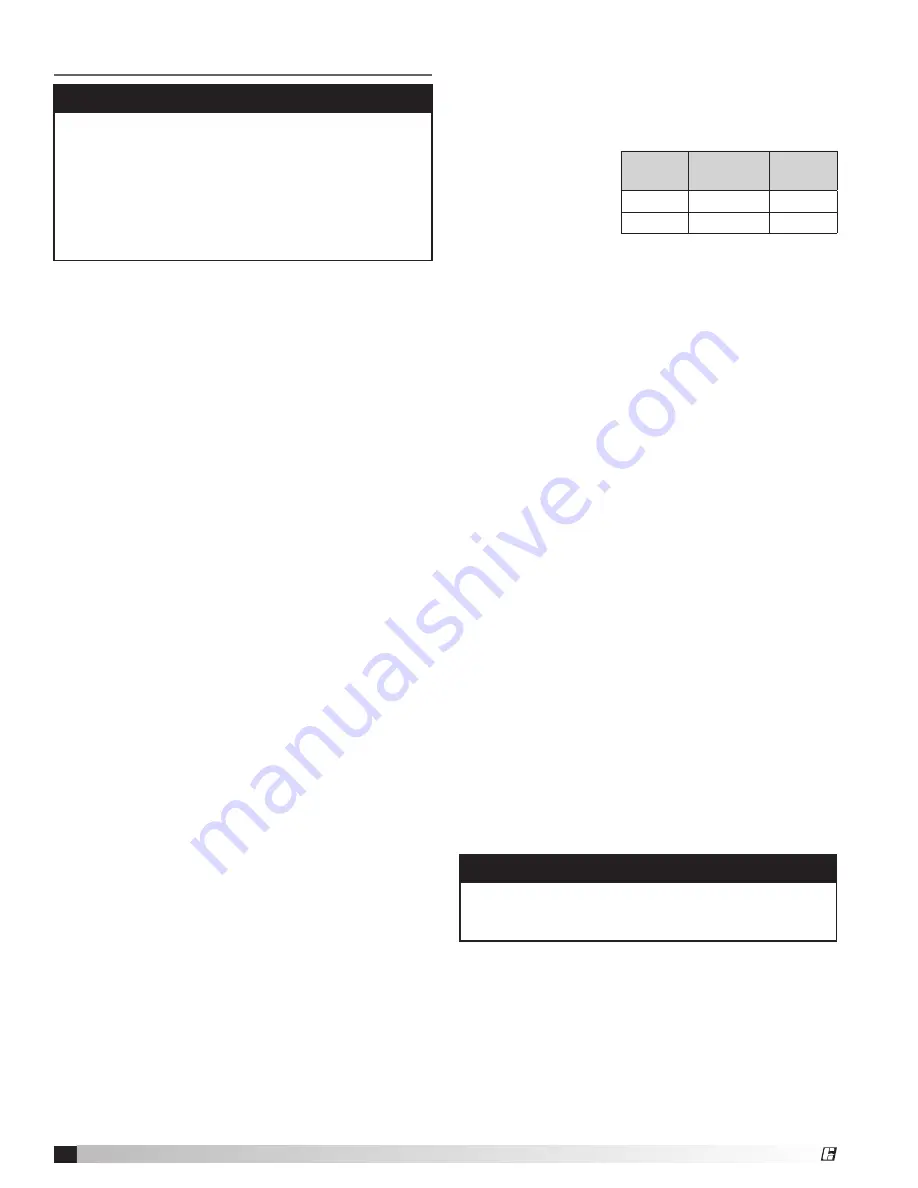
12
Energy Core Ventilator
®
Internal Filter Maintenance
Opening the access panel provides access to the two
inch deep, pleated MERV 8 (30% efficient) filters. These
filters should be checked regularly, cleaned, or replaced
as needed.
After the MiniCore
has been put into
operation, an annual
inspection and
maintenance program
should be set-up to
preserve reliability and performance.
The MiniCore energy recovery ventilator requires
very little maintenance. However, small problems left
unchecked, over time, could lead to loss of performance
or early motor failure. We recommend that the unit be
inspected once a year.
Energy Recovery Core
Annual inspection of the energy recovery core is
recommended. MiniCore units ventilating smoking
lounges or other non-clean air spaces should have
energy recovery core inspections more often based
upon needs.
Frequency of cleaning -
A regular cleaning cycle
must be established for the energy recovery core in
order to maintain optimum sensible and latent energy
transfer. In reasonably clean environments such as
schools, offices or retail stores, the energy recovery core
should be inspected annually and cleaned as needed.
Failure to follow a regular cleaning cycle for the energy
recovery core can result in significant energy transfer
performance losses.
Accessing the energy recovery core -
Disconnect
the power to the MiniCore. Remove access panel.
Removing the energy recovery core -
Once the
energy core access doors are removed, the core can
be pulled from the housing. To replace the core, reverse
the procedure.
Recommended cleaning procedure -
Once the core
is removed, gently vacuum the surfaces of the core to
remove the dirt and debris that has accumulated.
WARNING
Do not wash, soak in water or use detergents
and cleaners on the core. This will result in a
damaged core.
WARNING
Disconnect all electrical power to the MiniCore prior
to inspection or servicing. Failure to comply with this
safety precaution could result in serious injury or
death. Improper installation, adjustment, alteration,
service or maintenance can cause property damage,
injury or death. Read the installation, operating, and
maintenance instructions thoroughly before installing
or servicing this equipment.
After the MiniCore has been put into operation, an
annual inspection and maintenance program should be
set-up to preserve reliability and performance.
The MiniCore energy recovery ventilator requires
very little maintenance. However, small problems
left unchecked, over time, could lead to loss of
performance or early motor failure. We recommend that
the unit be inspected once a year.
Fasteners and Set Screws
Any fan vibration has a tendency to loosen mechanical
fasteners. A periodic inspection should include
checking all fasteners and set screws for tightness.
Particular attention should be paid to set screws
attaching the fan wheel to the shaft. Loose bearing set
screws will lead to premature failure of the fan shaft.
Removal of Dust and Dirt
The fan motor and wheel(s) should be checked for
dust and dirt accumulation. Dirt buildup clogs cooling
openings on the motor housing and causes motor
overheating. Dirt buildup can contaminate bearing
lubricant and collect on fan wheel blades causing loss
of performance or premature failure. Cleaning can be
accomplished by brushing off any dust that may have
accumulated. Under no circumstances should motors or
bearings be sprayed with steam or water. Even filtered
units can accumulate build up and should be checked
when cleaning filters.
Maintenance to these components is achieved through
the provided access panels.
Routine Maintenance
MiniCore
Internal
Filter Size
Quantity
5
15 x 20
2
10
20 x 20
2