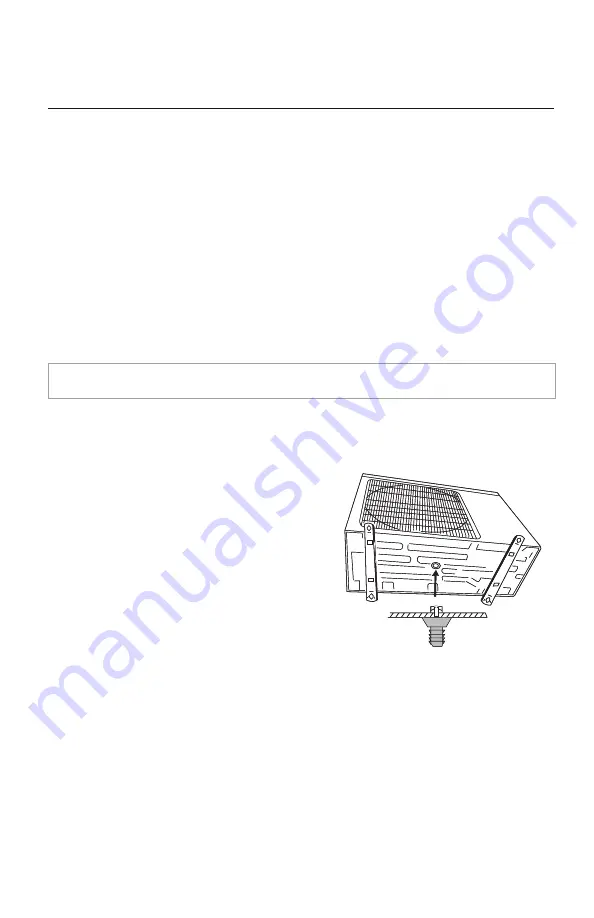
Install Ground Pad or Wall Hangers
1. Determine proper location for outdoor unit.
2. Follow all instructions provided by manufacturer for installing wall hangers or ground pad.
3. Verify the wall hangers or ground pad can safely support the weight of the outdoor unit.
4. Verify the wall hangers or ground pad is level and meets all outdoor dimensional clearances.
Install Outdoor Unit Risers
If the outdoor unit requires added elevation above the ground, installing riser legs will provide
a sturdy and stable solution. Follow all instructions provided by manufacturer for installing
riser legs to outdoor unit.
NOTE:
Riser legs will also help absorb vibrations and noise while facilitating proper drainage.
Install Condensate Drain for Outdoor Unit
During normal heating and defrost operation,
the outdoor unit will generate condensate water.
The condensate water should be routed to a safe
location through the drain hose.
1. Locate drain hole on bottom of outdoor unit.
2. Install the outdoor drain fitting into hole on
the bottom of outdoor unit as shown.
3. Connect the drain hose to drain fitting.
4. Route drain hose to safe location for proper
drainage of excess condensate water.
5. Plug the remaining drain holes in basepan with
plugs provided from factory.
OUTDOOR UNIT INSTALLATION
Drain Fitting Installation
18