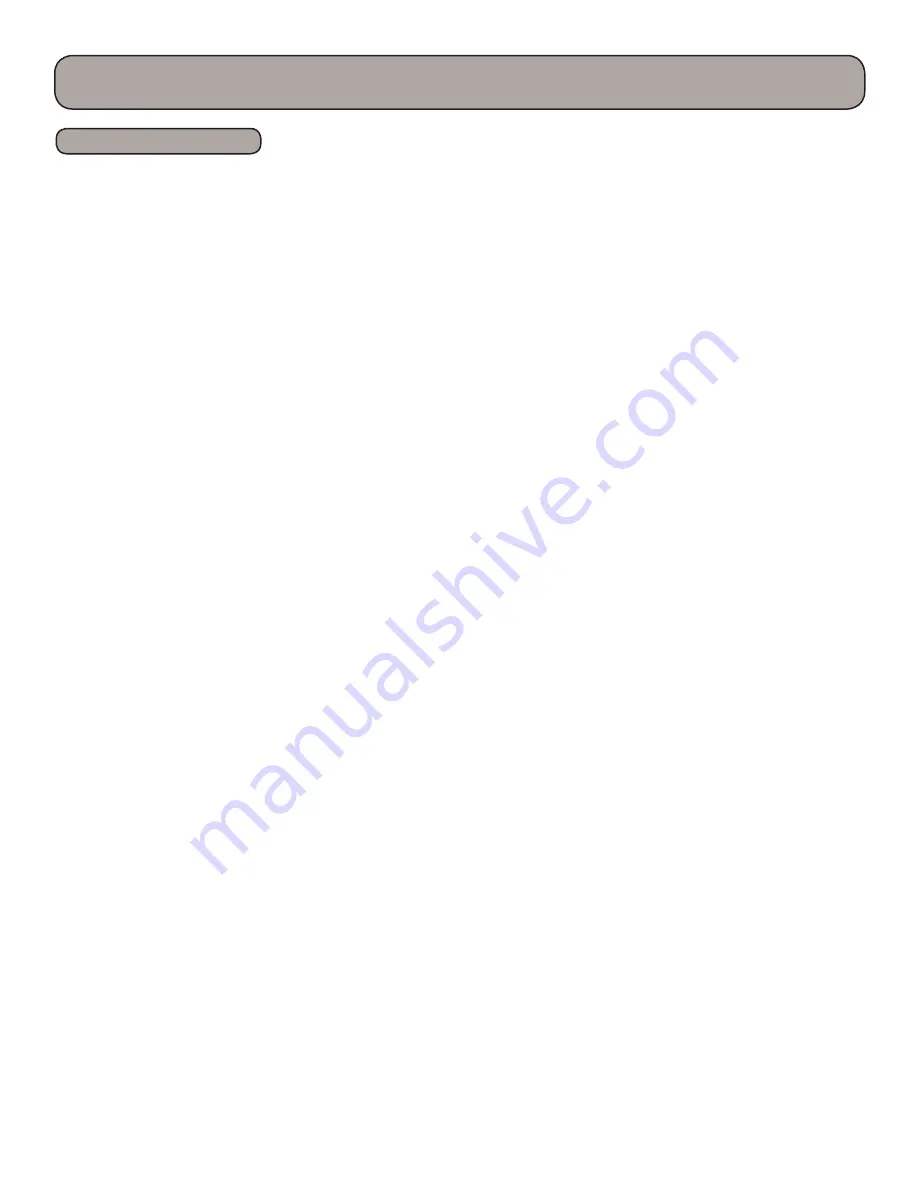
20
Common Protection Functions and Fault Displays
Coil High Temperature Protection
T
tube
= measured temperature of outdoor coil in cooling mode, measured temperature of indoor coil in heating mode.
1) Outdoor Coil High Temperature Protection
- In cooling mode the software will monitor the outdoor coil for an
abnormal high temperature condition.
A. If T
tube
<= 1260 F, the unit will return to its original operation state
B. If T
tube
>= 1310 F, frequency rise is not allowed
C. If T
tube
>= 1360 F, the compressor will run at reduced frequency
D. If T
tube
>= 1440 F, the compressor will stop and the indoor fan will operate at preset speed
2) Indoor Coil Temperature Protection
-
In heating mode the software will monitor the indoor coil for an abnormal high
temperature condition.
A. If T
tube
<= 1220 F, the unit will return to its original operation state
B. If T
tube
>= 1270 F, frequency rise is not allowed
C. If T
tube
>= 1330 F, the compressor will run at reduced frequency
D. If T
tube
>= 1400 F, the compressor will stop and the indoor fan will blow residual heat and then stop
3) Compressor Discharge Temperature Protection
The software will monitor the compressor discharge for an abnormal high temperature condition.
A. If T
tube
>= 2080 F, frequency rise is not allowed
B. If T
tube
>= 2170 F, the compressor will run at reduced frequency
C. If T
tube
>= 2300 F, the compressor will stop
D. If T
tube
<= 1940 F and the compressor has been off for at least 3 minutes, the compressor will resume operation
4) Compressor High Pressure Protection (Not available on 115v 9k & 12k models)
When the high pressure switch is detected for 6 seconds or more, the compressor will stop and can only be started by
powering off the unit. Dirty coils, refrigerant overcharge and outdoor fan problems can cause this fault.
5) Compressor Phase-lacking Protection
If one of the compressor phases are detected open before startup, the compressor will enter phase-locking protection.
The malfunction will be cleared after 1 min, then the unit will try a restart. If an error has been detected for 6 times
continuously, the compressor will lock out and will need to have power cycled. The errors will be cleared after the
compressor has run for 7 minutes continuously.
6) Module Protection (IPM)
Under module protection mode, the compressor will stop. When the compressor remains off for 3 minutes, the compressor
will resume operation. If the module protection occurs six times in succession, the compressor will remain off. Power will
need to be cycled to start unit. This is a thermal protection for the indoor module.
7) DC Buss Voltage Protection
The software will monitor the DC bus voltage.
If voltage on the DC Bus is below 150 or over 420v, the compressor will stop and the outdoor fan will stop in 30 seconds.
When the voltage on the DC bus returns to normal and the compressor has been off for 3 minutes, the compressor will
resume its operation.
Protection Functions
Basic & Protection Functions