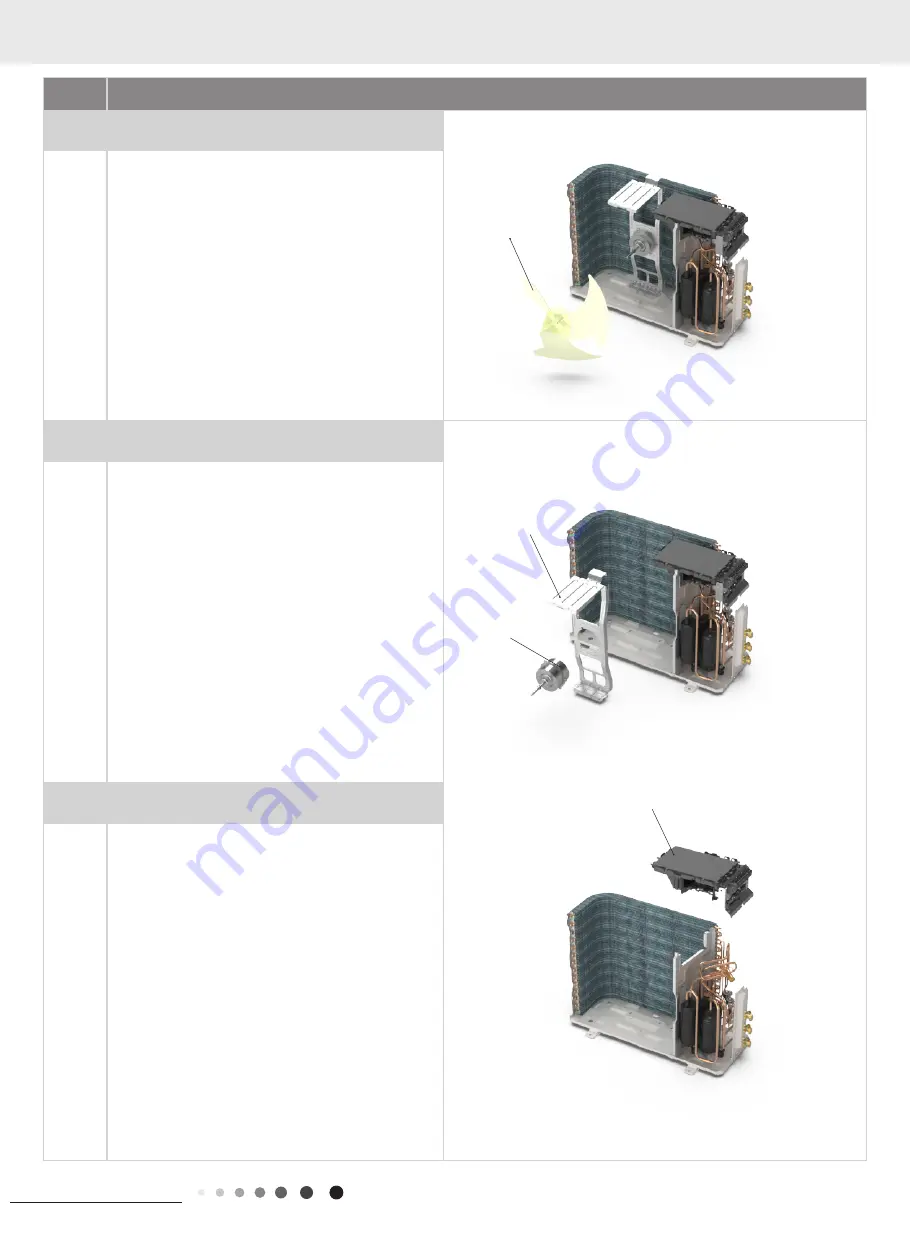
89
Installation and Maintenance
Service Manual
Step
Procedure
10. Remove axial flow blade
Remove the nut on the blade and then remove the axial
flow blade.
11. Remove motor and motor support
Remove the 4 tapping screws fixing the motor and
disconnect the leading wire insert of the motor. Then
remove the motor. Remove the 2 tapping screws fixing
the motor support and chassis, and then lift the motor
support to remove it.
12. Remove electric box assy
Remove the screws fixing the electric box assy and the
middle isolation sheet, loosen the wire bundle, unplug
the wiring terminals, and then lift the electric box assy
to remove it.
Axial flow blade
Motor support
Electric box assy
Motor
11. Removal Procedure