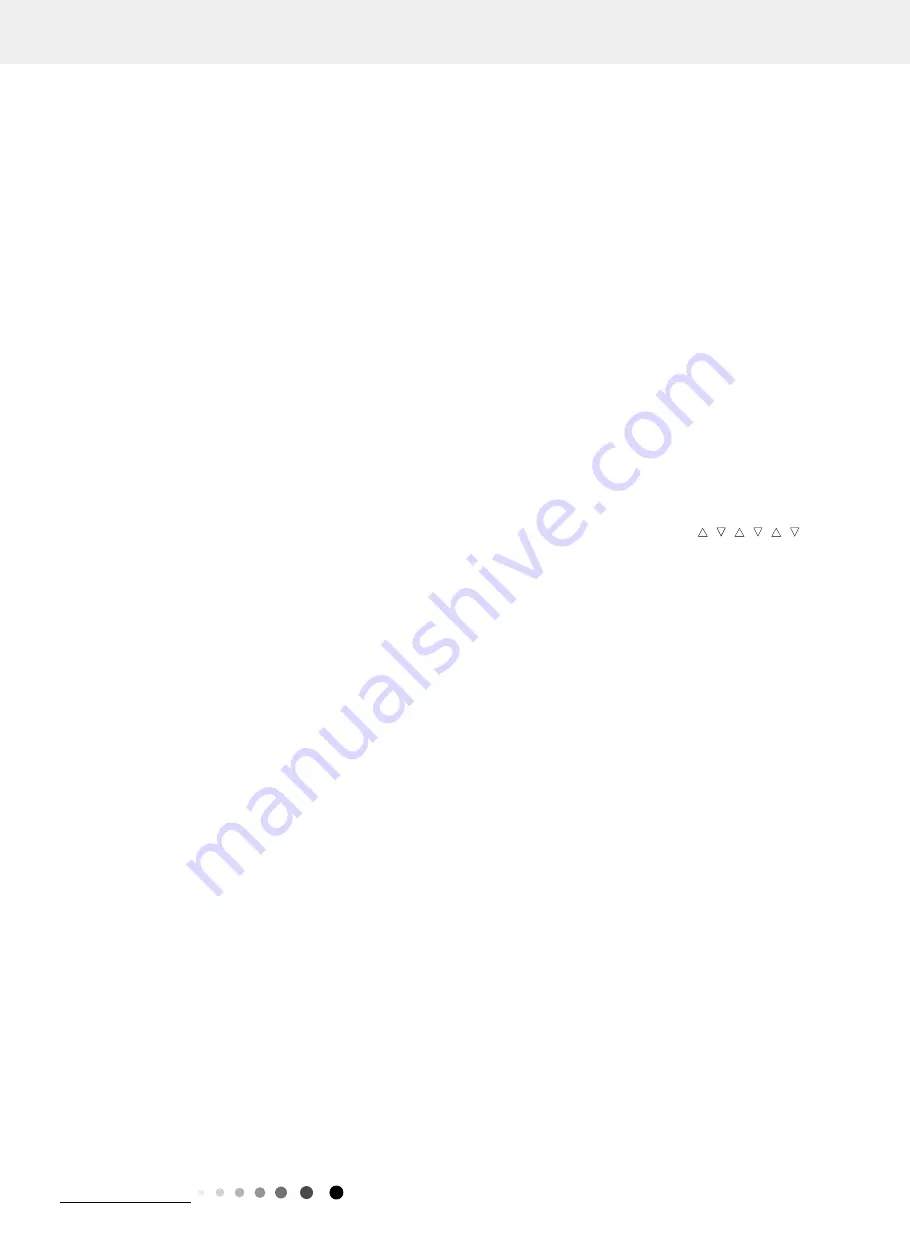
43
Technical Information
After power recovery, compressor can only be started up after
180+T s at least.
(13) SE control mode
The unit operates at SE status.
(14) X-fan mode
When X-fan function is turned on, after turn off the unit, indoor fan
will still operate at low speed for 2min and then the complete unit
will be turned off. When x-fan function is turned off, after turn off
the unit, the complete unit will be turned off directly.
(15) 8
O
C heating function
Under heating mode, you can set 8
o
Cheating function by remote
controller. The system will operate at 8
o
C set temperature.
(16)Turbo function
Turbo function can be set under cooling and heating modes.
Press Fan Speed button to cancel turbo setting. Turbo function is
not available under auto, drying and fan modes.
●Outdoor Unit
1. Cooling mode:
Working condition and process of cooling mode:
①
When Tindoor ambient temperature≥Tpreset, unit enters into
cooling mode. Indoor fan, outdoor fan and compressor start
operation. Indoor fan operates according to set fan speed.
②
When Tindoor ambient temperature≤Tpreset-2
o
C, compressor
stops operation and outdoor fan will stop 30s later. Indoor fan
operates according to set fan speed.
③
When Tpreset-2
o
C
<
Tindoor ambient temperature
<
Tpreset,
unit operates according to the previous status.
Under cooling mode, 4-way valve is not energized. Temperature
setting range is 16~30
o
C. If compressor stops because of
malfunction in cooling mode, indoor fan and swing motor will work
according to the original status.
2. Drying mode
(1) Working condition and process of drying mode
①
When Tindoor ambient temperature
>
Tpreset, unit will be in
drying mode. Outdoor fan and compressor start operation while
indoor fan will operate at low fan speed.
②
When Tpreset-2
o
C≤Tindoor ambient temperature≤Tpreset, unit
operates according to the previous status.
③
When Tindoor ambient temperature
<
Tpreset-2
o
C,
compressor stops operation and outdoor fan will stop 30s later.
(2) Under drying mode, 4-way valve is not energized. Temperature
setting range is 16~30
o
C.
(3) Protection function: same as in cooling mode.
3. Fan mode
(1) Under this mode, indoor fan can select different fan speed
(except Turbo) or auto fan speed. Compressor, outdoor fan and
4-way valve all stop operation.
(2) In fan mode, temperature setting range is 16~30
o
C.
4. Heating mode
Working condition and process of heating mode:
①
W h e n T p r e s e t - ( T i n d o o r a m b i e n t t e m p e r a t u r e -
Tcompensation)≥1
o
C, unit enters into heating mode. Compressor,
outdoor fan and 4-way valve start operation.
②
When -2
o
C
<
Tpreset-(Tindoor ambient temperature-
Tcompensation)
<
1
o
C, unit operates according to the previous
status.
③
When Tpreset-(Tindoor ambient temperature-Tcompensation)≤-
2
o
C, compressor stops operation and outdoor fan will stop 30s
later. Indoor fan will be in residual-heat blowing status.
④
When unit is turned off under heating mode or changed to other
modes from heating mode, 4-way valve will be power-off 2min
after compressor stops working (compressor is in operation status
under heating mode).
⑤
When Toutdoor ambient temperature
>
30
o
C, compressor
stops operation immediately. Outdoor fan will stop 30s later.
⑥
Under the condition that compressor is turned on, when unit
is changed to heating mode from cooling or drying mode, 4-way
valve will be energized in 2~3mins delay.
Note: Tcompensation is determined by IDU and ODU. If IDU
controls the compensation temperature, then Tcompensation is
determined according to the value sent by IDU to ODU; If
IDU does not control the compensation temperature, then
Tcompensation will default to 3
o
C by the ODU.
5. Freon recovery mode
After the Freon recovery signal from IDU is received, cooling at
rated frequency will be forcibly turned on to recover Freon.
Indoor unit will display Fo. If any signal from remote controller is
received, unit will exit from Freon recovery mode and indoor unit
stops displaying Fo.
6. Compulsory defrosting
If unit is turned on under heating mode and set temperature is
16OC (by remote controller), press “ , , , , , ” within 5s,
unit will enter into compulsory defrosting mode and send the
signal to ODU. When the compulsory defrosting signal from ODU
is received, IDU will exit from the compulsory defrosting mode and
stop sending the signal to ODU.
After ODU receives the compulsory defrosting code, it will start
compulsory defrosting. Defrosting frequency and opening
angle will be the same as in normal defrosting mode. When
compulsory defrosting is finished, the complete unit resumes
original status.
7. Auto mode
Auto mode is determined by controller of IDU. See IDU logic for
details.
8. 8
o
C heating
Set temperature is 8
o
C. Display board of IDU displays 8
o
C. Under
this mode, “Cold air prevention” function is shielded.
If compressor is operating under this mode, fan speed will adjust
according to auto fan speed; if compressor stops operation
under this mode, indoor fan will be in residual-heat blowing status.
When power on, communication light will be blinking in a
normal way (after receiving a group of correct signals,
blinking stops for 0.2s~0.3s). If theres no communication,
communication light will be always on. If other ODU has
malfunction, communication light will be on for 1s and off for
1s in a circular way.