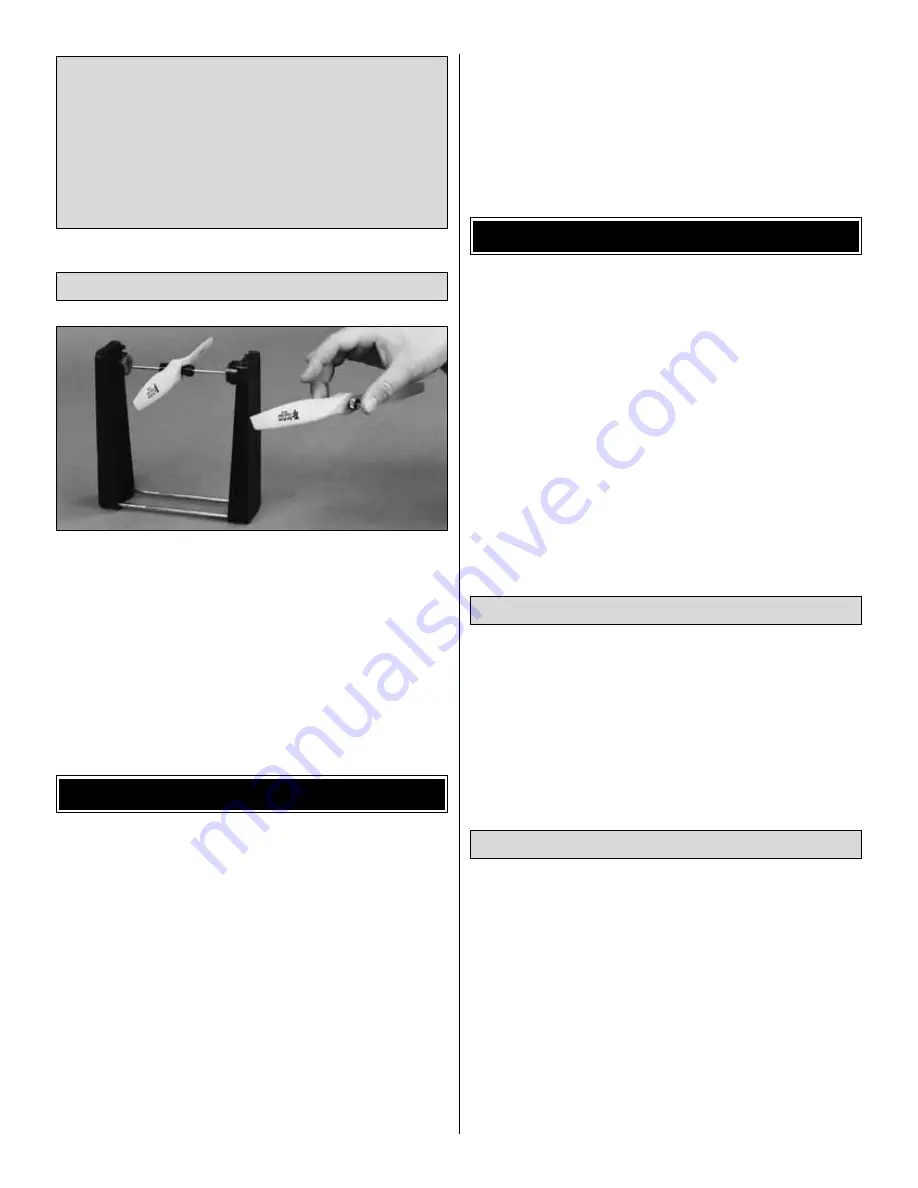
Carefully balance your propeller and spare propellers before
you fly. An unbalanced prop can be the single most
significant cause of vibration that can damage your model.
Not only will motor mounting screws and bolts loosen,
possibly with disastrous effect, but vibration may also
damage your radio receiver and battery.
We use a Top Flite Precision Magnetic Prop Balancer
™
[TOPQ5700] in the workshop and keep a Great Planes
Fingertip Prop Balancer [GPMQ5000] in our flight box.
1. The included motor will benefit from a short “break-in” by
running the motor at full throttle without the propeller for at
least 15 minutes. It is best to run the motor in 5 minute
intervals, allowing the motor to cool between runs. This will
seat the motor brushes on the commutator, insuring that the
motor will provide full power for your first flight and extend
the life of your motor. If you notice a decrease in motor
power after several flights, it may be due to carbon build-up
on the brushes or commutator. To remove this build-up,
repeat the above break-in procedure.
2. The bronze bushings in the motors are self lubricating, but
their life may be extended by applying a very small amount
of light machine oil to the point where the motor shaft
contacts the bushings after every hour or two of run time.
Note: A drop of oil is far too much. You should apply the oil
with a toothpick. Never oil the inside of the motor.
3. Using multiple battery packs to run the motor for
successive flights may cause the motor to become
excessively hot. We recommend at least a 10-minute motor
cool-down period between flights.
1. A new battery pack should be “cycled” for best results. You
should peak charge the battery, then discharge it almost
completely by actually running your motor with the propeller
attached until the auto cut-off stops the motor. To help cool
the battery, remove the battery from the plane. Do this 2 or
3 times on the ground before actually flying. Be sure you
remove the battery from the airplane between each cycle
and allow it and the motor to cool before recharging.
2. Examine your propeller for irregularities caused by the
injection molding process. Carefully remove the imperfections
with fine sandpaper.
After you break-in the motor on the model, inspect the
model closely to make sure all screws remained tight, the
hinges are secure, the prop is secure and all pushrods and
connectors are secure.
Ground check the operational range of your radio before the
first flight of the day. With the transmitter antenna collapsed
and the receiver and transmitter on, you should be able to
walk at least 100 feet [30m] away from the model and still
have control. Have an assistant stand by your model and,
while you work the controls, tell you what the control surfaces
are doing. Repeat this test with the motor running at
various speeds with an assistant holding the model, using
hand signals to show you what is happening. If the control
surfaces do not respond correctly, do not fly! Find and
correct the problem first. Look for loose servo connections or
broken wires, corroded wires on old servo connectors, poor
solder joints in your battery pack or a defective cell, or a
damaged receiver crystal from a previous crash.
Range Check
Ground Check
PERFORMANCE TIPS
PROPER CARE OF YOUR MOTOR
Balance Propellers
CAUTION: Unless the instructions that came with your
radio system state differently, the initial charge on new
transmitter and receiver batteries should be done for 15
hours using the slow-charger that came with the radio
system. This will “condition” the batteries so that the next
charge may be done using the fast-charger of your choice.
If the initial charge is done with a fast-charger the
batteries may not reach their full capacity and you may be
flying with batteries that are only partially charged.
19