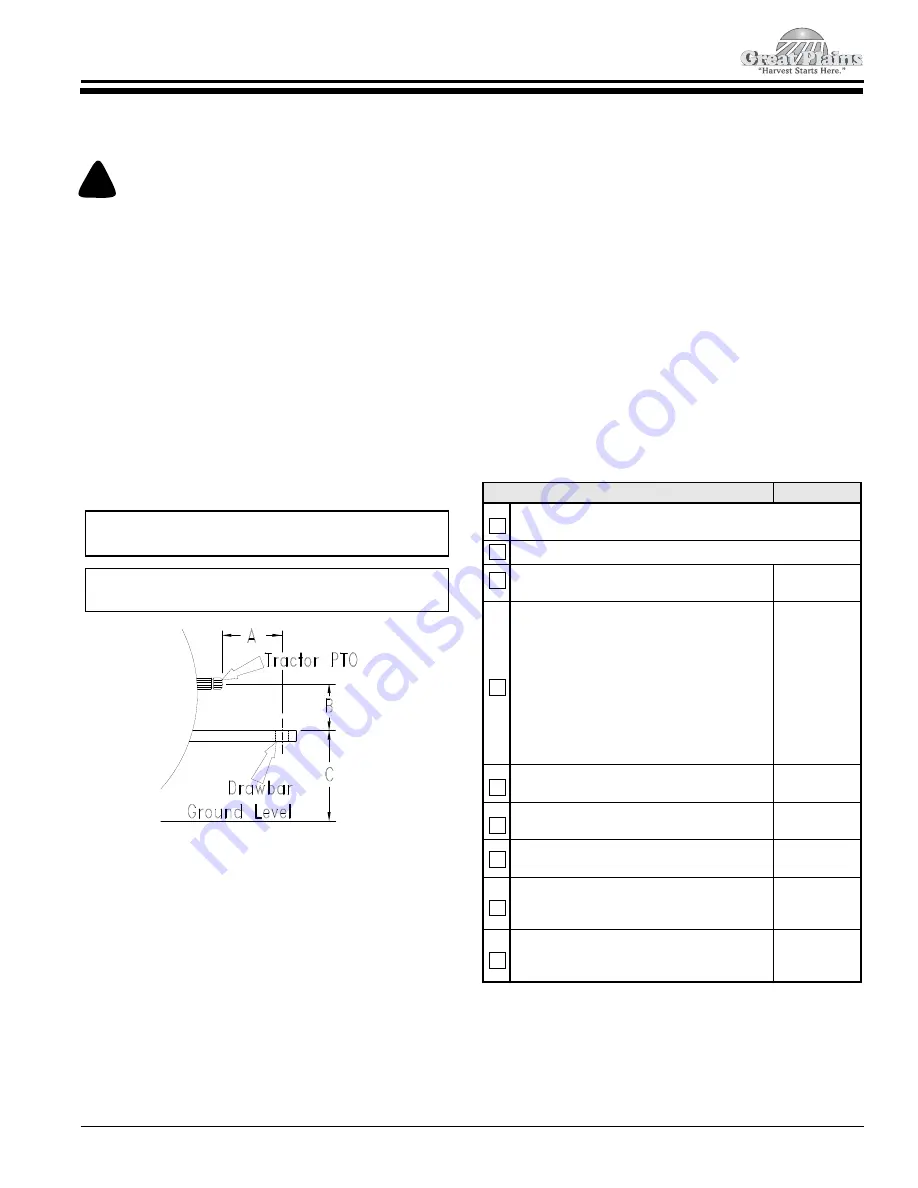
11
Section 1: Assembly & Set-up
9/19/16
RC4015 & RCM4015 Rotary Cutters 334-300M
Section 1: Assembly & Set-up
Tractor Requirements
Horsepower
!
WARNING
Tractor horsepower should be within the range noted
below. Tractors outside the range must not be used.
Horsepower Rating . . . . . . . . . . . . . . . . . . 50-200 HP
Drawbar Set-up
Refer to Figure 1-1:
Maintain proper distance, dimension A, between center
of drawbar hitch pin hole and end of tractor PTO shaft.
Hitch Type . . . . . . . . . . . . . . . . . . . . . . . . . . Draw Bar
540 RPM & 1 3/8", 1000 RPM Rear PTO Speed:
A . . . . . . . . . . . . . . . . . . . . . . . . . . . . . . . . .14"- 16"
B . . . . . . . . . . . . . . . . . . . . . . . . . . . . . . . . . 8" - 10"
C . . . . . . . . . . . . . . . . . . . . . . . . . . . . . . . . 18" - 22"
PTO to Drawbar Distance
Figure 1-1
PTO Speed
Rear PTO Speed:
Model RC4015 . . . . . . . . . . . . . . . . . . . . . 540 RPM
Model RCM4015 . . . . . . . . . . . . . . . . . . .1000 RPM
Hydraulic Outlets
The number of tractor hydraulic duplex outlets is
dependent upon how the Rotary Cutter is set-up.
•
Two duplex outlets are required if the wings are folded
up and down simultaneously. (Factory standard)
•
Three duplex outlets are required if the wings are
folded up and down independently.
•
Float position is highly recommended for the wings.
IMPORTANT:
PTO damage may occur if distances
“A” and “B” are not properly maintained.
IMPORTANT:
A PTO adaptor should not be used.
Using a PTO adaptor can damage the PTO.
22273
If the tractor does not have the necessary number of
duplex outlets, there are control valve kits available to
add outlets. See
for a complete description of this kit.
Before You Start
Read and understand the Operator’s Manual for your
cutter. An understanding of how it works will aid in the
assembly and setup of your cutter.
It is best to go through the
Pre-Assembly Checklist
before assembling the cutter. Speed up your assembly
task and make the job safer by having all needed parts
and equipment readily at hand.
Torque Requirements
“Torque Values Chart for Common Bolt Sizes”
page 56 to determine correct torque values when
tightening hardware. See
bottom of chart for exceptions to common torque values.
Assembly Checklist
Check
Reference
Have a fork lift or loader with properly sized chains and safety
stands capable of lifting and supporting the equipment on hand.
Have a minimum of two people available during assembly.
Make sure all major components and loose
parts are shipped with the machine.
Operator’s
Manual
Double check to make sure all parts, fasteners,
and pins are installed in the correct location.
Refer to the Parts Manual if unsure. By double
checking, you will lessen the chance of using a
bolt incorrectly that may be needed later.
NOTE:
All assembled hardware from the
factory has been installed in the correct
location. Remember location of a part or
fastener if removed during assembly. Keep
parts separated.
Operator’s
Manual
334-300M
Parts Manual
334-300P
Make sure working parts move freely, bolts are
tight & cotter pins are spread.
Make sure all grease fittings are in place and
lubricated.
Make sure all safety labels are correctly
located and legible. Replace if damaged.
Make sure all red and amber reflectors are
correctly located and visible when machine is
in transport position.
Make sure all pneumatic tires are properly
inflated and all wheel bolts and axle nuts are
tightened to the specified torque.