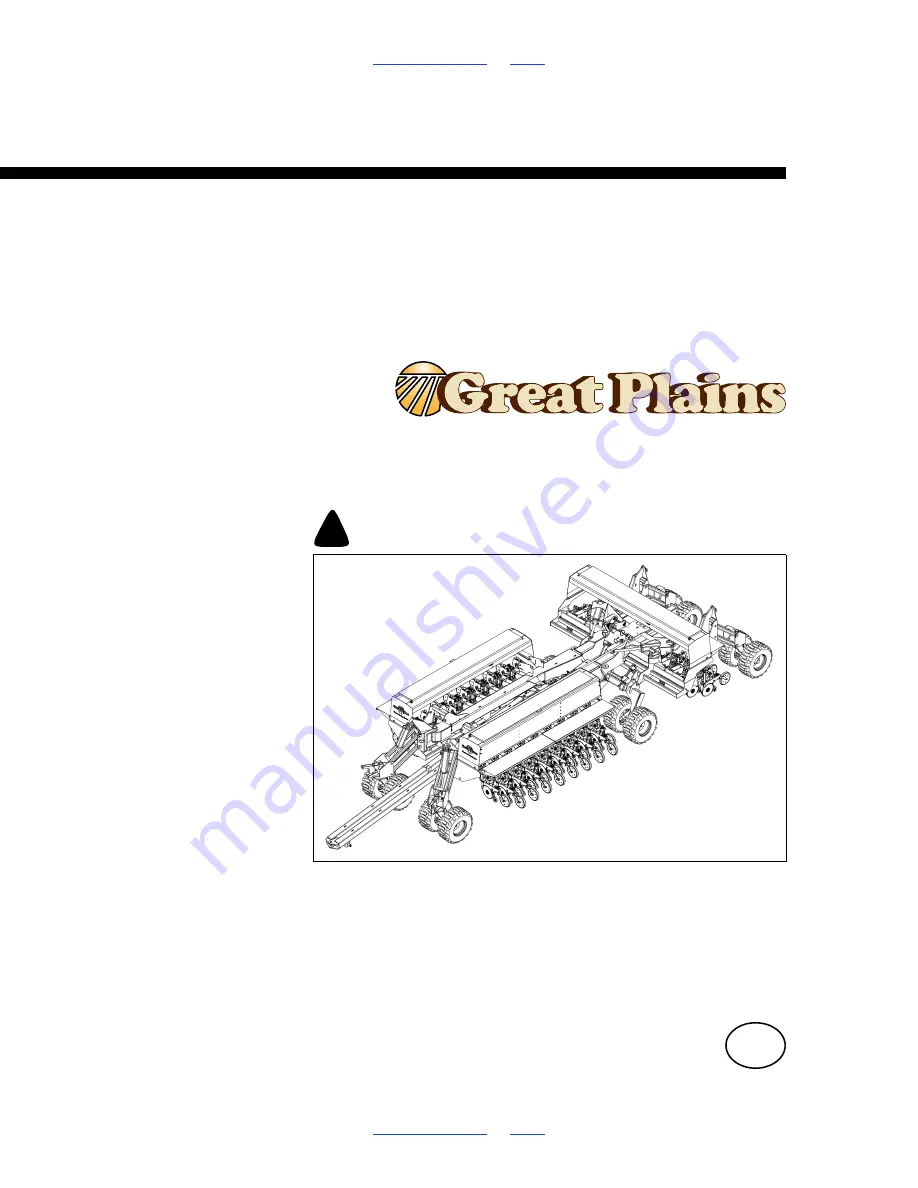
Manufacturing, Inc.
www.greatplainsmfg.com
© Copyright 2019
Printed 2019-03-14
196-538M
EN
ORIGINAL INSTRUCTIONS
Operator Manual
3N-4010P, 3N-4010HDP, 3N-4020P and 3N-4025P
2014+
3-Section 40-Foot No-Till Precision Drills
Read the operator manual entirely. When you see this symbol, the subsequent
instructions and warnings are serious - follow without exception. Your life and
the lives of others depend on it
!
Illustrations may show optional equipment not supplied with standard unit or
may depict similar models where a topic is identical.
!
20293