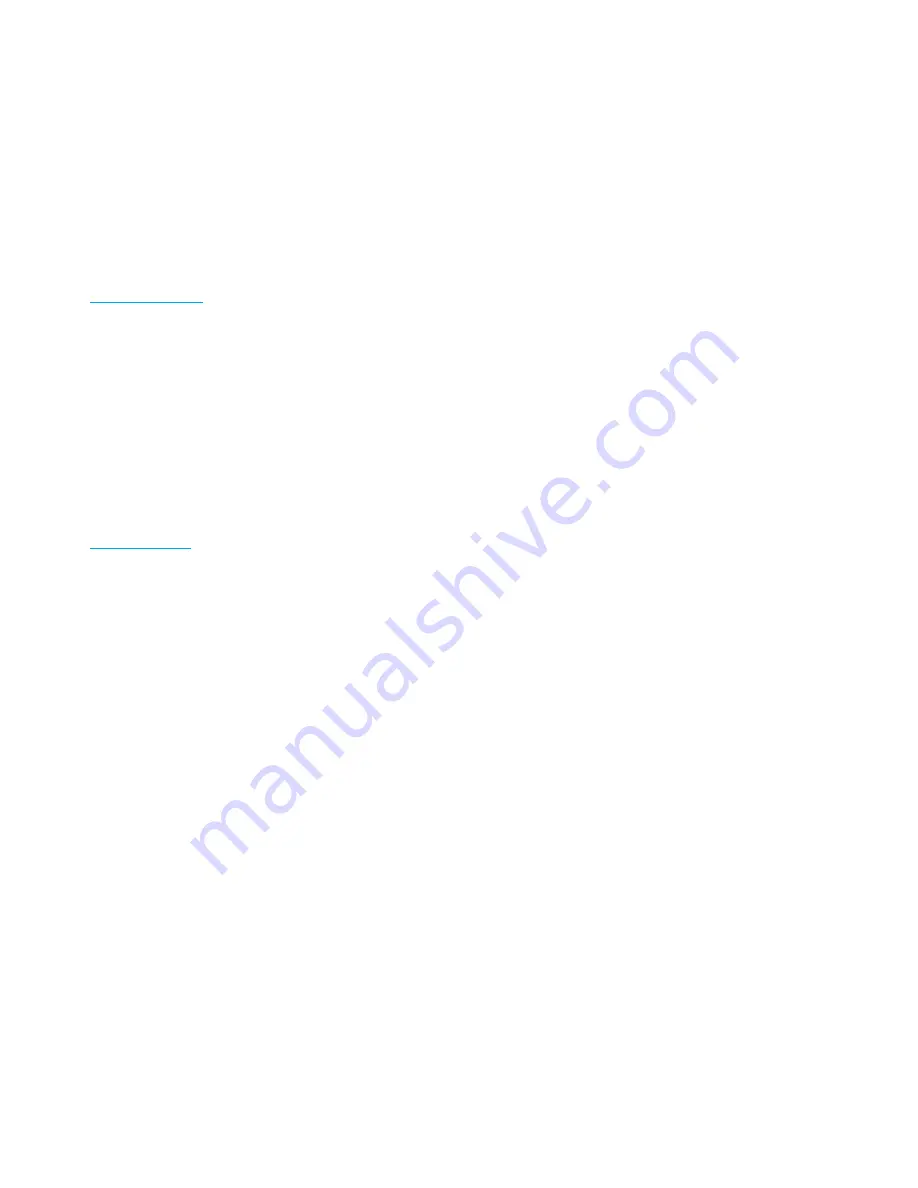
Page 4 GCR Class 8B
Page 4 GCR Class 8B
Ÿ
Detailed step-by-step instructions with the drawings extracted from the CAD originals
The original CAD drawings were prepared from GA drawings obtained from MOSI in Manchester and scaled at 12” to 1’. During
the design process a number of compromises had to be made (such as the frame widths) because of the materials and parts
available to the modeller and the P4 and EM standards. These compromises were used to draw a full size CAD drawing which
was then used to provide the instructions and construction drawings and the final etch parts. The etch parts of the drawing
were scaled down very accurately to produce etches for the 4 mm modeller.
The kit prototypes were built by the designer. The first trial etch was used as a feasibility project and to write outline
instructions. The second test etch was used to test the assembly, write instructions and produce the assembly diagrams as well
as a viable model. A modeller familiar with etch brass kit construction should be able to build an accurate model if these
instructions are followed, generally as written. However, fine-scale modellers being who we are, other ways of building the kit
will be tried!
The Instructions
More years ago than I care to remember I was involved in validating and writing Master Work Sheets for the Royal Air Force.
These were sets of instructions that had to be followed to the letter by technicians world-wide even though they may never
have met that particular piece of equipment before. Deviations were never permitted to the technicians – given that the
machines being tested were vital to safe flying – and any permission to be deviant granted by senior authority was subject to a
very close monitoring process.
However, senility and pending obsolescence have taken their toll – nobody is perfect – so if you find anything in these
instructions you feel to be wrong it will be examined closely and amended where appropriate. Likewise, with the measurements
of the parts, if there is something which you feel may be wrong then, please let me know. It would be nice if this was supported
by drawings, or copies of drawings with time stamps if possible. Photographs are useful as well. But be warned, the available
drawings are neither consistent nor accurate if my research means anything at all and there were so many cosmetic changes
made to these locomotives over nearly 50 years that photographs without a date stamp must be treated with some caution.
Things to note
In a few areas there are alternative ways of doing things. While there are traditional etched springs on Sheet 3, for this kit the
centre springs have been printed using 3D CAD technology. They are fitted to the horn blocks. Note that these are heat sensitive
and will melt as quickly as white metal castings. The etched or printed springs mean that the wheels can also be removed for
‘servicing’.
Continuous Springy Beams (CSBs) may be fitted - they seem to be all the vogue these days. I am a little uncomfortable with the
idea for a complex wheelbase such as a 4-4-2 and prefer to stick with the prototype idea where each axle is sprung by itself.
Short handrail knobs are used for the spring mounts. EM and ‘00’ modellers may use frame blanks to remove the need for
springing.
Stephenson’s Valve Gear would have been visible only by looking very carefully, for this engine. Extra parts are provided so you
can experiment with the way it fits together. If you are tempted to try this then please do remember not to solder the parts in
situ
‘after’
you have fitted your plastic centred wheels. The valve gear may be fitted in working order or as a very loose fit on the
centre axle. In the second case they will be visible but will not move except around the axis of the axle.
The Stephenson’s Valve Gear is tricky to get working well and may be left out. The rest of the engine will still look good when
finished and painted.
The builder will find an array of brake parts on the fret. While 3D brakes are an option and remove the possibility of shorts while
fitting closely to the wheels, they are vulnerable to handling errors. However, there are ways to strengthen them with the etch
base parts, or the builder may use etch parts only.
Rear and centre frame spacers - those supplied on the etch are to scale and may be fitted if desired - you can create frame
spacers which are a good representation of the originals with their strengthening brackets but these are difficult to see when
the model is completed. In practice the rear spacer construction was used to steady the front of the fire box but this may be
omitted without weakening the whole chassis. P4 and EM versions of these spacers are supplied together with some generic
spares. These are not standard widths though. Use the spares in appropriate places if you do not need the scale spacers or wish
to add your own parts for additional electrical pick-up.
There is substantial current collection capability in the tender. I was persuaded not to have pick-ups in the locomotive since they
would detract from the scale frame spacers and the valve gear and since there is plenty of space in the tender with or without
the optional DCC chip this may be a good option. The two wires for the motor may then represent the vacuum and heating
pipes.