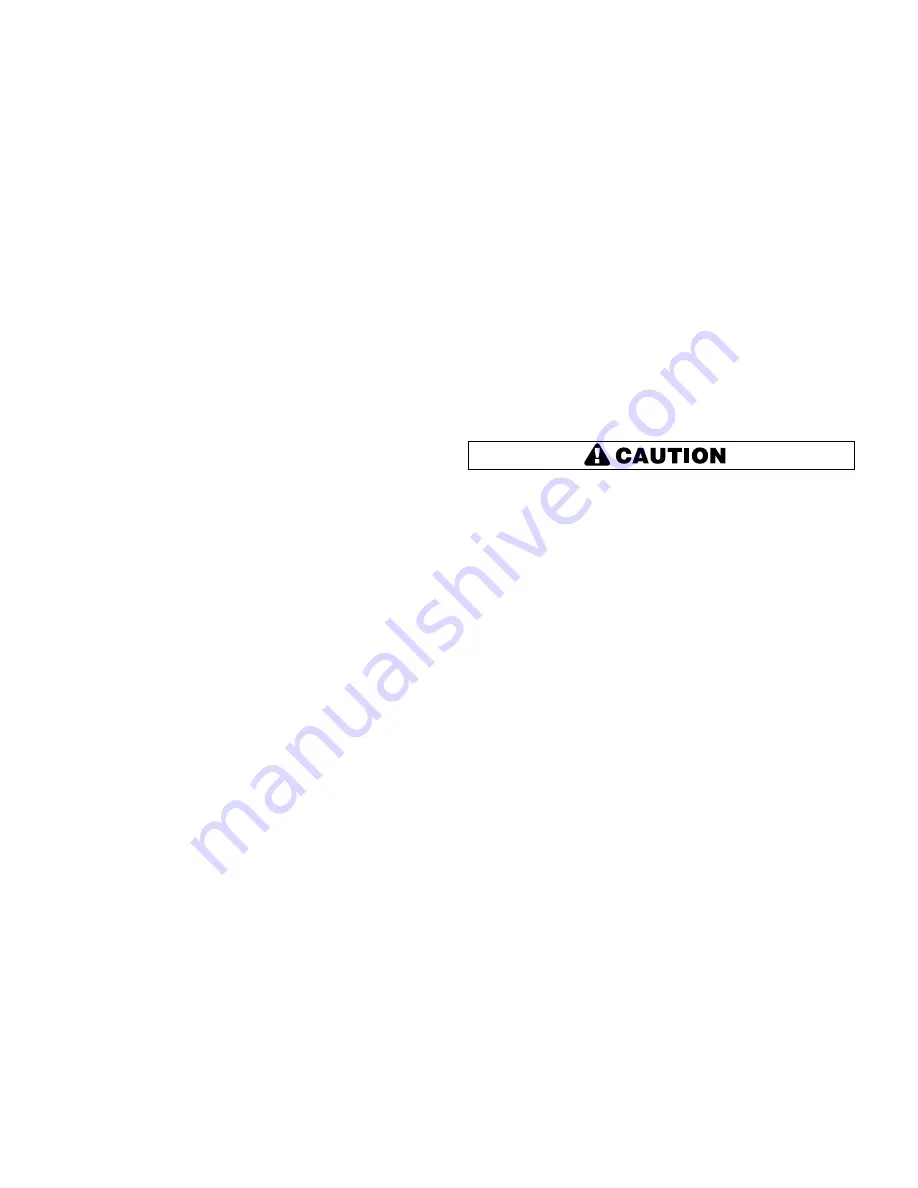
For portable installation, remove threaded levelers and
replace with heavy-duty dual wheel swivel casters
(provided).
• Connect the 3/8" clear suction skimmer hose to the
inlet strainer basket and clamp.
• Connect 1" oil discharge hose to clean coolant outlet on
side of OSEP-2 tank. Hoses have been provided in 10
foot lengths. Do not exceed 10 feet. However, if all
your sumps can be serviced with shorter suction and
discharge hoses, cut hoses as short as possible for opti-
mum performance.
• Close all system drain valves.
• Make sure clear inlet strainer gasket is in place and
bowl is secure.
• Open fluid conditioning filter vessel. Make sure filter
cartridge is securely in place.
• Lift the oil intake nozzle (orange and blue) straight up
even with top.
• Fill the coalescing chamber and fluid conditioning filter
vessel (approximately 17 US gallons) with fresh charge
of coolant used for normal machining operation.
• Close fluid conditioning filter vessel and tighten wing
nuts.
• Open black cap on auto air bleeder on fluid condition-
ing filter vessel lid.
• Be sure that machine tool sump/tank is full (especially
on low profile coolant tanks).
• Locate floating skimmer in coolant sump/tank as close
to machine tool discharge as possible. Use the handy
hose spring clamp to stabilize and/or secure the floating
skimmer in place. Be sure the skimmer is floating with
the proper side up and is level to assure optimum flow
through the OSEP-2 system.
• Clamp the return hose to the sump/tank, as far away
from the skimmer as possible. Be sure to leave an air
gap for positive flow and to provide the best possible
circulation and accelerate turnover.
• Place an oil recovery pail, supplied by customer, under
oil outlet (1/2" hose).
• Close 1/4" ball valve on air regulator.
• Install 1/4" male air fitting on 1/4" ball valve and con-
nect air line. (Air fitting is supplied by customer.)
START UP
• Open 1/4" ball valve on air regulator.
• Be sure regulator is set at 50 psi. Higher or lower pres-
sure will adversely effect system performance. Do not
use an air lubricator.
• Check system for leaks.
• Once system has run for approximately 10 minutes,
adjust oil intake nozzle in coolant sump/tank to approx-
imately 3/16" above coolant level.
BE PATIENT! The OSEP-2 may take several hours or
even days to begin discharging tramp oil. This is due to
the fact that the system must reach its saturation point
based on the amount of tramp oil in each machine.
OPERATION & MAINTENANCE
Turn unit off prior to servicing.
The OSEP-2 is designed to run continuously and unat-
tended. A periodic check of the oil recovery pail is need-
ed to prevent an overflow situation. Use proper judge-
ment when leaving the unit unattended for long periods.
Be sure to follow all federal and local EPA requirements
when disposing of waste oil.
Cycle Times
Cycle times will vary due to tramp oil levels in coolant
tank. Run OSEP-2 until sump is noticeably free of float-
ing tramp oil.
Servicing inlet strainer basket
Periodically remove clear canister on front of unit and
check stainless mesh screen. Wash out and replace, return
to normal operation.
Servicing fluid conditioning filter
Periodically monitor the pressure gauge on the inlet of
the fluid conditioning filter. When the gauge reads 15 psi
change the filter cartridge.
Service instructions:
• Close 1/4" ball valve on air supply.
• Remove wing nuts on the vessel. Remove lid.
• Lift out cartridge and replace.
• Inspect and clean vessel rim gasket.
• Return system to normal operation.
Diaphragm Pump
Refer to manual 795-08691 enclosed with this unit for
pump operation/maintenance. For replacement pump
use DPHG-50 Diaphragm Pump 1/2", 1/1 Hytrel.