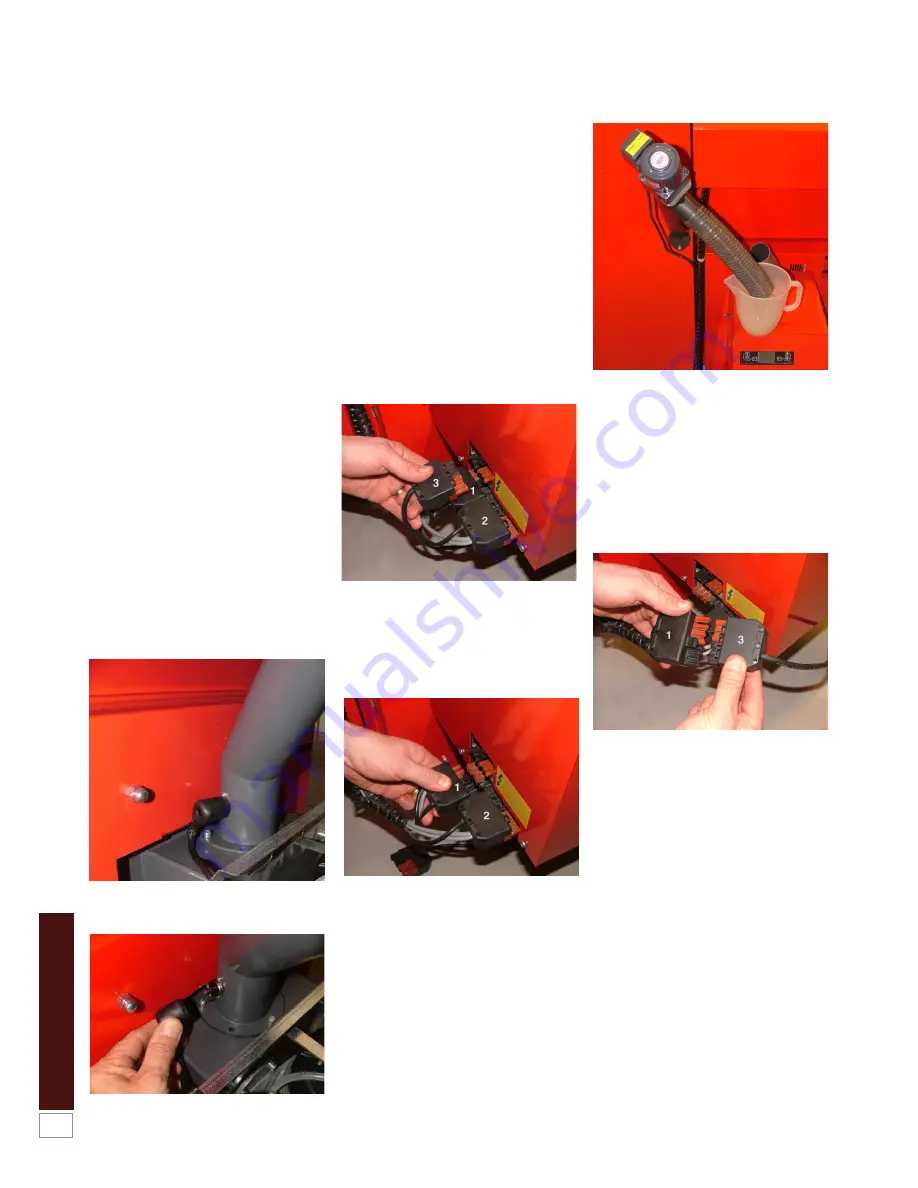
8
6 Pellet Feed Tube
Thermostat
This is a built-in safety device, mounted on
the pellet feed tube (on the top of the burner)
to automatically shut down the burner if the
temperature on the pellet feed tube (between
the pellet auger and the burner) exceeds a
safe level.
If this device should operate, it can be
manually reset once the boiler and pellet feed
tube has cooled down.
To reset:
•
Isolate the electrical supply to the boiler
(set the switch on the fused spur to off).
•
Remove the red burner cover by
loosening the four M5 screws (two on
each side of the cover) and lifting it off
the burner. The thermostat is located on
the pellet feed tube. Refer to Figure 6-1.
•
Disconnect the lead from the thermostat
terminals. Refer to Figure 6-2.
•
Press the reset button located between
the two terminals.
•
Reconnect the lead. Ensure it is fully
pushed on to thermostat terminals.
•
Finally, refit the burner cover and tighten
the four screws.
•
Reconnect the electrical supply to the
boiler and check operation.
NOTE
There is no power present on the two
thermostat terminals when the lead has
been disconnected, so there is no risk of
electrocution when resetting the thermostat.
Figure 6-1: Location of pellet feed tube
thermostat
Figure 6-2: Disconnect lead from pellet tube
thermostat
7 Priming the
Auger
The pellet feed auger on the pellet hopper
MUST be fully primed BEFORE attempting
to start the boiler. The auger should be
initially primed by the Installer as part of the
commissioning process.
If for any reason the auger needs to be re-
primed, this is a simple process using the
following procedure:
Step 1
First set the burner ON/STANDBY switch to
the STANDBY position.
Step 2
Disconnect the pellet feed auger 6-way plug
(3) from the upper socket on the left side of
the burner. Refer to Figure 7-1.
Figure 7-1: Remove plug 3 from burner
Step 3
Disconnect the 7-way plug (1) from
the socket on the left side of the
burner.Refer to Figure 7-2.
Figure 7-2: Remove plug 1 from burner
Step 4
Disconnect the pellet delivery hose from the
pellet feed tube (on the burner) and place the
open end into a DRY container of at least 1
litre capacity. Refer to Figure 7-3.
Figure 7-3: Pellet tube ready for priming the
pellet auger
Step 5
Insert the 6-way plug (3) into the 7-way plug
(1). Refer to Figure 7-4. It is not possible to
connect these two plugs incorrectly as they
will only fit together one way. When these
plugs are connected the pellet feed auger will
run continuously.
Figure 7-4: Connect plugs together
Step 6
Leave the auger running until there is a
continuous flow of pellets from the pellet
delivery hose. This may take 15 to 20
minutes. The pellet feed auger is now fully
primed.
Step 7
Disconnect the two plugs from each other
and the auger will stop.
Refit the pellet delivery hose onto the pellet
feed tube of the burner.
WARNING
Ensure that the pellet delivery hose
forms an air tight seal each end and that
the hose is not damaged. Leakage of
air could cause increased temperature
in the pellet delivery hose and result in
the pellet feed tube thermostat shutting
down the burner.