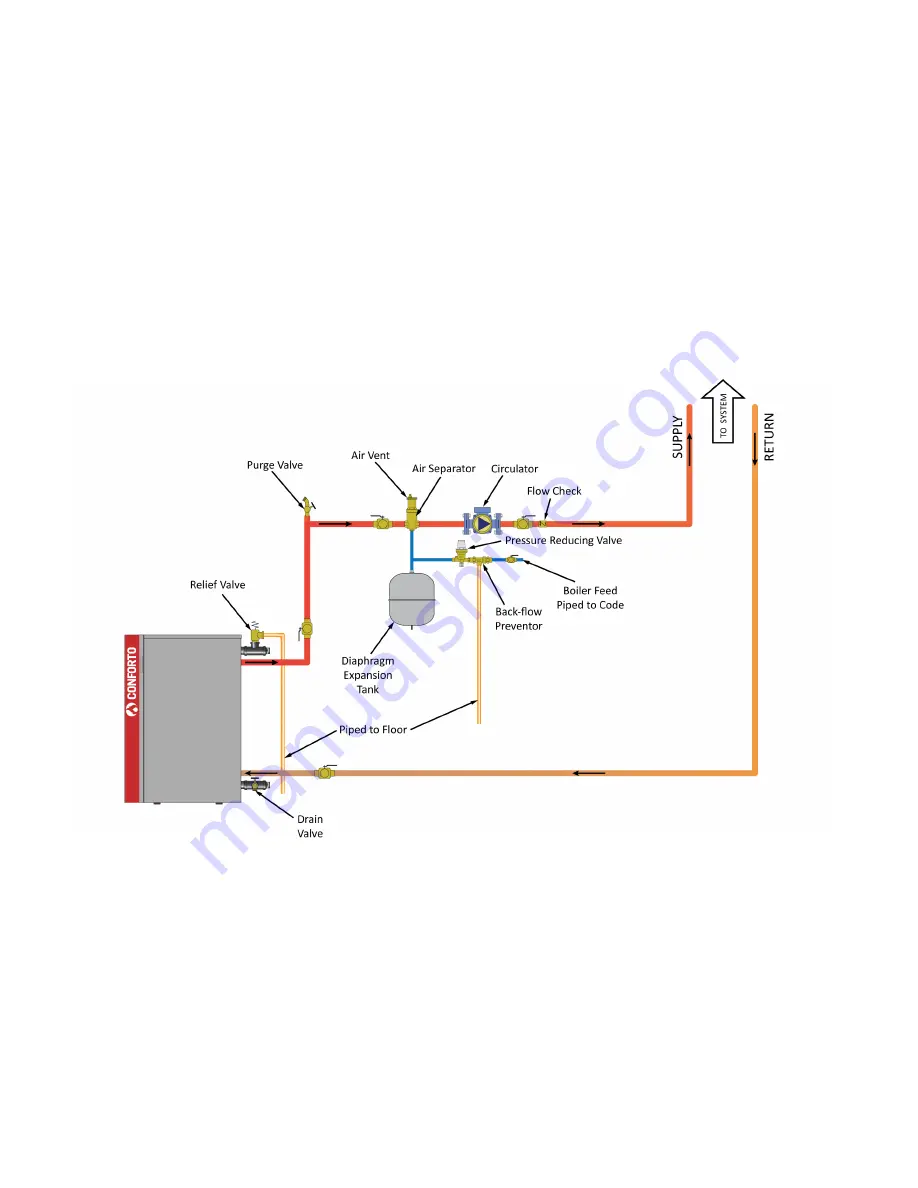
12
Circulation Pump
A calculation for proper pump selection must be performed for all installations. The pump(s)
should not be operated at maximum working pressures above 30 psi or maximum working
temperatures above 200°F and within limits advised by the manufacturer. The pump must not be
operated unless the system has been flushed, bled of all air and completely filled with water.
Recommended locations for the circulator, expansion tank, relief valve and other trim are
shown in Figures 1 - 7.
Figure 1: A typical installation with no domestic hot water and no by-pass
loop installed.
Summary of Contents for Cast Iron Boiler Series
Page 26: ...26 10 3 HYDROSTAT 3250 CONTROL Setting the control...
Page 27: ...27...
Page 30: ...30 12 0 EXPLODED PARTS VIEW...