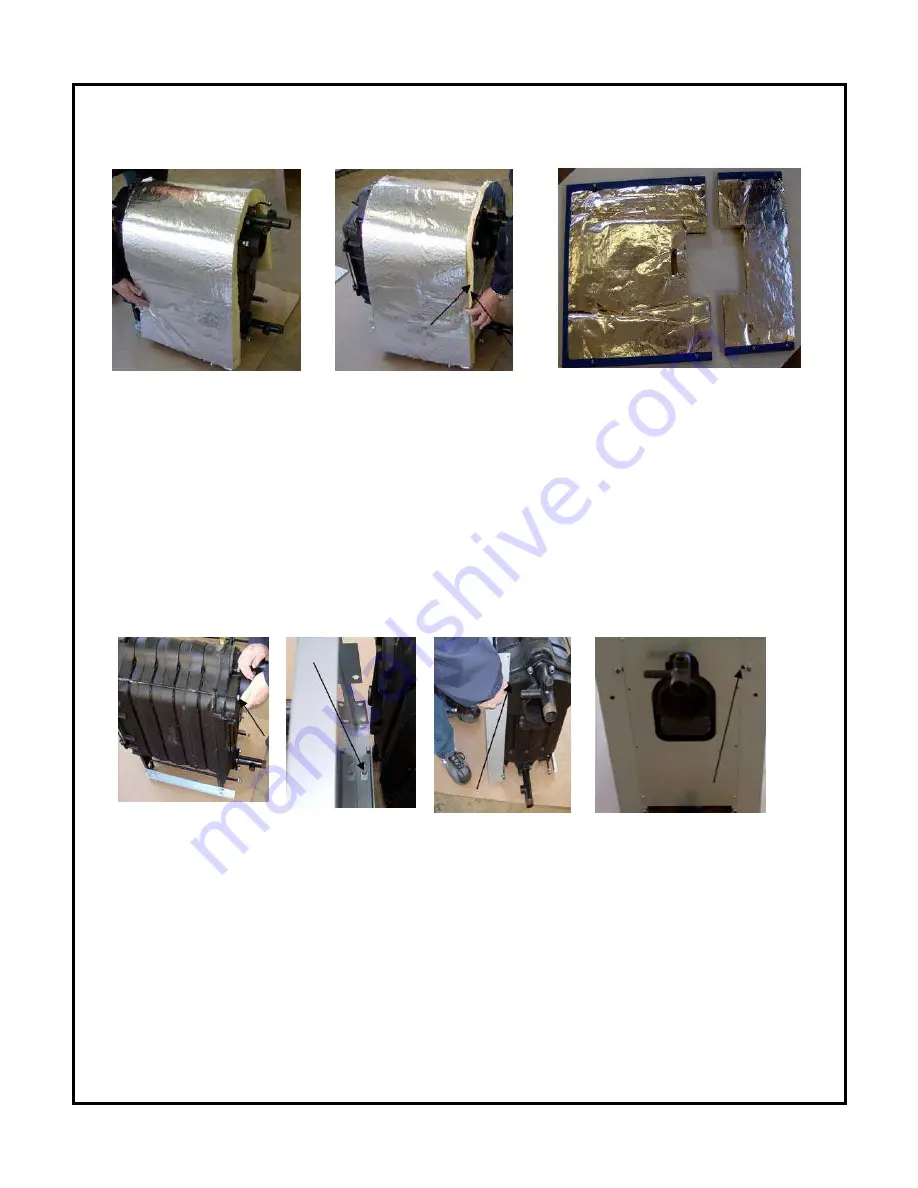
6
STEP 4: INSULATION INSTALLATION
Drape the large piece of block insulation directly over the block taking care to provide adequate
clearance from frame rails. Using the aluminum faced tape attach the preshaped rear
inslulation to the block insulation. The process is simply taping the two pieces together. The
front panels come pre-insulated.
STEP 5: SIDE AND BACK PANEL ATTACHMENT
Affix panel mounting nuts to the rear of the tie rods. Mount the side panels by placing the
panel over the frame rail so that the hole in the bottom lip of the panel fits directly over the
jacket affixing screw on the rail. You can then lock the panel in place by sliding it slightly
forward. The slot on the rear of the panel will now be in position to slide over the tie rod at the
rear of the boiler. Tighten the nuts on the tie rod end to firmly secure the panel. Repeat on the
other side. Screw the back panel to the side panels.
Summary of Contents for B*C-3 sections
Page 25: ...24...
Page 26: ...25 Trouble Shouting the HydroStat 3250...
Page 29: ...28 13 0 EXPLODED PARTS VIEW Exploded Parts View...