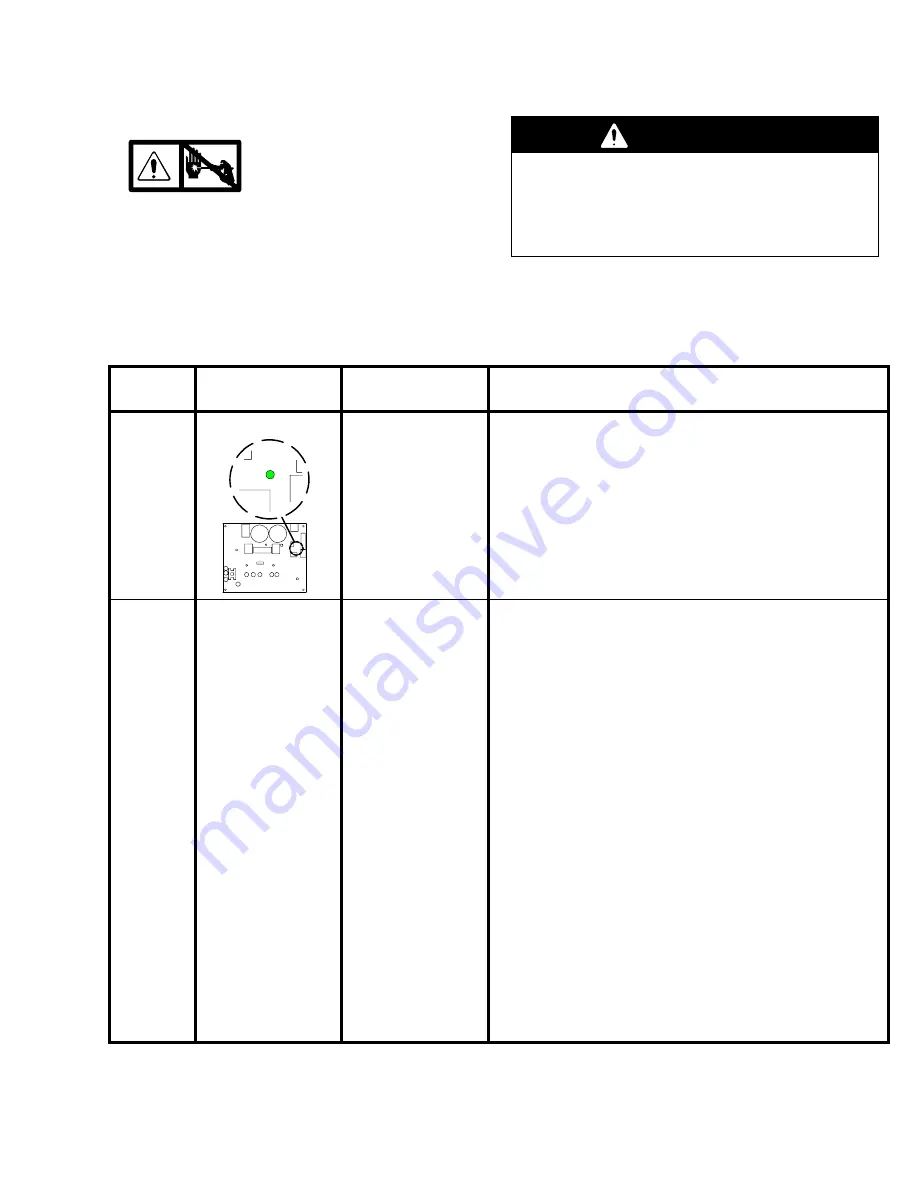
7
309942
Troubleshooting
Electrical
Symptom: Sprayer does not run or stops running
D
Relieve pressure
;
page 5.
D
Plug sprayer into correct voltage, grounded outlet
D
Set power switch OFF for 30 seconds and then ON
again. This ensures sprayer is in normal run mode.
D
Turn pressure control knob up 1/2
D
View digital display
WARNING
To avoid electrical shock or moving parts hazards
when covers are removed for troubleshooting, wait
30 seconds after unplugging power cord for stored
electricity to dissipate. Keep clear of electrical and
moving parts during troubleshooting procedures.
D
If no digital display is available, use control board
status light to troubleshoot problems: Turn ON/OFF
switch OFF, remove control cover and then turn
power back ON. Observe status light.
DIGITAL
DISPLAY
CONTROL BOARD
STATUS LIGHT
INDICATION
WHAT TO DO
Blank
Never lights
LED
100
No power to control
board
1.
Verify required voltage is present
2.
Check wiring connections to control board
3.
Perform continuity check on power cord and switch.
Replace power cord or switch as needed.
4.
If steps 1 – 3 are ok, replace control board
–––– psi
Blinks once and
stops
No RUN command
to control board.
Potentiometer or
transducer problem
1.
Make sure prime valve is open and there is no pres-
sure in the system
2.
Turn pressure control knob clockwise
3.
Check potentiometer connection to control board
4.
Check pressure control knob alignment to potentiom-
eter shaft. Turn shaft fully clockwise and attach knob
in full ON position.
5.
Unplug potentiometer. Short out center pin of control
board potentiometer connector to each outer pin (one
at a time). If sprayer runs, replace potentiometer.
6.
Check transducer connection
7.
Disconnect and reconnect transducer plug to ensure
good connection with control board socket. Check
that transducer contacts are clean.
8.
Open prime valve. Connect a known good transducer
in place of the sprayer transducer. Set sprayer ON.
Replace transducer If sprayer runs. Replace control
board If sprayer does not run.