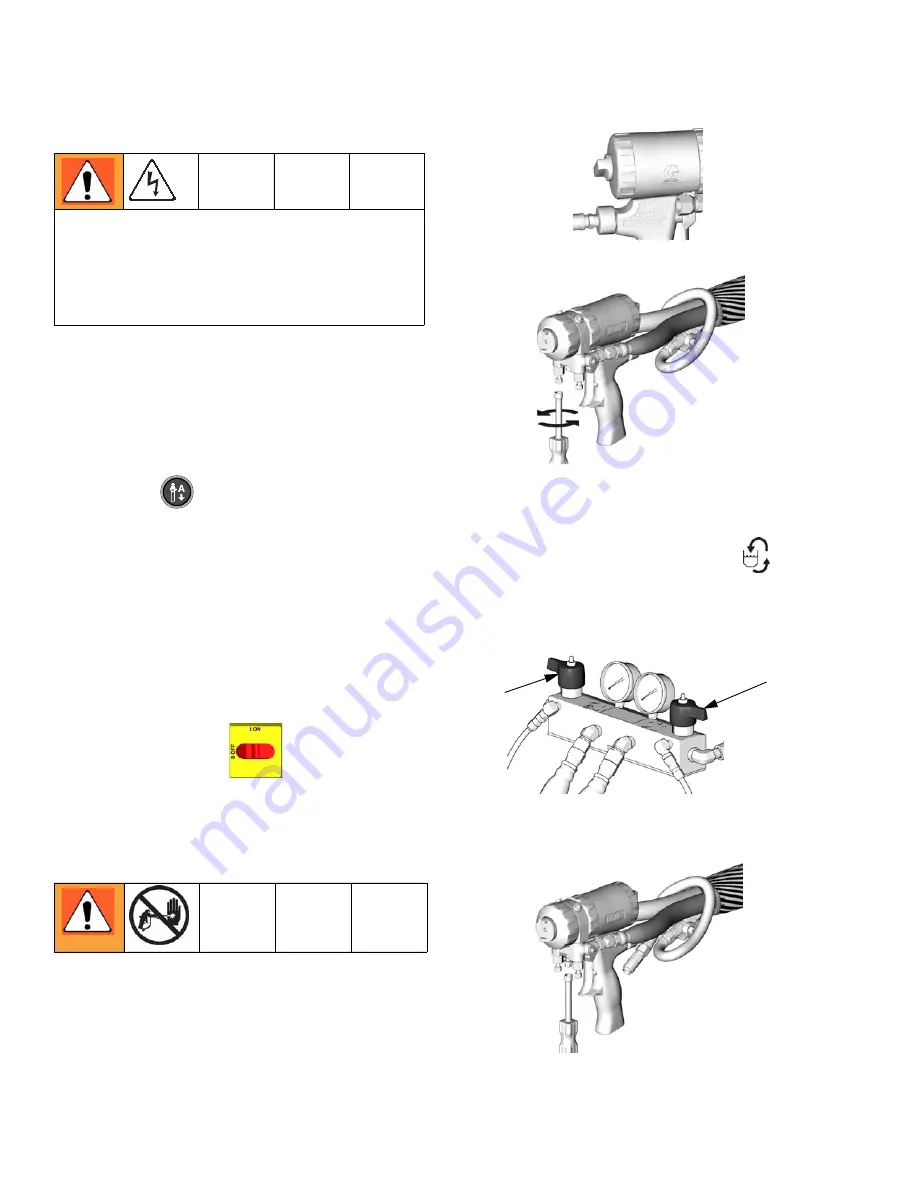
Repair
26
312066ZAD
Repair
Before Beginning Repair
1.
Flush if necessary; see Flushing.
2.
Park component A pump.
a.
Press
.
b.
Trigger gun until pump A stops. After fluid pres-
sure drops below 700 psi (7.9 MPa, 79 bar),
motor will run until component A pump is at bot-
tom of its stroke, then shut off.
c.
Check ISO reservoir for component A pump. Fill
wet cup on component B pump. Refer to Reac-
tor Operation manual 312065.
3. Turn main power OFF
.
4.
Relieve pressure.
Pressure Relief Procedure
1.
Relieve pressure in gun and perform gun shutdown
procedure. See gun manual.
2.
Engage gun piston safety lock.
3.
Close gun fluid manifold valves A and B.
4.
Shut off feed pumps and agitator, if used.
5. Turn PRESSURE RELIEF/SPRAY valves (SA, SB)
to PRESSURE RELIEF/CIRCULATION
. Route
fluid to waste containers or supply tanks. Ensure
gauges drop to 0.
6.
Disconnect gun air line and remove gun fluid mani-
fold.
Repairing this equipment requires access to parts
that may cause electric shock or other serious injury if
work is not performed properly. Have a qualified elec-
trician connect power and ground to main power
switch terminals, see operation manual. Be sure to
shut off all power to the equipment before repairing.
ti2409a
ti2421a
SA
SB
ti2554a