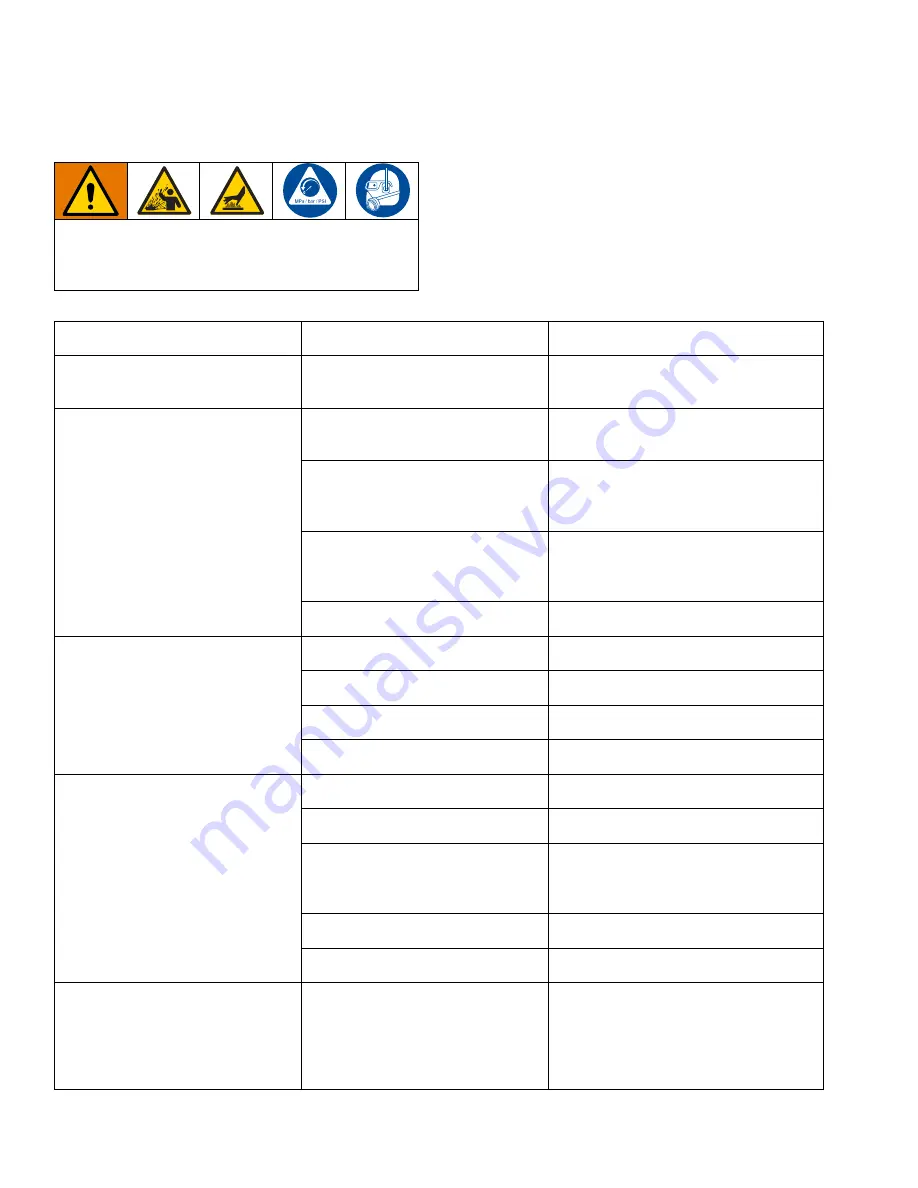
Troubleshooting
14
3A4238B
Troubleshooting
•
Relieve the pressure before checking or servicing
the equipment.
•
Check all possible problems and causes before dis-
assembling the pump.
To reduce the risk of serious injury, whenever you
are instructed to relieve pressure, always follow
the
on page 12.
PROBLEM
CAUSE
SOLUTION
Pump cycles at stall or fails to hold
pressure at stall.
Worn check valve balls (301), seats
(201) or o-rings (202).
Replace. See page 18.
Pump will not cycle, or cycles once
and stops.
Air valve is stuck or dirty.
Disassemble and clean air valve. See
page 16. Use filtered air.
Check valve ball (301) severely
worn and wedged in seat (201) or
manifold (102 or 103).
Replace ball and seat. See page 18.
Check valve ball (301) is wedged
into seat (201), due to overpressur-
ization.
Install Pressure Relief Valve
(see page 9).
Dispensing valve clogged.
Relieve pressure and clear valve.
Pump operates erratically.
Clogged suction line.
Inspect; clear.
Sticky or leaking balls (301).
Clean or replace. See page 18.
Diaphragm ruptured.
Restricted exhaust.
Remove restriction.
Air bubbles in fluid.
Suction line is loose.
Tighten.
Diaphragm ruptured.
Loose inlet manifold (102), dam-
aged seal between manifold and
seat (201), damaged o-rings (202).
Tighten manifold clamps (113), or
replace seats (201) or o-rings (202).
See page 18.
Loose diaphragm shaft bolt (107).
Tighten or replace (pages 19-21).
Damaged o-ring (108).
Chattering - noisy operation.
Check valve balls do not seat prop-
erly/cleanly due to imbalance
between fluid inlet and outlet line
sizing. Noise is accentuated with
light viscosity fluids.
Reduce size/diameter of inlet line
relative to outline line. Outlet line size
should not exceed pump size.