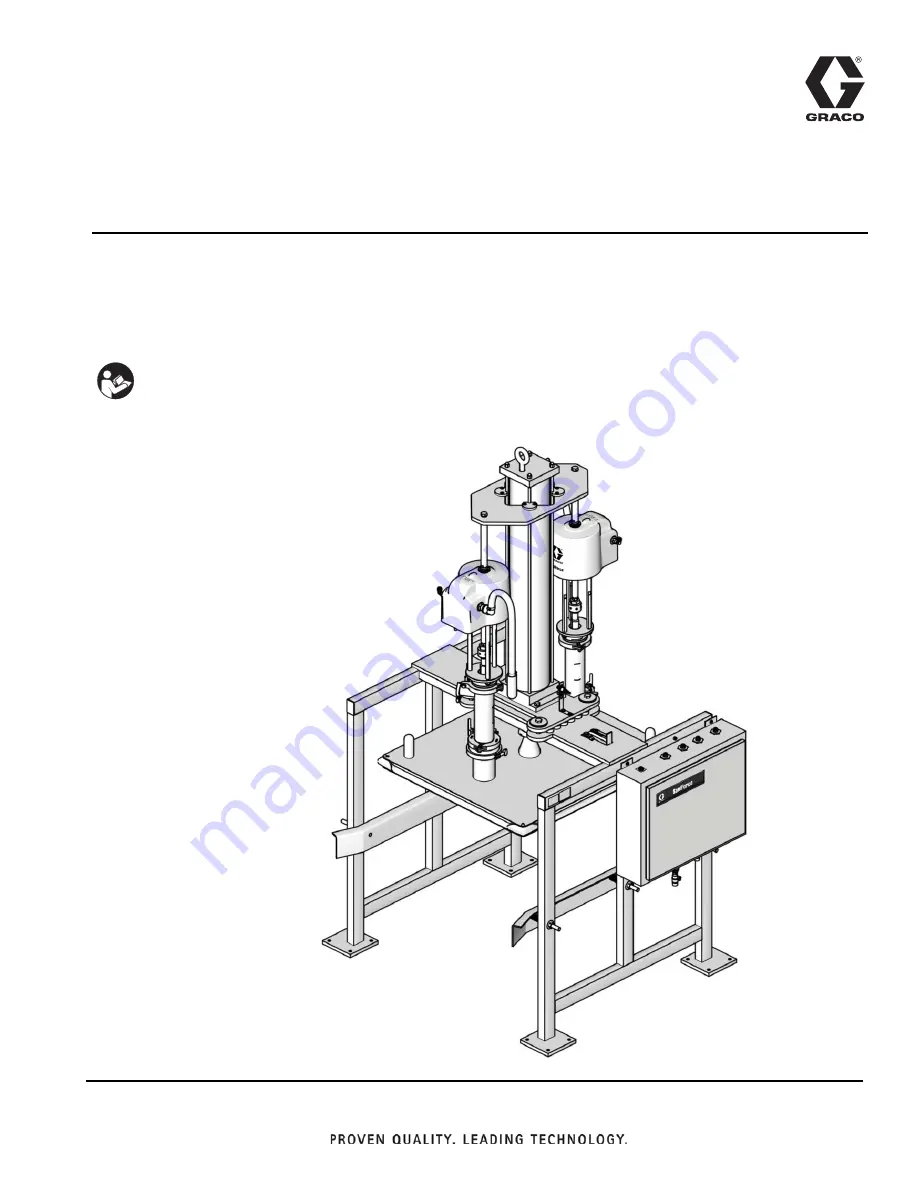
311163ZAH
EN
Instructions-Parts List
SaniForce
™
Bin Evacuation System
For use with 300 gallon (1135 liter) bags in bin containers. For professional use only.
Not approved to European Explosive Atmosphere requirements.
See page 3 for model information, including maximum working pressure and approvals.
Important Safety Instructions
Read all warnings and instructions in this
manual. Save these instructions.
Model BESE1A Shown
ti16236a
Summary of Contents for SaniForce BES Series
Page 4: ...Models 4 311163ZAH ...