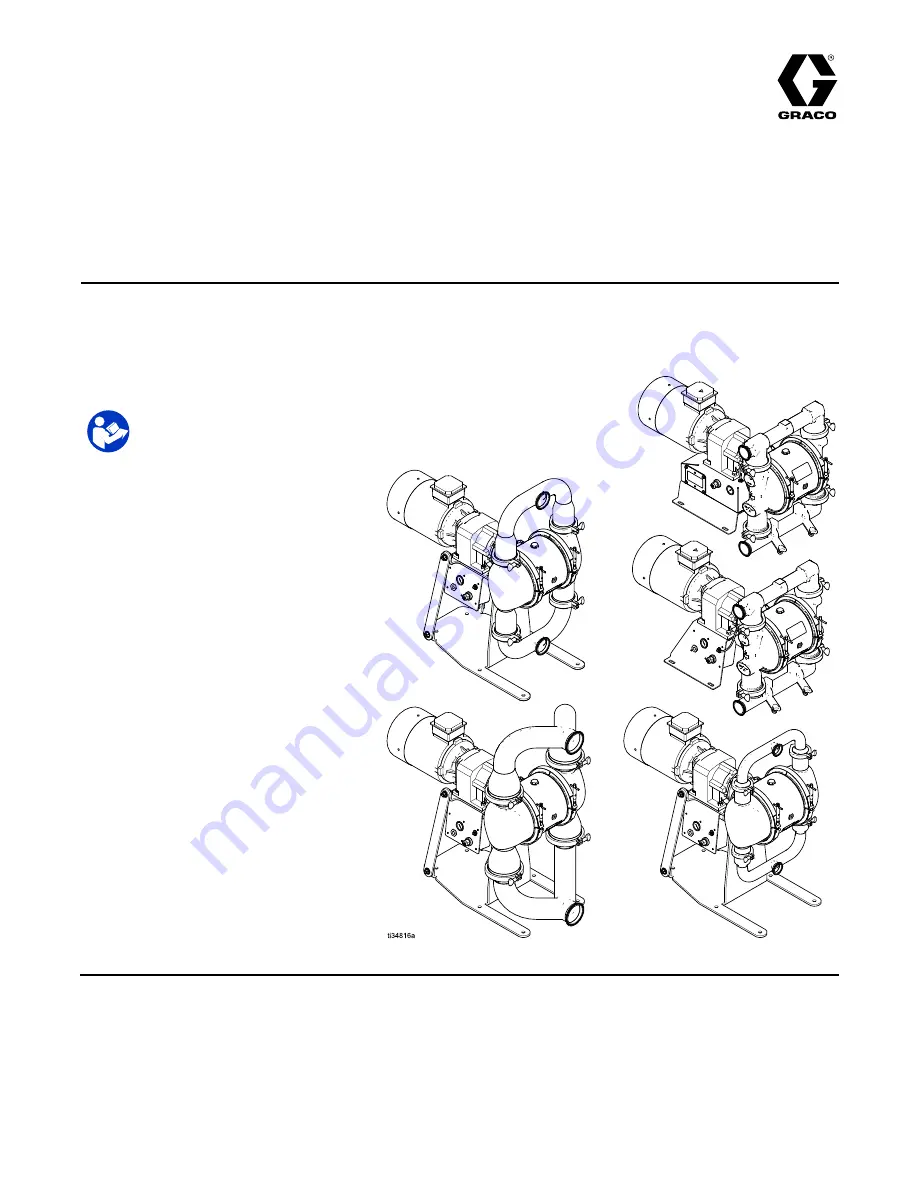
Repair/Parts
SaniForce® 2150, 3000, 4000,
Electric - Operated
Diaphragm
Pump
3A5133J
EN
2
2
2---Inch,
Inch,
Inch, 3
3
3---Inch,
Inch,
Inch, and
and
and 4
4
4---Inch
Inch
Inch pumps
pumps
pumps with
with
with electric
electric
electric drive
drive
drive for
for
for fluid
fluid
fluid transfer
transfer
transfer applications.
applications.
applications.
Not
Not
Not approved
approved
approved for
for
for use
use
use in
in
in explosive
explosive
explosive atmospheres
atmospheres
atmospheres or
or
or hazardous
hazardous
hazardous locations
locations
locations unless
unless
unless otherwise
otherwise
otherwise stated.
stated.
stated. See
See
See
Approvals
Approvals
Approvals page
page
page for
for
for more
more
more information.
information.
information. For
For
For professional
professional
professional use
use
use only.
only.
only.
Important
Important
Important Safety
Safety
Safety Instructions
Instructions
Instructions
Read all warnings and instructions in this manual and in your
Operation manual. Save
Save
Save these
these
these instructions.
instructions.
instructions.
For maximum working pressure, see
Technical Data sheets
See page 7 for approvals.
PROVEN QUALITY. LEADING TECHNOLOGY.
Summary of Contents for saniforce 2150
Page 24: ...Parts Parts Parts Parts 2150T 2150T 2150T Pump Pump Pump 24 3A5133J ...
Page 25: ...Parts 2150HS 2150HS 2150HS Ball Ball Ball Check Check Check Pump Pump Pump 3A5133J 25 ...
Page 26: ...Parts 3000HS 3000HS 3000HS Flapper Flapper Flapper Pump Pump Pump 26 3A5133J ...
Page 27: ...Parts 4000HS 4000HS 4000HS Flapper Flapper Flapper Pump Pump Pump 3A5133J 27 ...